AUTOR | DATA CRIADA | VERSÃO | NÚMERO DO DOCUMENTO |
---|---|---|---|
Dr. Peter Marshall | 8 de Abril de 2016 | V1.1 | CC11 - 00101 |
Introdução
A CCP Gransden abordou a Ceramicx para construir um forno infravermelho para aquecer materiais pré-impregnados de fibra de carbono termoplástica para suas operações de conformação. Este trabalho de teste foi realizado como parte das funções definidas na proposta de venda (CSP 000 008). A fase um envolve a avaliação e seleção do aquecedor infravermelho para este projeto, com a temperatura mínima estipulada do material sendo 425 ° C.
Descrição do material
Três amostras de dois materiais foram recebidas em peças 230 x 230 x 1mm. Nesses casos, a matriz era PEEK1 e PPS2. Uma amostra menor de PEKK3 com dimensões de 200 x 150 x 2mm também foi recebido. O material era rígido, liso com um acabamento preto brilhante. Um pequeno padrão foi visível na superfície das amostras de PEEK e PPS.
As amostras de PEEK e PPS foram cortadas em pedaços de 115 x 115 mm. O material PEKK foi cortado em pedaços 100 x 75mm.
Forma
Duas famílias distintas de aquecedores foram avaliadas; halogênio (QH e QT) e cerâmica oca preta (FFEH). Em cada caso, as placas foram montadas acima e abaixo da amostra de material com altura ajustável.
FastIR
Um sistema de montagem foi fabricado para permitir que duas unidades FastIR 500 da Ceramicx sejam montadas acima e abaixo do material. Um FastIR 500 consiste em sete elementos de aquecimento montados de maneira paralela dentro de um gabinete de 500 x 500 mm. O espaçamento entre esses tubos é 81mm. Foram utilizados os elementos 1500W e 2000W 'long' (comprimento total: 473mm), fornecendo uma saída total das duas unidades de 21 ou 28kW, respectivamente. As unidades de aquecimento foram montadas de modo que a distância entre a superfície do elemento e a amostra variasse entre 55mm e 95mm.
O protocolo experimental utilizado foi o seguinte:
- Ventiladores ligados
- Três elementos de aquecimento centrais ligados, superior e inferior
- Fora de quatro elementos de aquecimento ligados, superior e inferior
Uma imagem de uma amostra entre as duas unidades FastIR é mostrada na Figura 1. Nada foi usado para delimitar o espaço entre as duas unidades de aquecimento
elementos
Dois tipos de elemento podem ser montados na unidade FastIR; halogênio de quartzo e tungstênio de quartzo. Esses elementos emitem diferentes comprimentos de onda de infravermelho de pico; halogênio a aproximadamente 1.0 - 1.2μm e tungstênio entre 1.6 - 1.9μm. Cada tubo tem um diâmetro de 10mm, um comprimento total de 473mm e um comprimento aquecido de 415mm.
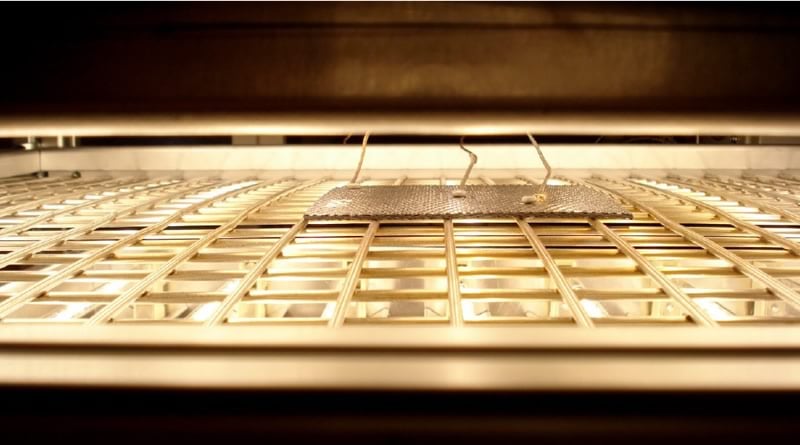
Oco preto
Uma placa de aquecimento personalizada foi projetada para incorporar uma matriz 2 x 7 dos elementos 800W FFEH da Ceramicx, fornecendo energia a cada placa 11.2kW. Essa matriz foi encerrada em um gabinete 510 x 510mm e montada no mesmo quadro que o sistema FastIR detalhado acima. O protocolo experimental foi utilizado; no entanto, os ventiladores não eram empregados nesses pratos. A distância entre esses elementos era 65mm.
