AUTORE | DATA DI CREAZIONE | VERSIONE | NUMERO DEL DOCUMENTO |
---|---|---|---|
Dr. Peter Marshall | 8 Aprile 2016 | V1.1 | CC11 - 00101 |
Introduzione
CCP Gransden ha contattato Ceramicx per costruire un forno a infrarossi per riscaldare materiali preimpregnati in fibra di carbonio termoplastica per le loro operazioni di formatura. Questo lavoro di test è stato svolto nell'ambito delle funzioni definite nella proposta di vendita (CSP 000 008). La prima fase prevede la valutazione e la selezione del riscaldatore a infrarossi per questo progetto, con la temperatura minima del materiale stabilita di 425 ° C.
Descrizione del materiale
Sono stati ricevuti tre campioni di due materiali in pezzi 230 x 230 x 1mm. In questi casi, la matrice era PEEK1 e PPS2. Un campione più piccolo di PEKK3 con dimensioni di 200 x 150 x 2mm è stato anche ricevuto. Il materiale era rigido, liscio con una finitura nera lucida. Un piccolo motivo era visibile sulla superficie sulla superficie dei campioni PEEK e PPS.
I campioni PEEK e PPS sono stati tagliati in pezzi 115 x 115 mm. Il materiale PEKK è stato tagliato in pezzi 100 x 75mm.
metodo
Sono state valutate due famiglie di riscaldatori distinte; alogeno (QH e QT) e ceramica cava nera (FFEH). In ogni caso, i piani sono stati montati sopra e sotto il campione di materiale con altezza regolabile.
FastIR
È stato prodotto un sistema di montaggio per consentire il montaggio di due unità FastIR 500 di Ceramicx sopra e sotto il materiale. Un FastIR 500 è costituito da sette elementi riscaldanti montati in modo parallelo all'interno di una custodia 500 x 500 mm. La distanza tra questi tubi è 81mm. Sono stati utilizzati gli elementi "lunghi" (lunghezza totale: 1500mm) di 2000W e 473W che danno rispettivamente un output totale dalle due unità di 21 o 28kW. Le unità di riscaldamento erano montate in modo tale che la distanza tra la superficie dell'elemento e il campione fosse variata tra 55mm e 95mm.
Il protocollo sperimentale utilizzato era il seguente:
- I fan sono accesi
- Tre elementi riscaldanti centrali accesi, in alto e in basso
- All'esterno quattro resistenze accese, in alto e in basso
L'immagine di un campione tra le due unità FastIR è mostrata nella Figura 1. Nulla è stato usato per racchiudere lo spazio tra le due unità di riscaldamento
Elementi
Nell'unità FastIR possono essere montati due tipi di elementi; alogeno al quarzo e tungsteno al quarzo. Questi elementi emettono diverse lunghezze d'onda di picco a infrarossi; alogeno a circa 1.0 - 1.2μm e tungsteno tra 1.6 - 1.9μm. Ogni tubo ha un diametro di 10mm, una lunghezza totale di 473mm e una lunghezza riscaldata di 415mm.
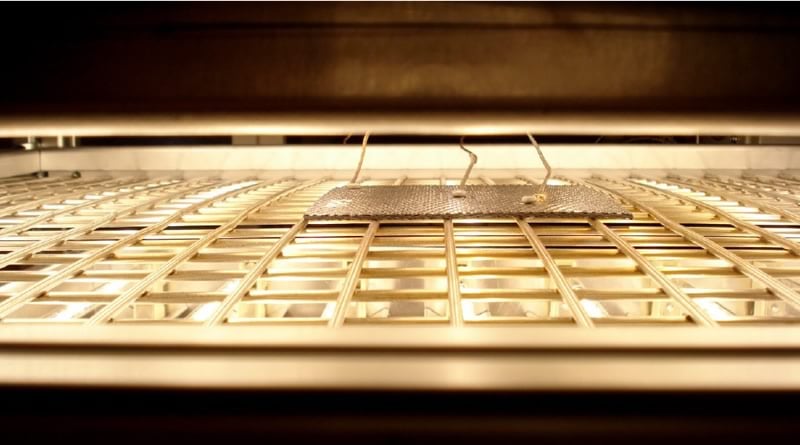
Cavità nera
Una piastra di riscaldamento personalizzata è stata progettata per incorporare una matrice 2 x 7 degli elementi FFEH 800W di Ceramicx, dando potenza a ciascuna piastra 11.2kW. Questa matrice è stata racchiusa in una custodia 510 x 510mm e montata nello stesso telaio del sistema FastIR descritto sopra. È stato utilizzato il protocollo sperimentale; tuttavia, i fan non erano impiegati in questi piani. La distanza tra questi elementi era 65mm.
