AUTHOR | VYTVORENÉ DÁTUM | VERZIA | ČÍSLO DOKUMENTU |
---|---|---|---|
Peter Marshall | 8 2016 apríla | V1.1 | CC11 - 00101 |
úvod
CCP Gransden sa priblížil k Ceramicxu, aby postavil infračervenú pec na zahrievanie termoplastických materiálov z predimpregnovaných uhlíkových vlákien pre ich formovacie operácie. Tieto testovacie práce sa vykonali ako súčasť funkcií definovaných v návrhu predaja (CSP 000 008). Prvá fáza zahŕňa hodnotenie a výber infračerveného ohrievača pre tento projekt, pričom stanovená minimálna teplota materiálu je 425 ° C.
Popis materiálu
Tri vzorky z dvoch materiálov boli prijaté v kusoch 230 x 230 x 1mm. V týchto prípadoch bola matica PEEK1 a PPS2, Menšia vzorka PEKK3 s rozmermi 200 x 150 x 2mm. Materiál bol pevný, hladký s lesklým čiernym povrchom. Na povrchu vzoriek PEEK a PPS bol viditeľný malý obrazec.
Vzorky PEEK a PPS boli narezané na kúsky 115 x 115 mm. Materiál PEKK bol narezaný na kúsky 100 x 75 mm.
Metóda
Vyhodnotili sa dve odlišné rodiny ohrievačov; halogén (QH a QT) a čierna dutá keramika (FFEH). V každom prípade boli doštičky namontované nad a pod vzorkou materiálu s nastaviteľnou výškou.
FastIR
Montážny systém bol vyrobený tak, aby umožnil montáž dvoch jednotiek Ceramicx FastIR 500 nad a pod materiál. FastIR 500 pozostáva zo siedmich vykurovacích telies namontovaných paralelne do puzdra 500 x 500 mm. Rozstup medzi týmito rúrkami je 81mm. Boli použité prvky 1500W a 2000W „dlhé“ (celková dĺžka: 473mm), ktoré poskytujú celkový výstup z dvoch jednotiek 21 alebo 28kW. Ohrievacie jednotky boli namontované tak, že vzdialenosť medzi povrchom prvku a vzorkou bola menená medzi 55mm a 95mm.
Použitý experimentálny protokol bol nasledujúci:
- Zapnuté ventilátory
- Zapnuté sú tri vykurovacie telesá, hore a dole
- Mimo zapnutých štyroch vykurovacích telies, hore a dole
Obrázok vzorky medzi dvoma jednotkami FastIR je znázornený na obrázku 1. Na uzatvorenie medzery medzi dvoma vykurovacími jednotkami sa nepoužilo nič
Prvky
Do jednotky FastIR môžu byť namontované dva typy prvkov; kremičitý halogén a volfrám. Tieto prvky emitujú rôzne infračervené vlnové dĺžky; halogén približne pri 1.0 - 1.2μm a volfrám medzi 1.6 - 1.9μm. Každá trubica má priemer 10mm, celkovú dĺžku 473mm a zahrievanú dĺžku 415mm.
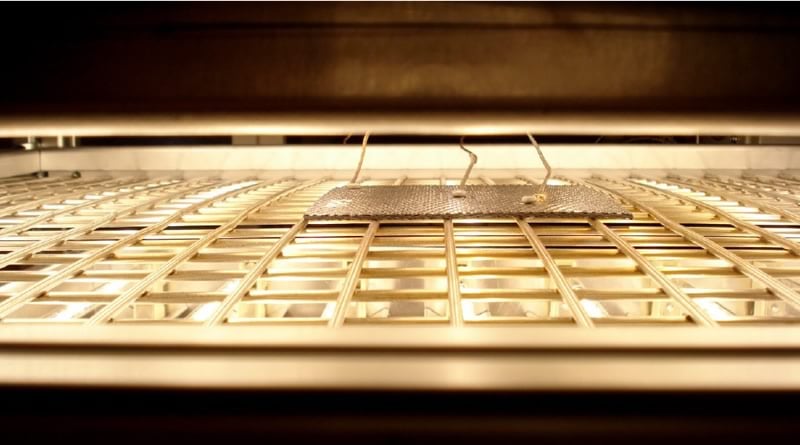
Black Hollow
Vlastná vyhrievacia doska bola navrhnutá tak, aby obsahovala maticu 2 x 7 prvkov 800W FFEH od Ceramicx, čo dáva každej doske 11.2kW silu. Táto matica bola uzavretá v puzdre 510 x 510mm a namontovaná v rovnakom rámci ako systém FastIR uvedený vyššie. Použil sa experimentálny protokol; na týchto doskách sa však nepoužívali ventilátory. Vzdialenosť medzi týmito prvkami bola 65mm.