Foram utilizadas duas distâncias elemento-amostra diferentes, 50 e 100mm. Mais uma vez, a lacuna entre as duas unidades de aquecimento foi deixada em aberto
elementos
Os elementos ocos pretos Ceramicx emitem comprimentos de onda de pico no regime médio a longo (2 - 10μm). Cada elemento possui dimensões de 245 x 60mm (lxw). Os comprimentos de onda mais longos associados aos elementos cerâmicos são muito eficientes para aquecer muitos materiais poliméricos.
Instrumentação
Os termopares tipo K foram afixados na superfície da amostra usando parafusos M3. O cimento cerâmico foi testado, no entanto, este não aderiu à superfície do material. Dadas as altas temperaturas exigidas, nenhum adesivo disponível permaneceria estável, portanto a fixação mecânica foi considerada necessária. Os termopares estavam localizados no centro de cada amostra e também 10mm (borda) e 30mm (quarto) da borda, como mostra a Figura 2. Isso localizou os termopares diretamente sobre os elementos do tubo e no centro entre os elementos, para que a diferença máxima de temperatura fosse registrada. Os dados de temperatura foram registrados em intervalos de um segundo.
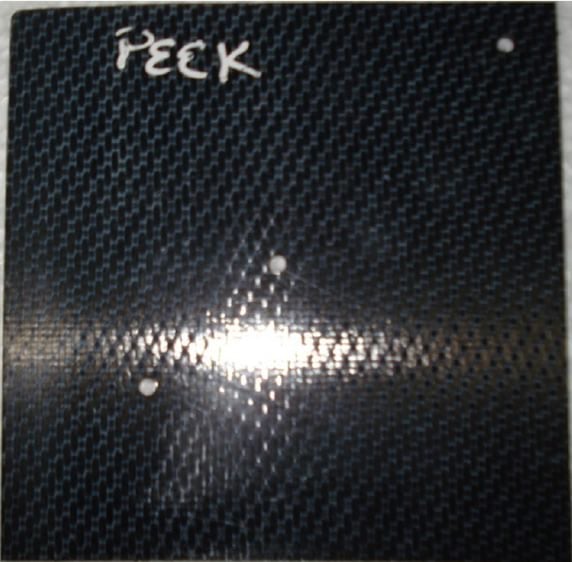
Teste de sanduíche
O testador sanduíche é uma máquina avançada de teste de resposta térmica de material, como mostra a Figura 2. Vários tipos de aquecedores infravermelhos podem ser montados em duas posições, voltados verticalmente para cima e para baixo. Isso garante que o material testado possa ser aquecido por cima e / ou por baixo. Quatro pirômetros ópticos sem contato são usados para determinar a temperatura da superfície superior e inferior do material testado. Os emissores podem aquecer até a temperatura operacional e o material é levado ao (s) emissor (s) por um período predeterminado. Esse teste foi realizado com os elementos ocos pretos 1kW (QTM) e 800W ocos pretos (FFEH) montados 75mm acima da amostra para determinar qual aquecedor proporcionou a melhor penetração no material.
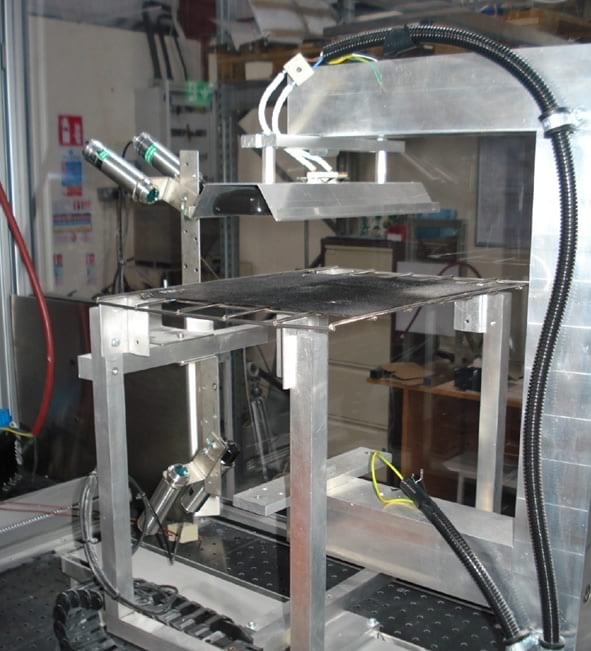
Resultados
FastIR
Esta seção relata os resultados encontrados para tubos de tungstênio e halogênio para os três materiais em questão. Os testes foram realizados com três alturas de aquecimento diferentes (55 mm, 80 mm e 95 mm).