Sono state utilizzate due diverse distanze campione-elemento, 50 e 100mm. Ancora una volta, lo spazio tra le due unità di riscaldamento è stato lasciato aperto
Elementi
Gli elementi cavi neri di Ceramicx emettono lunghezze d'onda di picco nel regime medio-lungo (2 - 10μm). Ogni elemento ha dimensioni di 245 x 60mm (lxw). Le lunghezze d'onda più lunghe associate agli elementi ceramici sono molto efficienti per riscaldare molti materiali polimerici.
Strumentazione
Le termocoppie di tipo K sono state fissate sulla superficie del campione usando viti M3. È stato testato il cemento ceramico, ma ciò non ha aderito alla superficie del materiale. Date le alte temperature richieste, nessun adesivo disponibile rimarrebbe stabile, quindi si è ritenuto necessario un fissaggio meccanico. Le termocoppie erano posizionate al centro di ciascun campione e anche 10mm (bordo) e 30mm (quarto) dal bordo, come mostrato nella Figura 2. Questo posizionava le termocoppie direttamente sopra gli elementi del tubo e al centro tra gli elementi in modo da registrare la massima differenza di temperatura. I dati di temperatura sono stati registrati a intervalli di un secondo.
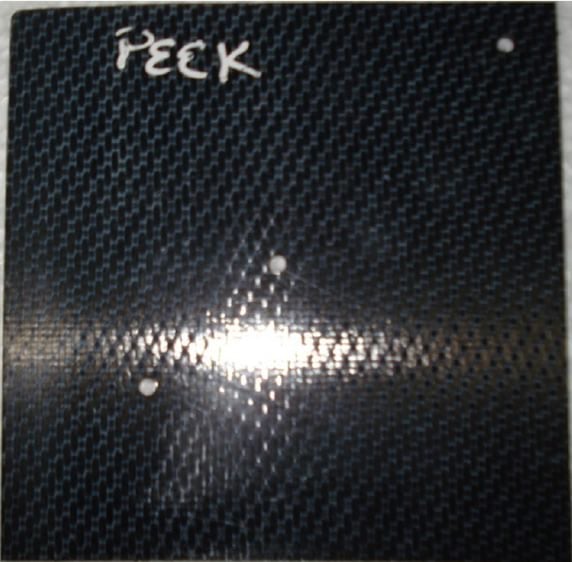
Test sandwich
Il tester sandwich è una macchina avanzata per il test della risposta termica del materiale, come mostrato nella Figura 2. Vari tipi di riscaldatori a infrarossi possono essere montati in due posizioni, rivolti verticalmente verso l'alto e verso il basso. Ciò garantisce che il materiale testato possa essere riscaldato dall'alto e / o dal basso. Vengono utilizzati quattro pirometri ottici senza contatto per determinare la temperatura della superficie superiore e inferiore del materiale testato. Gli emettitori possono riscaldarsi fino alla loro temperatura operativa e il materiale viene quindi portato sotto gli emettitori per un periodo predeterminato. Questo test è stato eseguito con 1kW tungsteno (QTM) e 800W elementi cavi neri (FFEH) montati 75mm sopra il campione per determinare quale riscaldatore ha fornito la migliore penetrazione attraverso il materiale.
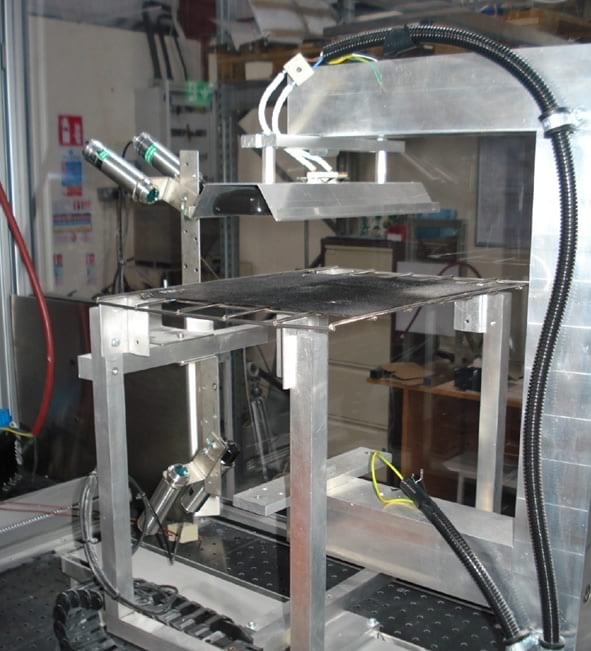
Risultati
FastIR
Questa sezione riporta i risultati trovati per i tubi al tungsteno e alogeni per i tre materiali in questione. I test sono stati effettuati con tre diverse altezze del riscaldatore (55 mm, 80 mm e 95 mm).