Boli použité dve rôzne vzdialenosti prvkov - 50 a 100mm. Medzera medzi dvoma vykurovacími jednotkami bola opäť ponechaná otvorená
Prvky
Duté čierne prvky Ceramicx emitujú vrcholové vlnové dĺžky v strednom až dlhodobom režime (2 - 10μm). Každý prvok má rozmery 245 x 60mm (lxw). Dlhšie vlnové dĺžky spojené s keramickými prvkami sú veľmi účinné na zahrievanie mnohých polymérnych materiálov.
inštrumentácie
Termočlánky typu K sa pripevnili na povrch vzorky pomocou skrutiek M3. Keramický cement bol skúšaný, ale to nelepilo na povrch materiálu. Vzhľadom na požadované vysoké teploty by žiadne dostupné lepidlo nezostalo stabilné, a preto sa považovala za nevyhnutnú mechanická fixácia. Termočlánky boli umiestnené v strede každej vzorky a tiež 10mm (okraj) a 30mm (štvrtina) od okraja, ako je znázornené na obrázku 2. To umiestnilo termočlánky priamo nad rúrkové prvky a v strede medzi prvkami tak, aby sa zaznamenal maximálny teplotný rozdiel. Údaje o teplote sa zaznamenávali v intervaloch jednej sekundy.
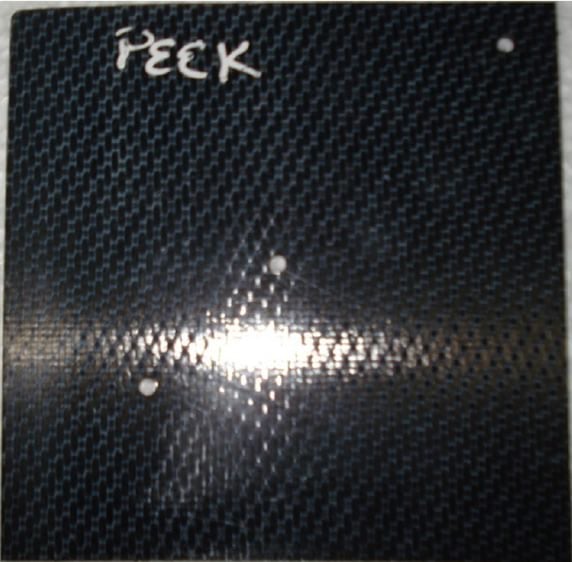
Sendvičové testovanie
Sendvičový tester je pokročilý prístroj na testovanie tepelnej odozvy materiálu, ako je znázornené na obrázku 2. Rôzne typy infračervených ohrievačov je možné namontovať v dvoch polohách otočených zvisle nahor a nadol. To zaisťuje, že testovaný materiál môže byť zahrievaný zhora a / alebo zdola. Na stanovenie hornej a dolnej povrchovej teploty testovaného materiálu sa používajú štyri bezkontaktné optické pyrometre. Emisie sa nechajú zahriať na svoju prevádzkovú teplotu a materiál sa potom na vopred určenú dobu privedie pod žiarič (e). Tento test sa uskutočňoval s 1kW volfrámom (QTM) a 800W čiernymi dutými prvkami (FFEH) namontovanými 75mm nad vzorkou, aby sa určilo, ktorý ohrievač poskytol najlepší prienik materiálom.
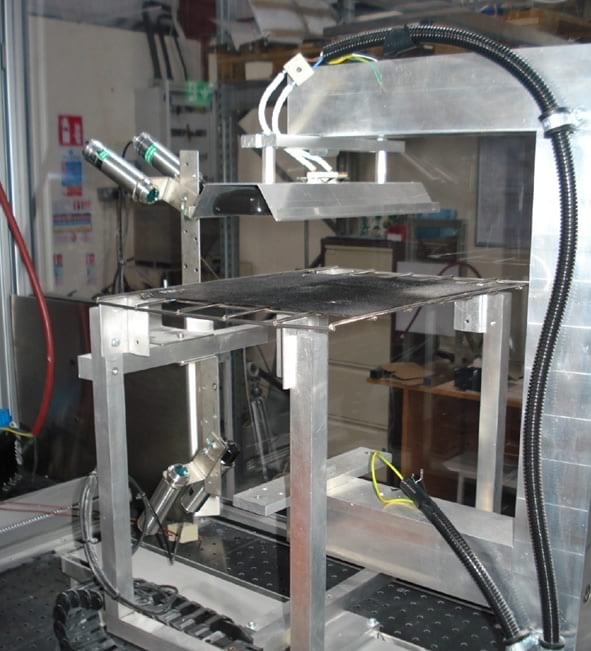
výsledky
FastIR
V tejto časti sa uvádzajú výsledky zistené pre volfrámové a halogénové trubice pre tri príslušné materiály. Testy sa uskutočňovali s tromi rôznymi výškami ohrievača (55 mm, 80 mm a 95 mm).