PEEK
Os ensaios iniciais foram conduzidos com uma amostra de PEEK e os dois aquecedores FastIR com tubos de halogênio de quartzo 1500W separados por 110mm. Os resultados deste teste, mostrados na Figura 4, indicam que a amostra falhou em atingir a temperatura necessária.
Os elementos foram alterados para tubos 2000W halogênio de ondas curtas (QHL), que mostraram que, na mesma separação, a amostra atingiu e excedeu a temperatura necessária em um local. Nesse caso, a temperatura máxima registrada foi 485 ° C, no entanto, diferenças significativas de temperatura (até 83 ° C) também foram detectadas. O tempo necessário para atingir a temperatura alvo de 425 ° C foi 99 segundos. Isso foi alcançado apenas em dois locais
Os tubos de quartzo tungstênio (QTL) (2000W) também foram examinados nos três níveis, com a temperatura máxima caindo à medida que a distância do aquecedor aumentava. Em 55mm, foi detectada uma temperatura máxima e mínima de 520 ° C. A temperatura alvo, através da amostra de material, foi alcançada em segundos 206. Aumentando a distância para 80mm, estes foram reduzidos para 450 ° C e 415 ° C e a 95mm acima da amostra, as temperaturas máxima e mínima da amostra foram 407 e 393 ° C.
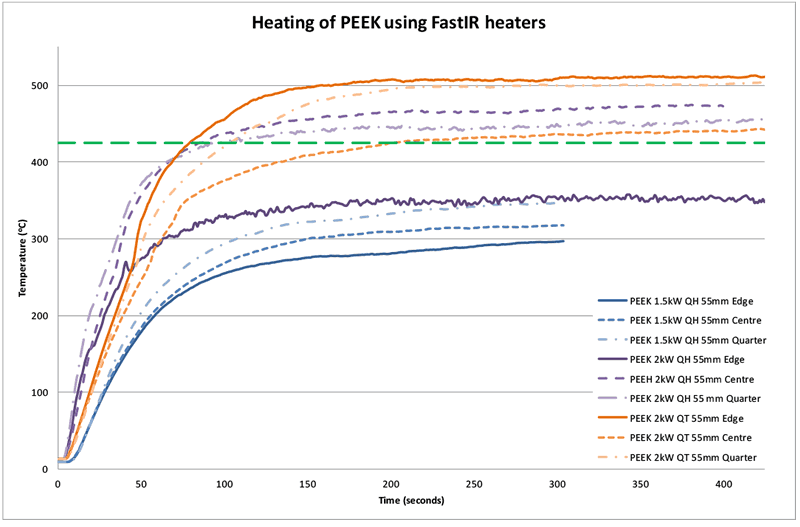
A Figura 4 mostra a variação de temperatura que pode ocorrer na amostra devido à proximidade dos aquecedores à amostra, bem como o tempo necessário para aquecer o material até 425 ° C (206 segundos para o aquecedor 2kW QT).
Os tubos de tungstênio 150 ° W não foram testados, pois foi considerado operacionalmente mais importante aumentar a distância do aquecedor do que diminuir a potência dos elementos utilizados.
A figura 5 mostra a diferença visual na amostra antes e após o aquecimento.
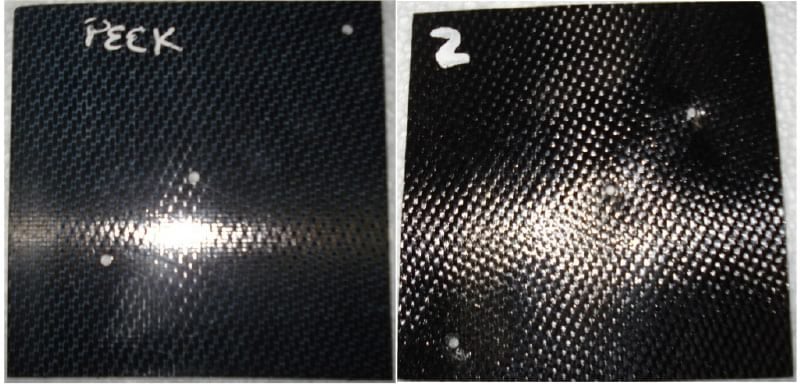
PEKK
O PEKK foi aquecido com aquecedores de tungstênio 2000W apenas no 55mm. A resposta térmica do material foi excelente, com temperaturas acima de 500 ° C sendo registradas. A temperatura mínima estipulada foi alcançada em segundos do 102, com a temperatura máxima registrada excedendo o 500 ° C.