PEEK
Le prove iniziali sono state condotte con un campione PEEK e i due riscaldatori FastIR con tubi alogeni al quarzo 1500W separati da 110mm. I risultati di questo test, mostrati nella Figura 4, indicano che il campione non è riuscito a raggiungere la temperatura richiesta.
Gli elementi sono stati cambiati in tubi alogeni ad onde corte 2000W (QHL) che hanno mostrato che, alla stessa separazione, il campione ha raggiunto e superato la temperatura richiesta in una posizione. In questo caso, la temperatura massima registrata era 485 ° C, tuttavia, sono state rilevate anche differenze di temperatura significative (fino a 83 ° C). Il tempo necessario per raggiungere la temperatura target di 425 ° C era 99 secondi. Ciò è stato ottenuto solo in due posizioni
Anche i tubi al quarzo tungsteno (QTL) (2000W) sono stati esaminati ai tre livelli con temperatura massima che diminuiva all'aumentare della distanza del riscaldatore. A 55mm, è stata rilevata una temperatura massima e minima di 520 ° C. La temperatura target, attraverso il campione di materiale, è stata raggiunta in 206 secondi. Aumentando la distanza a 80mm, questi sono ridotti a 450 ° C e 415 ° C e a 95mm sopra il campione, le temperature massima e minima del campione erano 407 e 393 ° C.
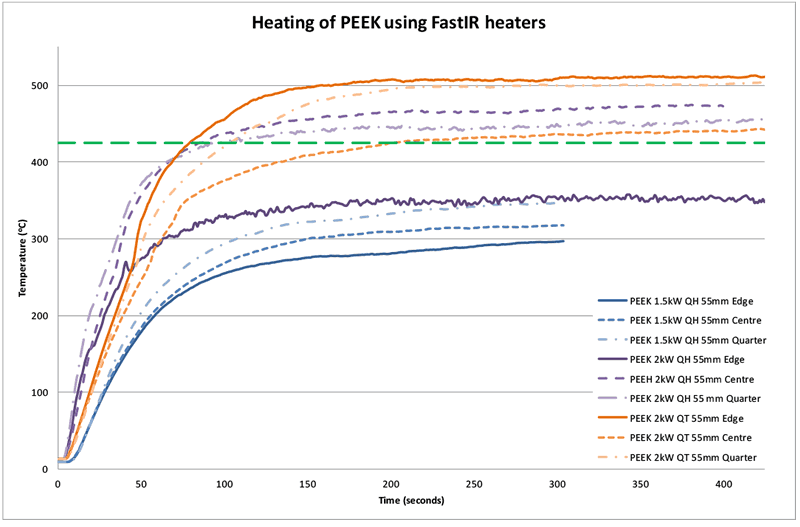
La Figura 4 mostra la varianza della temperatura che può verificarsi attraverso il campione a causa della stretta vicinanza dei riscaldatori al campione, nonché il tempo necessario per riscaldare il materiale a 425 ° C (secondi 206 per il riscaldatore QN 2kW).
I tubi in tungsteno 150 ° W non sono stati testati in quanto è stato ritenuto più operativamente importante aumentare la distanza del riscaldatore piuttosto che diminuire la potenza degli elementi utilizzati.
La Figura 5 mostra la differenza visiva nel campione prima e dopo il riscaldamento.
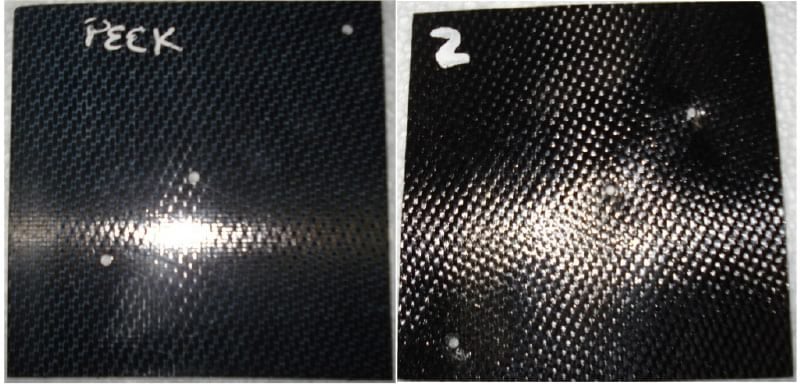
PEKK
PEKK è stato riscaldato con riscaldatori al tungsteno 2000W solo su 55mm. La risposta termica del materiale era eccellente con temperature superiori a 500 ° C in fase di registrazione. La temperatura minima stabilita è stata raggiunta in 102 secondi con la temperatura massima registrata superiore a 500 ° C.