PEEK
Počiatočné skúšky sa uskutočňovali so vzorkou PEEK a dvoma ohrievačmi FastIR s kremennými halogénovými skúmavkami 1500W oddelenými 110mm. Výsledky tohto testu, znázornené na obrázku 4, naznačujú, že vzorka nedosiahla požadovanú teplotu.
Prvky sa zmenili na krátkovlnné halogénové trubice 2000W (QHL), ktoré ukázali, že pri rovnakej separácii vzorka dosiahla a prekročila požadovanú teplotu na jednom mieste. V tomto prípade bola maximálna zaznamenaná teplota 485 ° C, boli však tiež zistené významné teplotné rozdiely (až do 83 ° C). Čas potrebný na dosiahnutie cieľovej teploty 425 ° C bol 99 sekúnd. To sa dosiahlo iba na dvoch miestach
Skúmavky z kremenného volfrámu (QTL) (2000W) sa skúmali aj na troch úrovniach s maximálnou teplotou klesajúcou so zvyšujúcou sa vzdialenosťou ohrievača. Pri 55 mm bola zistená maximálna a minimálna teplota 520 ° C. Cieľová teplota naprieč vzorkou materiálu sa dosiahla za 206 sekúnd. Zvýšením vzdialenosti na 80mm sa tieto znížili na 450 ° C a 415 ° C a pri 95mm nad vzorkou, maximálna a minimálna teplota vzorky bola 407 a 393 ° C.
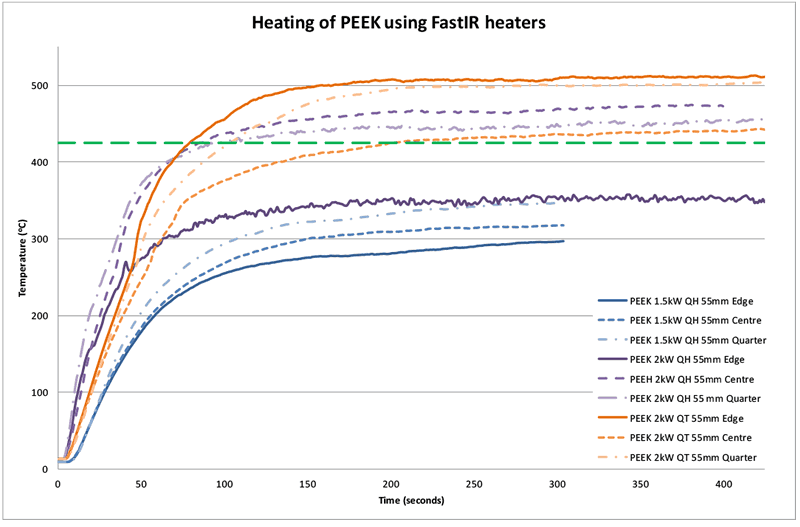
Obrázok 4 ukazuje kolísanie teploty, ktoré môže nastať naprieč vzorkou v dôsledku tesnej blízkosti ohrievačov voči vzorke, ako aj času potrebného na zahriatie materiálu na 425 ° C (206 sekúnd pre 2kW QT ohrievač).
Volfrámové rúry 150 ° W sa netestovali, pretože sa z hľadiska prevádzky považovalo za dôležitejšie zväčšiť vzdialenosť ohrievača ako znížiť výkon použitých prvkov.
Obrázok 5 ukazuje vizuálny rozdiel vo vzorke pred a po zahriatí.