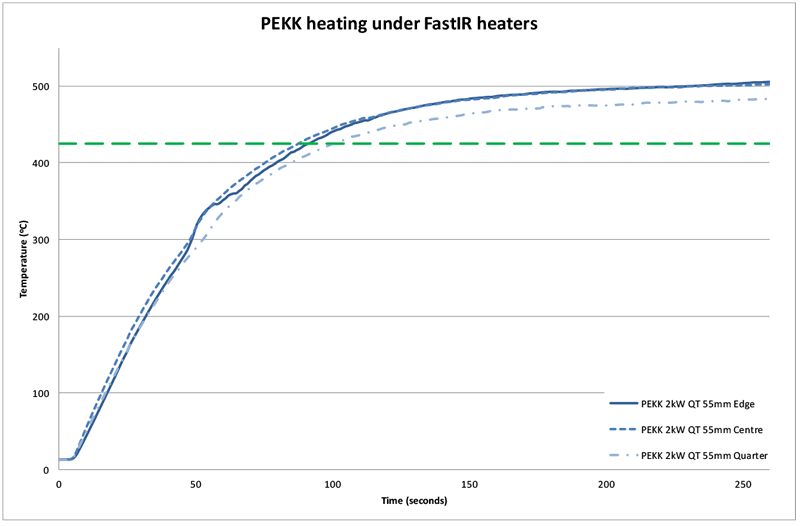
Foi notado que esta amostra parecia mostrar alguma divisão e delaminação nas bordas e também algumas distorções da superfície após o aquecimento, como mostrado na Figura 7, possivelmente devido à absorção de umidade durante o armazenamento e ao rápido aquecimento que ocorreu.
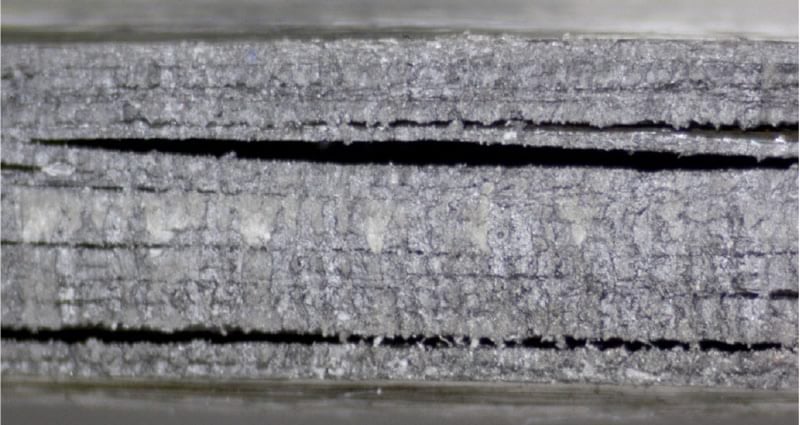
PPS
O material PPS foi testado com aquecedores de halogênio e tungstênio 2000W. O teste de halogênio foi realizado com uma separação de 55mm e os testes de tungstênio em 55mm e 95mm.
Os dados novamente mostraram que o tubo de tungstênio era um aquecedor melhor para este material (do que o aquecedor de halogênio), com temperaturas mais altas sendo registradas na separação 55mm e também maior uniformidade de temperatura na amostra. Uma variação de 38 ° C foi registrada para os aquecedores de halogênio e 30 ° C para aquecedores de tungstênio. Essa variação registrada será altamente influenciada pela localização do termopar em relação aos tubos. Locais idênticos de termopares não são garantidos.
Os testes com PPS foram finalizados logo após o material atingir a temperatura requerida de 425 ° C, pois houve uma liberação de fumos com cheiro de enxofre das amostras.