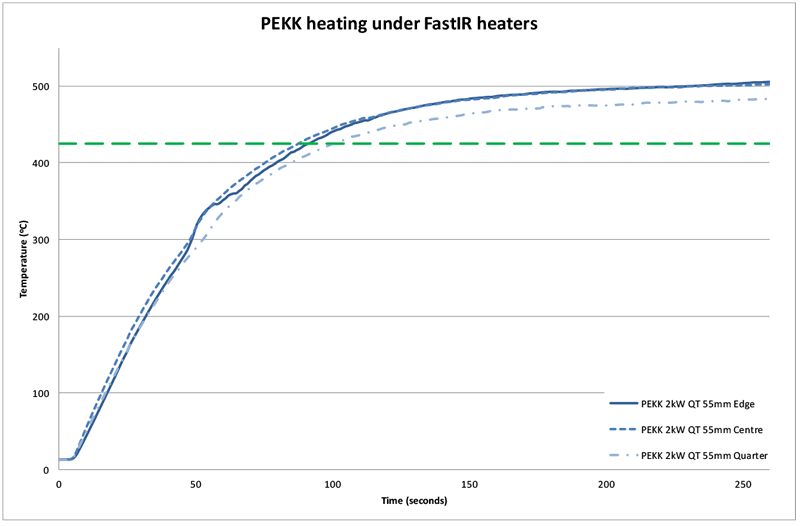
È stato evidente che questo campione sembrava mostrare alcune spaccature e delaminazioni ai bordi e anche alcune distorsioni della superficie a seguito del riscaldamento, come mostrato nella Figura 7, probabilmente dall'assorbimento di umidità durante lo stoccaggio e dal rapido riscaldamento che si è verificato.
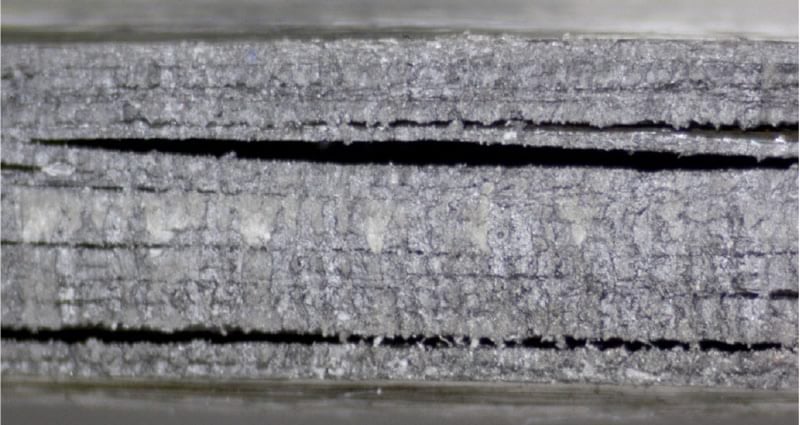
PPS
Il materiale PPS è stato testato con riscaldatori alogeni e tungsteno 2000W. Il test alogeno è stato condotto con una separazione di 55mm e i test al tungsteno su 55mm e 95mm.
I dati hanno nuovamente mostrato che il tubo di tungsteno era un riscaldatore migliore per questo materiale (rispetto al riscaldatore alogeno) con temperature più alte che venivano registrate alla separazione 55mm e anche una maggiore uniformità di temperatura attraverso il campione. Una variazione di 38 ° C è stata registrata per i riscaldatori alogeni e 30 ° C per i riscaldatori al tungsteno. Questa variazione registrata sarà fortemente influenzata dalla posizione della termocoppia rispetto ai tubi. Le posizioni identiche della termocoppia non sono garantite.
I test con PPS sono stati interrotti poco dopo che il materiale ha raggiunto la temperatura richiesta di 425 ° C in quanto si è verificato un rilascio di fumi odoranti di zolfo dai campioni.