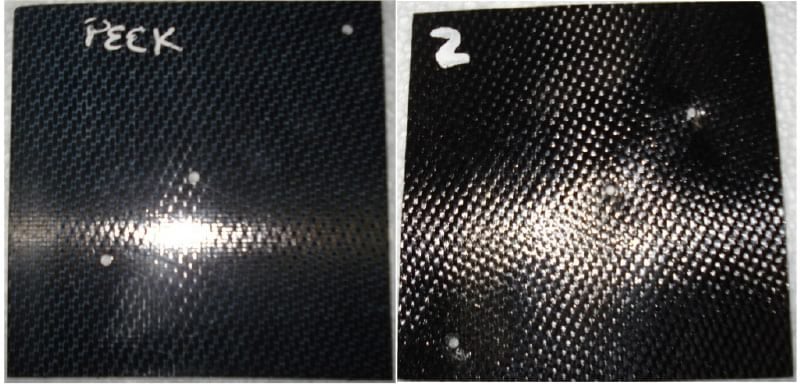
Pekka
PEKK bol ohrievaný volfrámovými ohrievačmi 2000W iba na 55mm. Tepelná odozva materiálu bola vynikajúca pri zaznamenávaní teplôt nad 500 ° C. Minimálna stanovená teplota sa dosiahla v 102 sekundách, pričom maximálna zaznamenaná teplota presahovala 500 ° C.
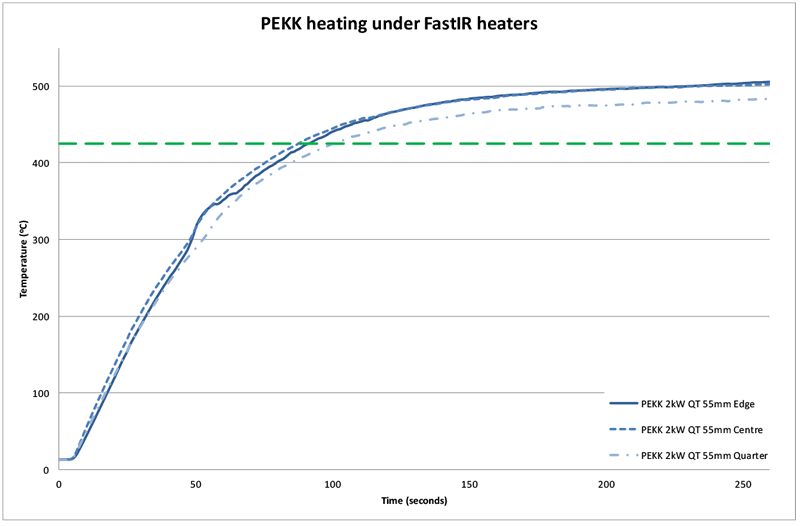
Bolo zrejmé, že táto vzorka vykazovala určité rozštiepenie a delamináciu na okrajoch a tiež určité deformácie povrchu po zahriatí, ako je znázornené na obrázku 7, pravdepodobne z absorpcie vlhkosti počas skladovania a rýchleho zahrievania, ku ktorému došlo.
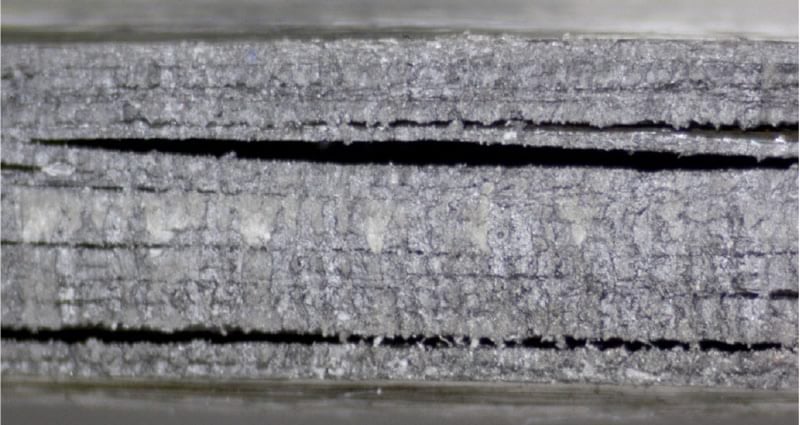
PPS
Materiál PPS bol testovaný pomocou halogénových a volfrámových ohrievačov 2000W. Halogénový test sa uskutočňoval so separáciou 55mm a volfrámové testy pri 55mm a 95mm.
Dáta opäť ukázali, že volfrámová trubica bola pre tento materiál lepší ohrievač (ako halogénový ohrievač), pričom vyššie teploty boli zaznamenávané pri 55mm separácii a tiež väčšia rovnomernosť teploty vo vzorke. Bola zaznamenaná zmena teploty 38 ° C pre halogénové ohrievače a 30 ° C pre volfrámové ohrievače. Táto zaznamenaná zmena bude vysoko ovplyvnená polohou termočlánku vzhľadom na skúmavky. Identické polohy termočlánkov nie sú zaručené.
Testy s PPS boli ukončené krátko potom, ako materiál dosiahol požadovanú teplotu 425 ° C, pretože zo vzoriek sa uvoľňovali výpary, ktoré vonia sírou.