A uma distância de 55mm, a temperatura alvo foi registrada após segundos de 66 e 88 para aquecedores de halogênio e tungstênio em 55mm, respectivamente. Quando os aquecedores de tungstênio foram montados a 95mm a partir da amostra, a temperatura alvo não foi atingida.
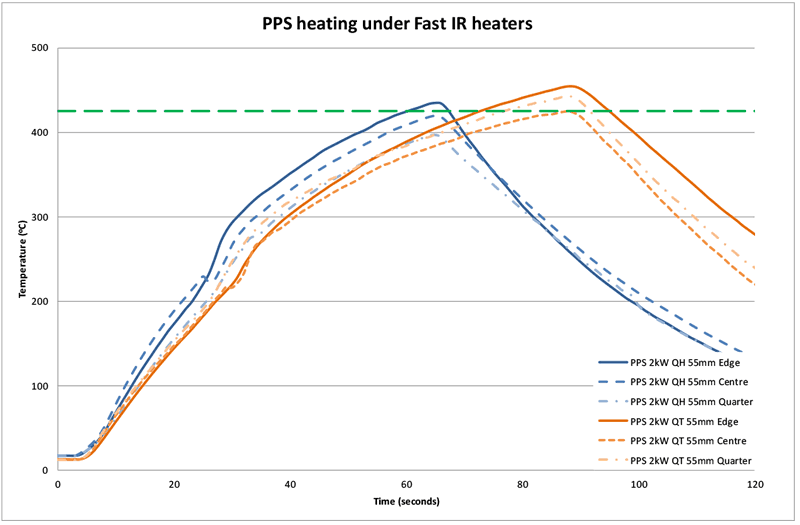
Oco preto
Os testes iniciais foram conduzidos com uma separação elemento-material de 50mm. O aumento da temperatura do material foi muito rápido para todos os materiais. De partida a frio, os elementos ocos levam aproximadamente 10-12 minutos para aquecer a níveis operacionais estáveis (temperatura da superfície de aprox. 700 ° C). O aumento da temperatura do material foi amplamente semelhante à curva de aquecimento do aquecedor; no entanto, houve um atraso de tempo nisso.
PEEK
Um gráfico do tempo necessário para aquecer a amostra de PEEK para atingir a temperatura de processamento necessária é mostrado abaixo na Figura 9. Isso mostra que o tempo de aquecimento até 425 ° C é de aproximadamente 185 segundos a partir de quando os aquecedores são ligados a 50mm. Se a distância for aumentada para 100mm, o tempo será aumentado para 230 segundos. A amostra foi deixada entre as duas placas durante o aquecimento e removida para resfriamento.
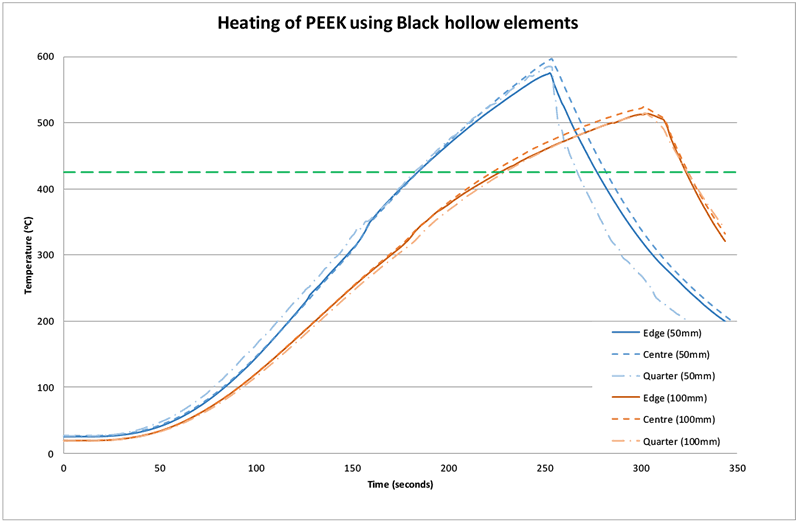
PEKK
O tempo necessário para o PEKK atingir o limite mínimo foi um pouco maior que o do PEEK. Existem duas razões possíveis para isso: 1.) O material não absorve a radiação infravermelha, bem como PEEK e 2.) A espessura do material é duas vezes maior (1 e 2mm, respectivamente). O tempo necessário para atingir o 425 ° C em 50mm foi 181 segundos e, em 100mm, aumentou para 244 segundos
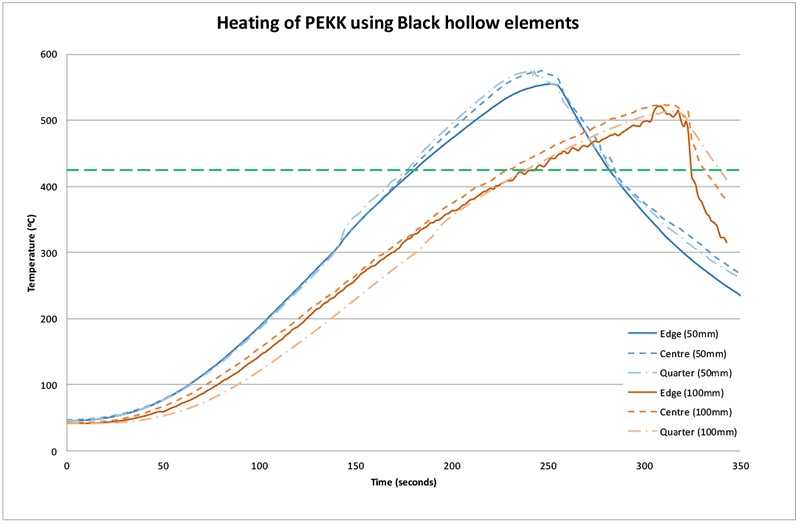
PPS