A una distanza di 55mm, la temperatura target è stata registrata dopo 66 e 88 secondi rispettivamente per riscaldatori alogeni e tungsteno a 55mm. Quando i riscaldatori al tungsteno sono stati montati a 95mm dal campione, la temperatura target non è stata raggiunta.
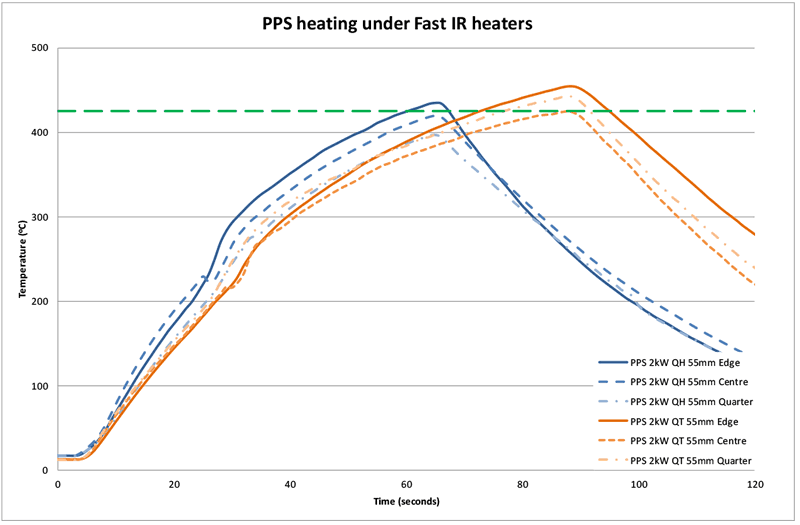
Cavità nera
I test iniziali sono stati condotti con una separazione elemento-materiale di 50mm. L'aumento della temperatura del materiale è stato molto rapido per tutti i materiali. Da un avvio a freddo, gli elementi cavi impiegano circa 10-12 minuti per riscaldarsi a livelli operativi costanti (temperatura superficiale di circa 700 ° C). L'aumento della temperatura del materiale era sostanzialmente simile alla curva di riscaldamento del riscaldatore, tuttavia, vi era un ritardo in questo.
PEEK
Un diagramma del tempo impiegato per riscaldare il campione di PEEK per raggiungere la temperatura di elaborazione richiesta è mostrato sotto nella Figura 9. Ciò mostra che il tempo di riscaldamento a 425 ° C è di circa 185 secondi dall'accensione dei riscaldatori a 50mm. Se la distanza viene aumentata a 100mm, il tempo viene aumentato a 230 secondi. Il campione è stato lasciato tra i due piani durante il riscaldamento e rimosso per il raffreddamento.
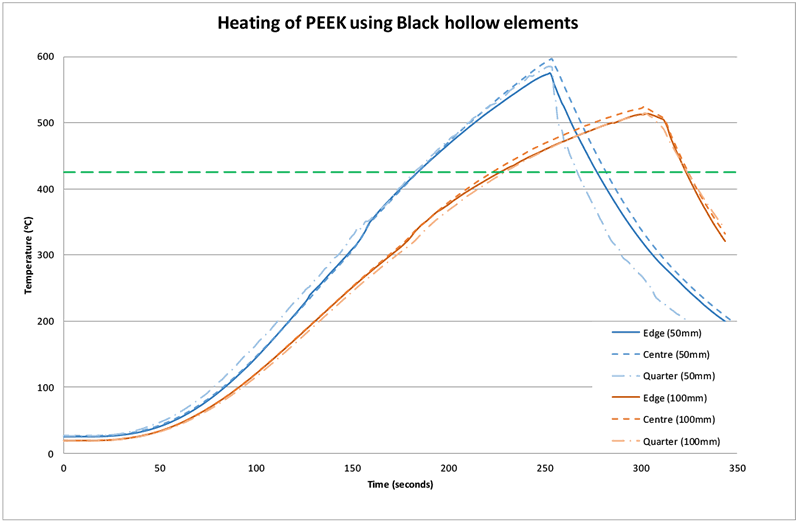
PEKK
Il tempo impiegato da PEKK per raggiungere la soglia minima è stato leggermente più lungo rispetto a PEKK. Esistono due possibili ragioni per questo: 1.) Il materiale non assorbe la radiazione infrarossa, così come PEEK e 2.) Lo spessore del materiale è due volte più grande (rispettivamente 1 e 2mm). Il tempo necessario per raggiungere 425 ° C a 50mm era 181 secondi e a 100mm questo è aumentato a 244 secondi
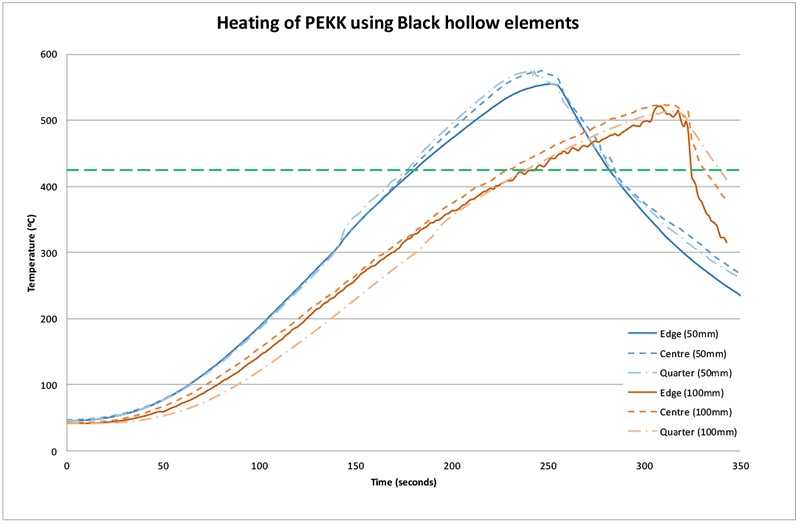
