AUTORE | DATA DI CREAZIONE | VERSIONE | NUMERO DEL DOCUMENTO |
---|---|---|---|
Dr. Peter Marshall | 1 Dicembre 2017 | V1.1 | CC11 - 00120 |
Introduzione
Questo documento studia l'influenza dell'esposizione dei riflettori a infrarossi in acciaio alluminato e acciaio inossidabile Ceramicx ad alte temperature sulla riflettività del materiale. Viene effettuato un confronto tra riflettori nuovi e ossidati per valutare l'influenza di questo sul flusso di calore radiativo percentuale.
Materiali
In questo studio sono stati utilizzati due riflettori di forma standard (RAS 1) per elementi ceramici. Una volta era l'acciaio alluminato standard di Ceramicx mentre l'altro era in acciaio inossidabile. Lo stesso 1000W FTE smaltato nero è stato utilizzato in tutti i test.
metodo
I riflettori sono stati collocati nel forno a 600 ° C per 8 ore in condizioni atmosferiche standard. Dopo il riscaldamento, sono stati lasciati raffreddare all'interno del forno fino al freddo. Una volta completato questo processo, un riflettore 1000W nero è stato montato sul riflettore e il flusso di calore è stato registrato usando la procedura standard.
Il robot del flusso di calore Ceramicx Herschel esamina il flusso di calore totale (W.cm-2) che è incidente sul sensore. I riscaldatori possono essere montati nell'Herschel e analizzati utilizzando la routine di mappatura del flusso di calore a infrarossi 3D. Questo sistema automatizzato utilizza un sensore a infrarossi che viene guidato roboticamente attorno a un sistema di griglia di coordinate predeterminato davanti all'emettitore del riscaldatore in prova. Il sensore ha un livello di flusso di calore massimo di 2.3 W.cm-2 e misura IR nella banda 0.4-10 micrometri. Il sistema di coordinate è una griglia cubica 500mm di fronte all'emettitore di riscaldamento, vedere la Figura 1. Il robot sposta il sensore con incrementi di 25mm lungo un percorso a serpentina nelle direzioni X e Z, mentre l'emettitore di riscaldamento è montato su un carrello scorrevole che aumenta con incrementi di 50mm lungo la direzione Y.
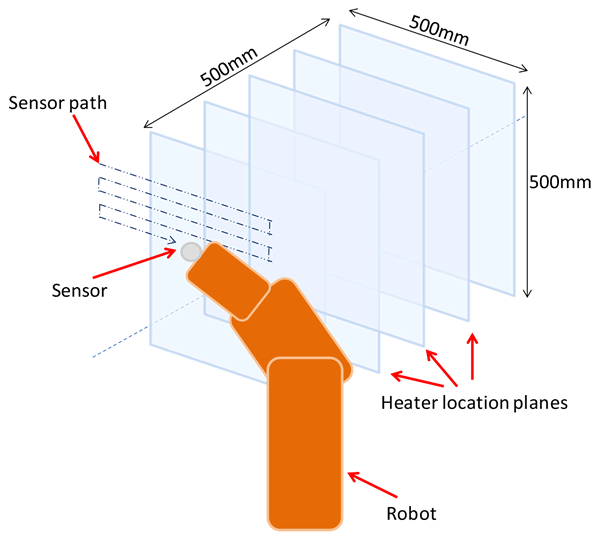
I risultati della macchina possono essere correlati in una percentuale di energia totale consumata restituita come flusso di calore radiante dal riscaldatore. Ciò diminuisce con la distanza dal riscaldatore poiché il flusso di calore radiante diverge dal riscaldatore.
Risultati
Trattamento termico
Dopo il trattamento termico, il riflettore in acciaio alluminato mostrava un'area grigio opaco nella parte centrale del riflettore mentre il riflettore in acciaio inossidabile mostrava un colore blu / viola intenso, come mostrato nella Figura 1, di seguito.
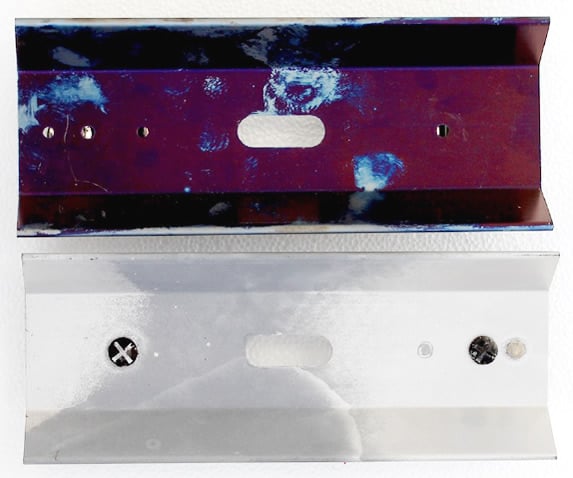
Misura del flusso di calore
I riflettori inutilizzati in acciaio inossidabile e alluminizzato mostrano che il flusso di calore percentuale massimo è registrato a 100mm dall'elemento, come mostrato nella Figura 3 di seguito. I risultati del flusso di calore mostrano che il flusso di calore percentuale registrato è più elevato per il riflettore in acciaio alluminato rispetto al riflettore in acciaio inossidabile, in linea con molta letteratura pubblicata fino ad oggi da Ceramicx e altri.