O PPS foi aquecido com muito sucesso, com os elementos ocos pretos com o 425 ° C sendo gravado em segundos 171 e em segundos 219 em 50 e 100mm, respectivamente. A curva de aquecimento para este material é mostrada na Figura 11. Novamente, ocorreu uma liberação de fumaça com cheiro de enxofre; no entanto, a quantidade disso não foi tanto quanto nos aquecedores de halogênio, conforme detalhado acima. Isso pode ser parcialmente devido à ausência de ventiladores na parte traseira da placa de aquecimento.
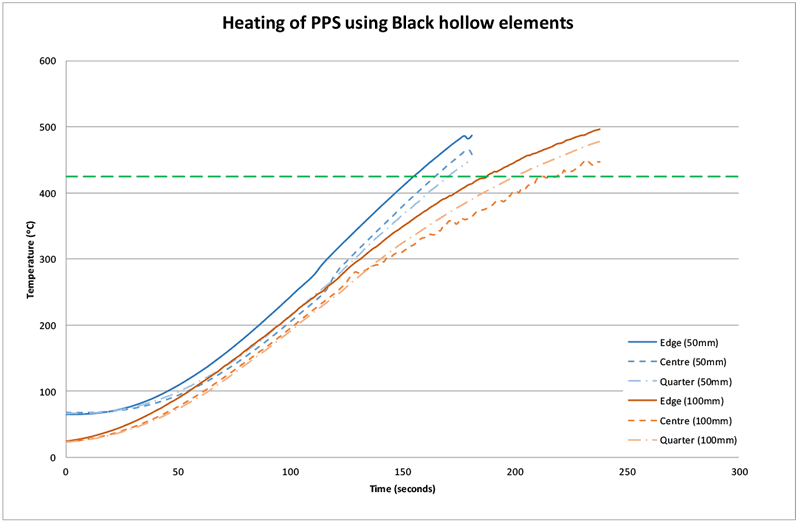
Um resumo dos tempos necessários para aquecer os materiais, com elementos cerâmicos de halogênio, tungstênio e ocos, até a temperatura alvo é mostrado abaixo na Tabela 1. Como a montagem dos elementos halógenos a distâncias maiores do que o 55mm não teve sucesso universal, esses resultados foram omitidos da tabela.
Material |
Tipo de aquecedor (potência)
|
Distância | Hora de atingir 425 ° C |
---|---|---|---|
PEEK | QHL (2kW) | 55mm | 99 |
QTL (2kW) | 55mm | 206 | |
FFEH (800W) | 50mm | 185 | |
FFEH (800W) | 100mm | 230 | |
PEKK | QTL (2kW) | 55mm | 102 |
FFEH (800W) | 50mm | 181 | |
FFEH (800W) | 100mm | 244 | |
PPS | QHL (2kW) | 55mm | 66 |
QTL (2kW) | 55mm | 88 | |
FFEH (800W) | 50mm | 171 | |
FFEH (800W) | 100mm | 219 |
Teste de sanduíche
Testes em sanduíche foram realizados para obter informações sobre a transferência de calor através do material. Isso foi feito aquecendo a amostra de um único lado, medindo a temperatura dos dois lados e comparando os resultados. Tubos de tungstênio e elementos ocos pretos foram examinados apenas, pois com base nos resultados do FastIR, os tubos de halogênio de ondas curtas não são aquecedores adequados para os materiais em questão.