PPS
Il PPS si è riscaldato con successo con gli elementi cavi neri con 425 ° C registrati in 171 secondi e 219 secondi rispettivamente su 50 e 100mm. La curva di riscaldamento per questo materiale è mostrata nella Figura 11. Ancora una volta, si è verificato un rilascio di fumo profumato di zolfo, tuttavia la quantità di questo non era tanto quanto con i riscaldatori alogeni come descritto sopra. Ciò può essere parzialmente dovuto all'assenza di ventole sul retro della piastra di riscaldamento.
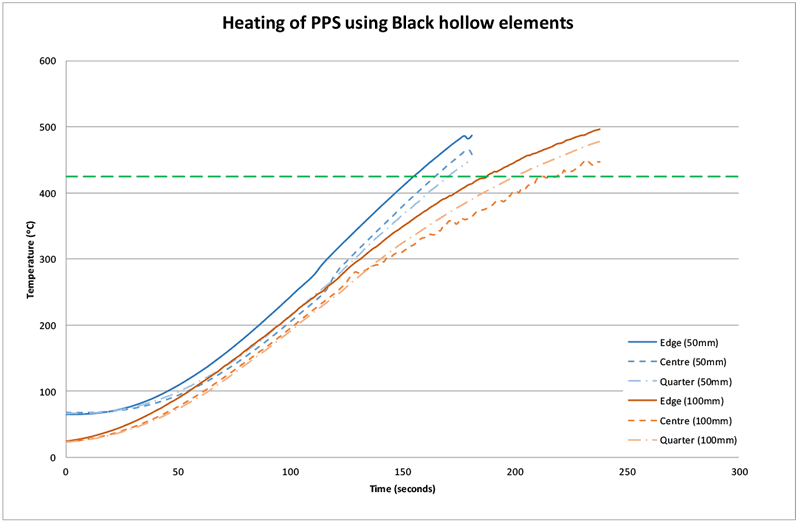
Nella tabella 1 è riportato di seguito un riepilogo dei tempi necessari per riscaldare i materiali, con alogeni, tungsteno e elementi in ceramica cava, alla temperatura target. Poiché il montaggio degli elementi alogeni a distanze maggiori di 55mm non ha avuto successo universale, questi risultati sono stati omessi dalla tabella.
Materiali |
Tipo di riscaldamento (potenza)
|
Distanza | Tempo per raggiungere 425 ° C |
---|---|---|---|
PEEK | QHL (2kW) | 55mm | 99 |
QTL (2kW) | 55mm | 206 | |
FFEH (800 W) | 50mm | 185 | |
FFEH (800 W) | 100mm | 230 | |
PEKK | QTL (2kW) | 55mm | 102 |
FFEH (800 W) | 50mm | 181 | |
FFEH (800 W) | 100mm | 244 | |
PPS | QHL (2kW) | 55mm | 66 |
QTL (2kW) | 55mm | 88 | |
FFEH (800 W) | 50mm | 171 | |
FFEH (800 W) | 100mm | 219 |
Test sandwich
Sono stati effettuati test sandwich per ottenere informazioni sul trasferimento di calore attraverso il materiale. Ciò è stato fatto riscaldando il campione da un solo lato, misurando la temperatura su entrambi i lati e confrontando i risultati. Sono stati esaminati solo i tubi di tungsteno e gli elementi cavi neri, in base ai risultati di FastIR, i tubi alogeni a onde corte non sono riscaldatori adatti per i materiali in questione.
