AUTOR | DATA CRIADA | VERSÃO | NÚMERO DO DOCUMENTO |
---|---|---|---|
Dr. Peter Marshall | 1 de Dezembro de 2017 | V1.1 | CC11 - 00120 |
Introdução
Este artigo estuda a influência da exposição dos refletores infravermelhos de aço aluminizado Ceramicx e aço inoxidável a altas temperaturas na refletividade do material. Uma comparação é feita entre refletores novos e oxidados para avaliar a influência disso no fluxo de calor radiativo percentual.
Materiais
Dois refletores de formato padrão (RAS 1) para elementos cerâmicos foram utilizados neste estudo. Uma vez foi o aço aluminizado padrão da Ceramicx, enquanto o outro era aço inoxidável. O mesmo 1000W FTE com vidro preto foi usado em todos os testes.
Forma
Os refletores foram colocados no forno a 600 ° C por 8 horas sob condições atmosféricas padrão. Após o aquecimento, eles foram deixados esfriar dentro do forno até esfriar. Depois que esse processo foi concluído, um FTE com vidro preto 1000W foi instalado no refletor e o fluxo de calor registrado usando o procedimento padrão.
O robô de fluxo de calor Ceramicx Herschel examina o fluxo de calor total (W.cm-2) que ocorre no sensor. Os aquecedores podem ser montados no Herschel e analisados usando a rotina de mapeamento de fluxo de calor por infravermelho 3D. Esse sistema automatizado usa um sensor infravermelho que é guiado por robô em torno de um sistema de grade de coordenadas pré-determinado na frente do emissor do aquecedor em teste. O sensor possui um nível máximo de fluxo de calor de 2.3 W.cm-2 e mede o IR nos micrômetros da banda 0.4-10. O sistema de coordenadas é uma grade cúbica 500mm na frente do emissor de aquecimento, veja a Figura 1. O robô move o sensor em incrementos de 25mm ao longo de um caminho serpentino nas direções X e Z-, enquanto o emissor de aquecimento é montado em um carro deslizante que aumenta em passos 50mm ao longo da direção Y.
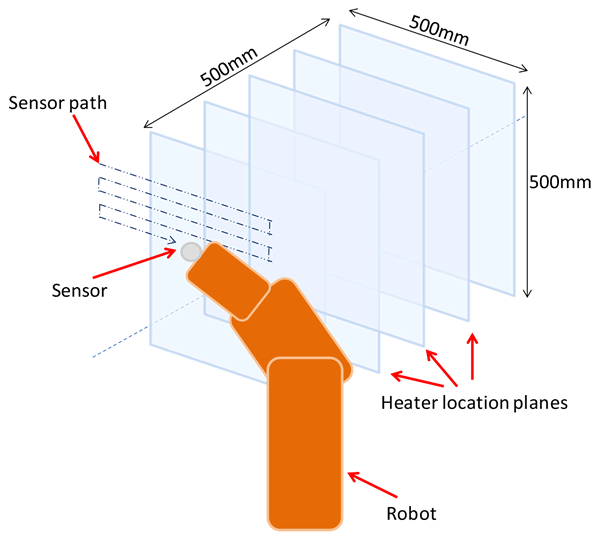
Os resultados da máquina podem ser correlacionados com uma porcentagem da energia total consumida retornada como fluxo de calor radiante do aquecedor. Isso diminui com a distância do aquecedor à medida que o fluxo de calor radiante diverge do aquecedor.
Resultados
Tratamento térmico
Após o tratamento térmico, o refletor de aço aluminizado mostrou uma área cinza-fosca na porção central do refletor, enquanto o refletor de aço inoxidável mostrou a cor azul / púrpura profunda, conforme mostrado na Figura 1, abaixo.
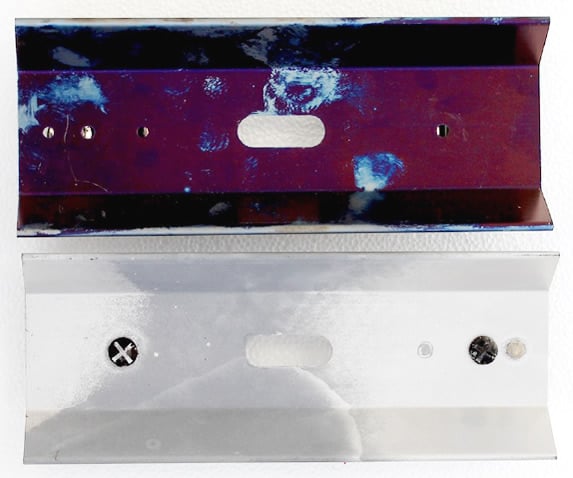
Medição de fluxo de calor
Os refletores aluminizados e de aço inoxidável não utilizados mostram que a porcentagem máxima de fluxo de calor é registrada em 100mm a partir do elemento, como é mostrado na Figura 3 abaixo. Os resultados do fluxo de calor mostram que o percentual de fluxo de calor registrado é maior para o refletor de aço aluminizado do que para o refletor de aço inoxidável, consistente com muita literatura publicada até hoje pela Ceramicx e outros.