Os resultados para os elementos QTM mostram que não há diferença significativa de temperatura entre a superfície superior e inferior dos materiais PEEK e PPS; no entanto, o PPS aquece mais rapidamente e as curvas para esse material são praticamente indistinguíveis. Note-se que esses dois materiais são muito finos (≈ 1mm). Como esperado, a diferença de temperatura para PEKK foi maior (75 ± 2oC) devido à sua espessura (≈ 2mm). Esses resultados são mostrados na Figura 12 abaixo.
Por razões operacionais, o teste termina quando uma temperatura de 300 ° C é detectada pelos pirômetros. O pico observado nos primeiros segundos do 30 do teste é refletância e não é uma leitura verdadeira da temperatura.
Esses resultados demonstram que é possível uma boa penetração de IR do material para PEEK e PPS usando o aquecedor do tipo tungstênio. No entanto, a equalização de temperatura para PEKK não é tão boa, demonstrada pela diferença de temperatura quase 75 ° C nos últimos segundos de 18 do teste4.
Não foi possível mover as amostras de material para mais perto do aquecedor para analisar qual efeito isso teria como o ângulo agudo necessário para o pirômetro ver o material distorceria a leitura.
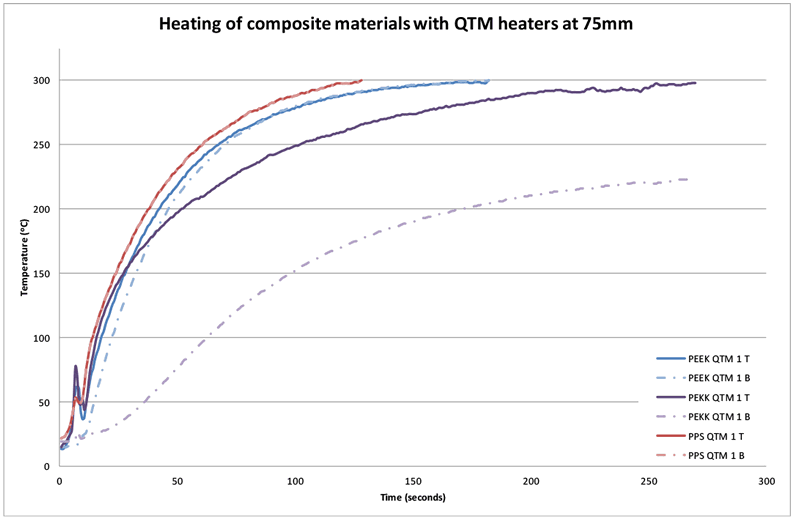
O aquecimento das amostras com elementos ocos pretos na mesma distância (75mm) mostra uma tendência semelhante, com uma diferença de temperatura maior (45 ± 2 ° C) sendo observada para o material PEKK mais espesso (comparado com os materiais mais finos). As temperaturas das superfícies superior e inferior do PEEK são praticamente indistinguíveis; no entanto, há uma diferença na temperatura do PPS (25 ± 2 ° C). Esses dados são mostrados na Figura 13. Isso indica que a penetração no IR do PPS com radiação de comprimento de onda maior não é tão boa quanto no IR com tungstênio mais curto; no entanto, a equalização de temperatura do PEKK é melhor (mas não ideal).
Na separação 75mm, as temperaturas e taxas de aquecimento mais altas são obtidas com o aquecedor de tungstênio, que parece contradizer os resultados anteriores da placa. No entanto, isso não deve ser usado como guia, pois apenas um aquecedor foi usado. Além disso, essas características serão aprimoradas usando uma matriz de aquecedores, em oposição a um único aquecedor.