I risultati per gli elementi QTM mostrano che non vi è alcuna differenza di temperatura significativa tra la superficie superiore e inferiore per i materiali PEEK e PPS, tuttavia PPS si riscalda più rapidamente e le curve per questo materiale sono praticamente indistinguibili. Va notato che questi due materiali sono molto sottili (≈ 1mm). Come previsto, la differenza di temperatura per PEKK era maggiore (75 ± 2oC) a causa del suo spessore (≈ 2mm). Questi risultati sono mostrati nella Figura 12 di seguito.
Per motivi operativi, il test termina quando i pirometri rilevano una temperatura di 300 ° C. Il picco visto nei primi 30 secondi del test è la riflettanza e non è una lettura della temperatura reale.
Questi risultati dimostrano che è possibile una buona penetrazione IR del materiale per PEEK e PPS utilizzando il riscaldatore di tipo tungsteno. Tuttavia, l'equalizzazione della temperatura per PEKK non è altrettanto buona, dimostrata dalla differenza di temperatura di quasi 75 ° C negli ultimi secondi 18 del test4.
Non è stato possibile avvicinare i campioni di materiale al riscaldatore per analizzare quale effetto avrebbe avuto in quanto l'angolo acuto richiesto al pirometro per vedere il materiale avrebbe distorto la lettura.
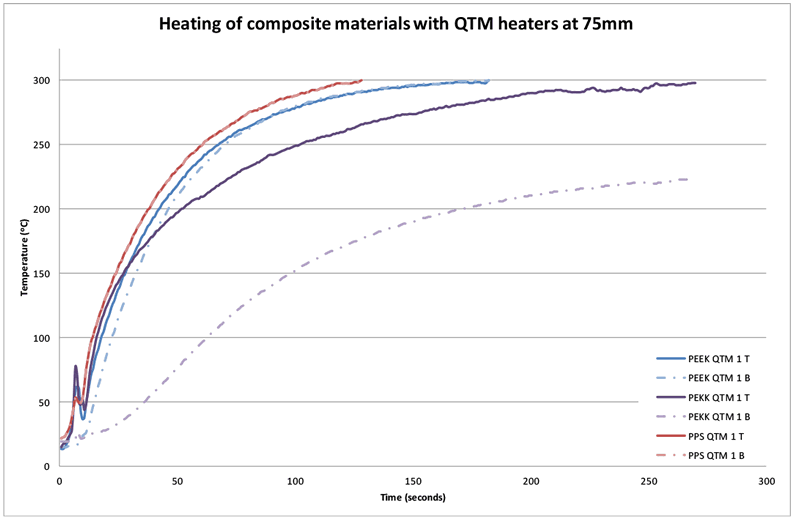
Il riscaldamento dei campioni con elementi cavi neri alla stessa distanza (75mm) mostra una tendenza simile con una differenza di temperatura maggiore (45 ± 2 ° C) osservata per il materiale PEKK più spesso (rispetto ai materiali più sottili). Le temperature delle superfici superiore e inferiore di PEEK sono praticamente indistinguibili; tuttavia c'è una differenza nella temperatura di PPS (25 ± 2 ° C). Questi dati sono mostrati nella Figura 13. Ciò indica che la penetrazione IR di PPS con radiazione a lunghezza d'onda più lunga non è buona come con IR a tungsteno più corto, tuttavia, l'equalizzazione della temperatura di PEKK è migliore (ma non ideale).
Alla separazione 75mm, le temperature e le velocità di riscaldamento più elevate sono ottenute utilizzando il riscaldatore al tungsteno che sembra contraddire i risultati della piastra precedente. Questo, tuttavia, non dovrebbe essere usato come guida in quanto è stato utilizzato un solo riscaldatore. Inoltre, queste caratteristiche saranno migliorate utilizzando una serie di riscaldatori anziché un singolo riscaldatore.