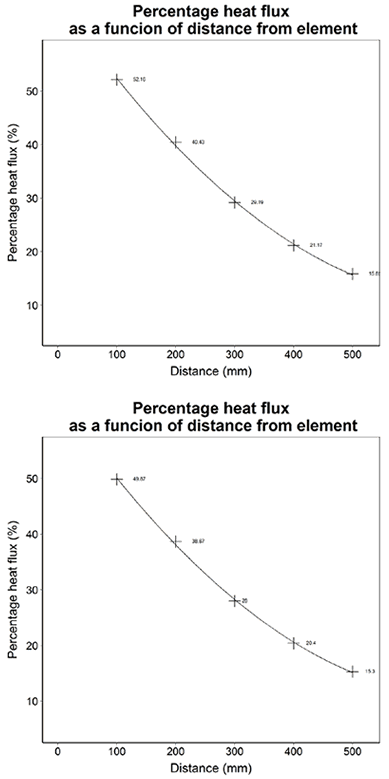
L'esposizione prolungata alle alte temperature provoca l'ossidazione e quindi la caduta del riflettore. Per l'acciaio alluminizzato, lo strato di ossido visibile provoca una riduzione del 18.6%, come mostrato nella Figura 4, di seguito. Per l'acciaio inossidabile, questa riduzione è dell'2%, che rientra ampiamente nei limiti dell'errore sperimentale.
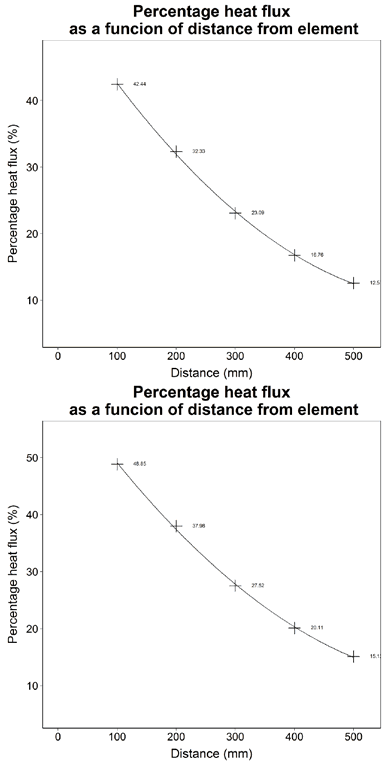
Il flusso di calore di picco per l'acciaio alluminizzato non trattato era superiore a quello dell'acciaio inossidabile. Ciò era previsto, dato che le proprietà riflettenti dell'acciaio alluminato sono migliori dell'acciaio inossidabile. Dopo il trattamento termico, la tabella 1 mostra che il flusso di calore di picco per l'acciaio alluminato è calato drasticamente mentre lo strato di ossido sul materiale assorbe la radiazione infrarossa. Al contrario, il cambiamento di colore per il riflettore in acciaio inossidabile, in linea con la misurazione del flusso di calore percentuale, ha mostrato solo una piccola diminuzione.
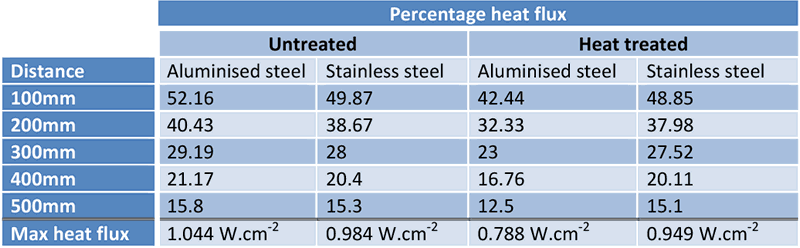
Non sono stati osservati cambiamenti distinti nel modello di emissione dell'elemento. Inoltre, il cambiamento nel flusso di calore, in funzione della distanza, era come previsto.
Conclusione
Come precedentemente dimostrato da Ceramicx, l'uso di un riflettore in acciaio alluminizzato lucido aumenta il flusso di calore radiativo percentuale emesso verso il target di riscaldamento rispetto all'acciaio inossidabile. Per applicazioni a temperature più basse, dove è improbabile che si verifichi ossidazione dell'alluminio, l'acciaio alluminizzato si rivela un materiale dalle prestazioni migliori. Per applicazioni a temperature più elevate, dove è probabile che si verifichi l'ossidazione dell'alluminio, l'acciaio inossidabile è una scelta migliore in quanto porta a una percentuale maggiore di energia radiativa diretta verso il materiale target.
Negazione di responsabilità
Questi risultati dei test devono essere attentamente considerati prima di determinare quale tipo di emettitore a infrarossi utilizzare in un processo. Test ripetuti condotti da altre società potrebbero non ottenere gli stessi risultati. Esiste la possibilità di errore nel raggiungere le condizioni di installazione e le variabili che possono alterare i risultati includono la marca dell'emettitore impiegato, l'efficienza dell'emettitore, la potenza fornita, la distanza dal materiale testato all'emettitore utilizzato e l'ambiente . Anche le posizioni in cui vengono misurate le temperature possono differire e quindi influenzare i risultati.