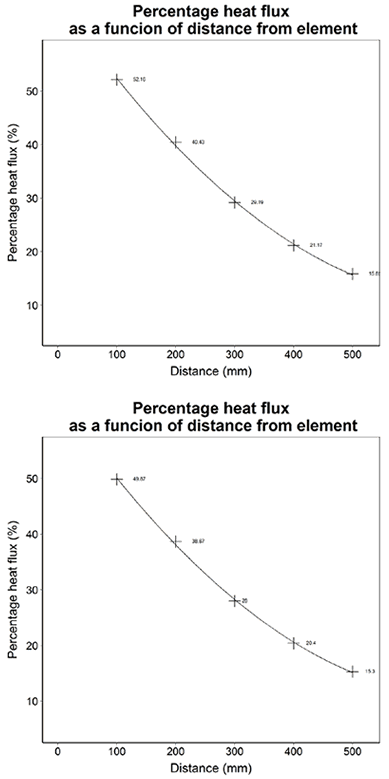
A exposição prolongada a altas temperaturas causa oxidação e, portanto, a eficiência do refletor diminui. Para aço aluminizado, a camada de óxido visível causa uma diminuição de% de 18.6, conforme mostrado na Figura 4, abaixo. Para aço inoxidável, essa redução é 2%, o que está dentro dos limites do erro experimental.
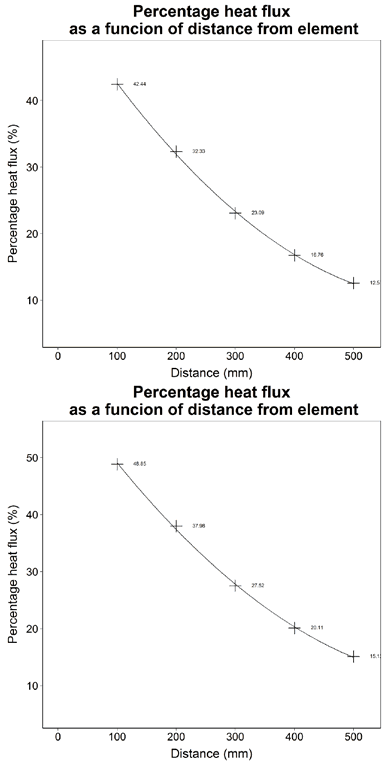
O pico de fluxo de calor para aço aluminizado não tratado foi maior que para aço inoxidável. Isso era esperado, dado que as propriedades refletivas do aço aluminizado são melhores que o aço inoxidável. Após o tratamento térmico, a Tabela 1 mostra que o pico de fluxo de calor do aço aluminizado caiu drasticamente à medida que a camada de óxido no material absorve a radiação infravermelha. Por outro lado, a mudança de cor do refletor de aço inoxidável, em linha com a medição percentual do fluxo de calor, mostrou apenas uma pequena diminuição.
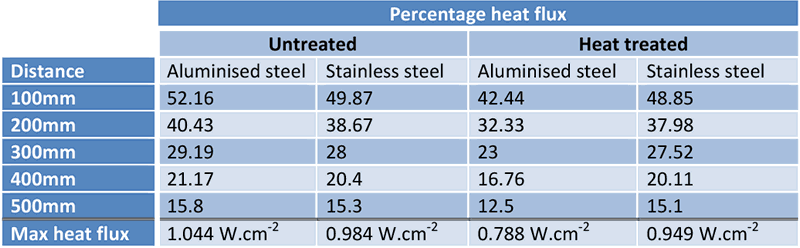
Nenhuma mudança distinta foi observada no padrão de emissão do elemento. Além disso, a mudança no fluxo de calor, em função da distância, foi a esperada.
Conclusão
Como mostrado anteriormente pela Ceramicx, o uso de um refletor de aço aluminizado polido aumenta a porcentagem de fluxo de calor radiativo emitido em direção ao alvo de aquecimento em comparação com o aço inoxidável. Para aplicações em temperaturas mais baixas, onde é improvável a oxidação do alumínio, o aço aluminizado é um material com melhor desempenho. Para aplicações em temperaturas mais altas, nas quais é provável que ocorra a oxidação do alumínio, o aço inoxidável é uma escolha melhor, pois leva a uma proporção maior de energia radiativa direcionada ao material alvo.
Aviso Legal
Esses resultados do teste devem ser cuidadosamente considerados antes da determinação do tipo de emissor infravermelho a ser usado em um processo. Testes repetidos realizados por outras empresas podem não alcançar os mesmos resultados. Existe a possibilidade de erro no alcance das condições de configuração e variáveis que podem alterar os resultados incluem a marca do emissor empregado, a eficiência do emissor, a potência fornecida, a distância do material testado ao emissor utilizado e o ambiente . Os locais em que as temperaturas são medidas também podem diferir e, portanto, afetar os resultados.