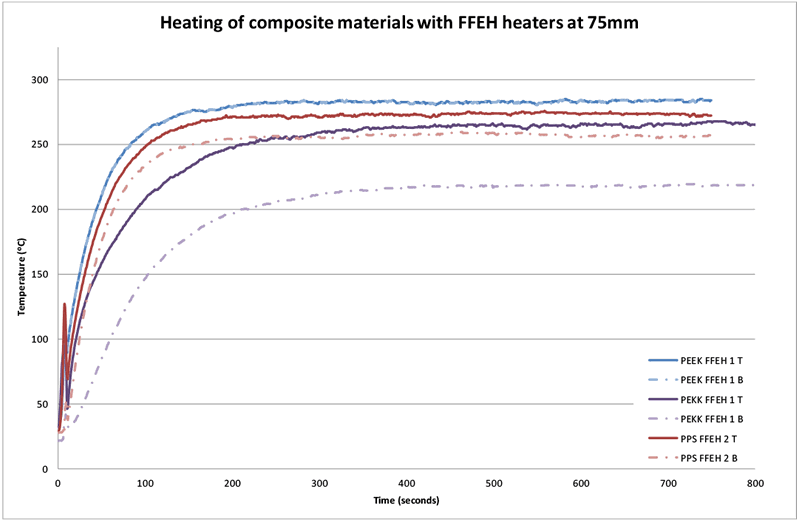
Conclusão
- Os testes realizados e detalhados acima indicam que o aquecimento dos três materiais compósitos de carbono termoplástico a um mínimo de 425 ° C é possível com halogênio de onda média e elementos ocos pretos.
- É possível obter temperaturas máximas mais altas usando o elemento oco preto (FFEH) da Ceramicx 800W.
- O tempo necessário para aquecer PEEK a 425 ° C foi 206 segundos para aquecedores de tubo de tungstênio 2kW a 55mm e 230 segundos para elementos FFEH em 100mm
- O tempo necessário para aquecer PEKK a 425 ° C foi 102 segundos para aquecedores de tubo de tungstênio 2kW a 55mm e 244 segundos para elementos FFEH em 100mm
- O tempo necessário para aquecer o PPS a 425 ° C foi 88 segundos para aquecedores de tubo de tungstênio 2kW a 55mm e 219 segundos para elementos FFEH em 100mm
- As temperaturas máximas, as taxas de aquecimento do material alcançáveis e a uniformidade da temperatura da superfície são uma forte função da distância em que os aquecedores são montados a partir do material.
- Excelente penetração no infravermelho e, portanto, equalização de temperatura, através da espessura do material, de PPS e PEEK foram alcançados com halogênio de onda média (tungstênio). A equalização de temperatura alcançada com PEKK não foi tão boa quanto com os outros materiais.
- Excelente penetração no infravermelho e equalização de temperatura foram observados no PEEK usando elementos ocos pretos. Esta propriedade não era tão boa quanto para PEKK e PPS.
Com base nos dados de teste acima e nas próximas separações elemento-material que são necessárias para atingir as temperaturas exigidas para formar os materiais em questão, parece que o melhor emissor de infravermelho é o elemento oco preto liso Ceramicx 800W. Embora os tempos para atingir as temperaturas exigidas sejam um pouco maiores que os aquecedores de tungstênio, a maior proximidade dos elementos usados levará a uma melhor uniformidade da temperatura da superfície. Além disso, os elementos cerâmicos foram iniciados a partir da temperatura ambiente e exigiram aproximadamente 12 min para atingir os níveis operacionais. Portanto, esse tempo pode ser reduzido significativamente com o pré-aquecimento dos elementos.
Note-se também que esses resultados são baseados nas amostras que foram disponibilizadas para teste (por exemplo, 1mm e 2mm de espessura). O aquecimento de peças mais espessas pode exigir que mudanças significativas na tecnologia de aquecimento sejam investigadas, a fim de garantir que o perfil de temperatura, através da espessura do material, seja uniforme e adequado para operações de formação subsequentes.
1 Éter poliéter éter cetona
2 Sulfeto de polifenileno
3 Polyetherketoneketone
4 Diferença média entre as superfícies superior e inferior obtidas nos últimos segundos do teste 18.
Aviso Legal
Esses resultados do teste devem ser cuidadosamente considerados antes que determinado tipo de emissor de infravermelho seja determinado a empregar.
Testes repetidos realizados por outras empresas podem não alcançar os mesmos resultados. Diferenças nas condições experimentais podem alterar os resultados. Outras fontes de erro incluem: a marca do emissor empregado, a eficiência do emissor, a energia fornecida, a distância do material testado ao emissor utilizado e o ambiente. Os locais em que a temperatura é medida também podem causar variação nos resultados.