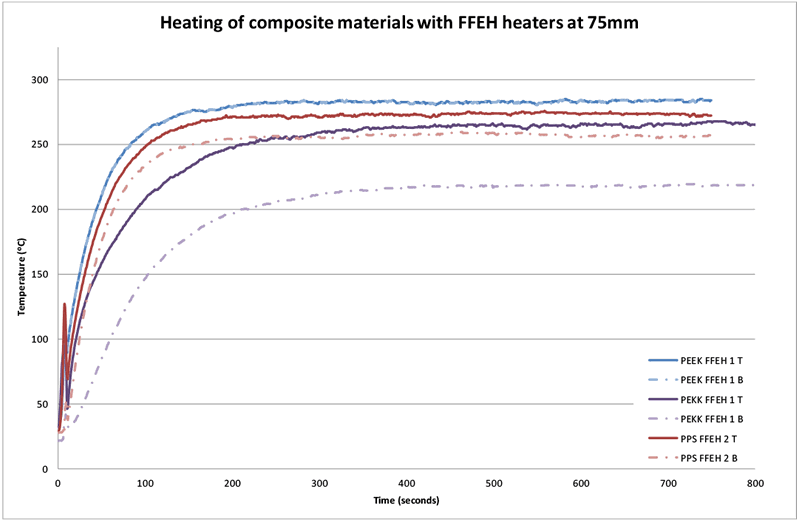
Conclusione
- I test effettuati e dettagliati sopra indicano che il riscaldamento dei tre materiali compositi di carbonio termoplastico a un minimo di 425 ° C è possibile sia con alogeni a onde medie che con elementi cavi neri.
- Temperature massime più elevate sono ottenibili utilizzando l'elemento cavo nero Ceramicx 800W (FFEH).
- Il tempo necessario per riscaldare PEEK a 425 ° C è stato di 206 secondi per i riscaldatori del tubo in tungsteno 2kW a 55mm e 230 secondi per gli elementi FFEH a 100mm
- Il tempo necessario per riscaldare PEKK a 425 ° C è stato di 102 secondi per i riscaldatori del tubo in tungsteno 2kW a 55mm e 244 secondi per gli elementi FFEH a 100mm
- Il tempo necessario per riscaldare PPS a 425 ° C è stato di 88 secondi per i riscaldatori di tubi in tungsteno 2kW su 55mm e 219 secondi per gli elementi FFEH su 100mm
- Le temperature massime, le velocità di riscaldamento del materiale ottenibili e l'uniformità della temperatura superficiale sono una forte funzione della distanza alla quale i riscaldatori sono montati dal materiale.
- L'eccellente penetrazione IR e quindi l'equalizzazione della temperatura, attraverso lo spessore del materiale, di PPS e PEEK sono state ottenute con alogeno a onde medie (tungsteno). L'equalizzazione della temperatura raggiunta con PEKK non era buona come con gli altri materiali.
- Eccellente penetrazione IR ed equalizzazione della temperatura sono state osservate con PEEK usando elementi cavi neri. Questa proprietà non era buona come per PEKK e PPS.
Sulla base dei dati di test sopra riportati e delle strette separazioni elemento-materiale necessarie per raggiungere le temperature richieste per formare i materiali in questione, sembra che il miglior emettitore a infrarossi sia l'elemento cavo completamente piatto nero Ceramicx 800W. Mentre i tempi per raggiungere le temperature richieste sono leggermente più lunghi rispetto ai riscaldatori al tungsteno, la maggiore vicinanza degli elementi utilizzati porterà a una migliore uniformità della temperatura superficiale. Inoltre, gli elementi ceramici sono stati avviati dalla temperatura ambiente e per raggiungere i livelli operativi sono stati necessari circa 12 minuti. Pertanto, questa volta potrebbe essere notevolmente ridotta preriscaldando gli elementi.
Va anche notato che questi risultati si basano sui campioni che sono stati resi disponibili per i test (ad es. 1mm e 2mm di spessore). Il riscaldamento di parti più spesse può richiedere importanti cambiamenti nella tecnologia di riscaldamento da esaminare per garantire che il profilo di temperatura, attraverso lo spessore del materiale, sia uniforme e adatto alle successive operazioni di formatura.
1 Chetone di etere polietere
2 Solfuro di polifenilene
3 Polieterchetonechetone
4 Differenza media tra le superfici superiore e inferiore rilevata negli ultimi 18 secondi del test.
Negazione di responsabilità
Questi risultati dei test devono essere attentamente considerati prima che un determinato tipo di emettitore a infrarossi sia determinato a impiegare.
Ripetere i test condotti da altre società potrebbe non ottenere gli stessi risultati. Le differenze nelle condizioni sperimentali possono alterare i risultati. Altre fonti di errore includono: la marca dell'emettitore impiegato, l'efficienza dell'emettitore, la potenza fornita, la distanza dal materiale testato all'emettitore utilizzato e l'ambiente. Le posizioni in cui viene misurata la temperatura possono anche causare variazioni nei risultati.