Vo vzdialenosti 55mm bola cieľová teplota zaznamenaná po 66 a 88 sekundách pre halogénové a volfrámové ohrievače pri 55mm. Keď boli volfrámové ohrievače namontované na 95mm zo vzorky, cieľová teplota nebola dosiahnutá.
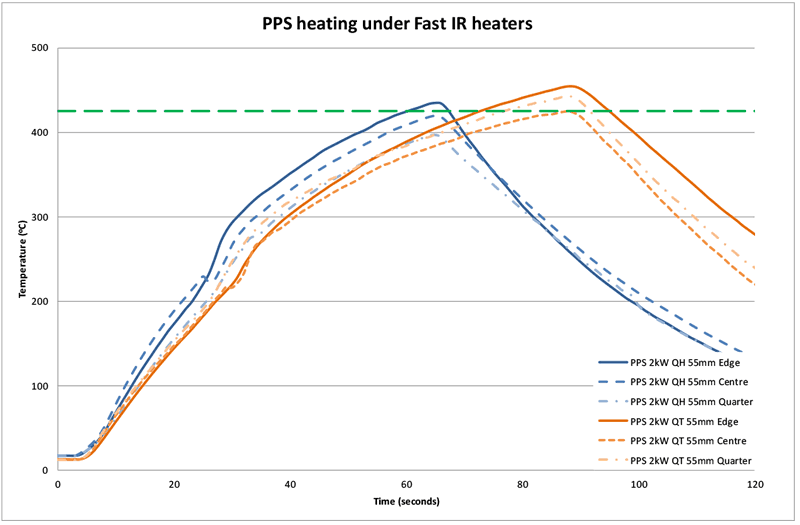
Black Hollow
Počiatočné testy sa uskutočňovali so separáciou prvkov a materiálov 50mm. Zvýšenie teploty materiálu bolo veľmi rýchle pre všetky materiály. Od studeného štartu trvajú duté prvky približne 10-12 minút, kým sa zahrievajú na stabilnú prevádzkovú úroveň (teplota povrchu približne 700 ° C). Zvýšenie teploty materiálu bolo zhruba podobné krivke zahrievania ohrievača, avšak v tom došlo k časovému oneskoreniu.
PEEK
Graf času potrebného na zahriatie vzorky PEEK na dosiahnutie požadovanej teploty spracovania je uvedený nižšie na obrázku 9. To ukazuje, že čas ohrevu na 425 ° C je približne 185 sekúnd od zapnutia ohrievačov na 50mm. Ak sa vzdialenosť zvýši na 100mm, čas sa zvýši na 230 s. Počas zahrievania bola vzorka ponechaná medzi oboma doskami a odstránená na ochladenie.
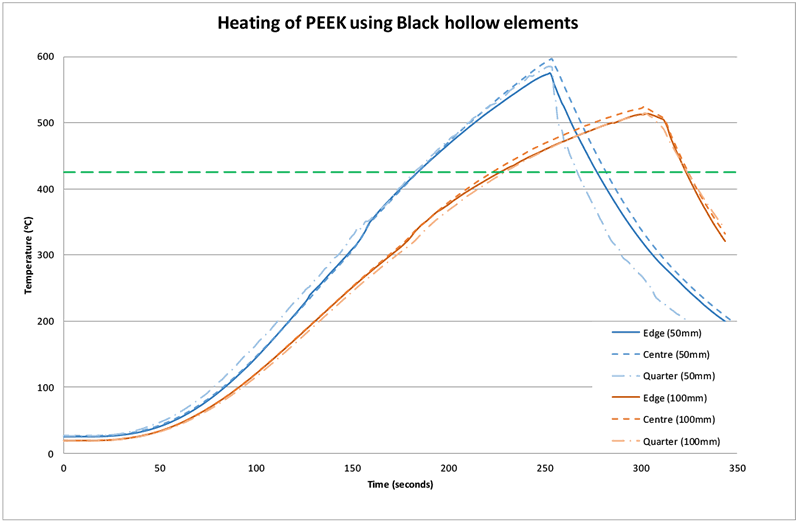
Pekka
Čas potrebný na dosiahnutie minimálneho prahu PEKK bol o niečo dlhší ako v prípade PEEK. Existujú dva možné dôvody: 1.) Materiál neabsorbuje infračervené žiarenie, ako aj PEEK a 2.) Hrúbka materiálu je dvakrát väčšia (1 a 2mm). Čas potrebný na dosiahnutie 425 ° C pri 50mm bol 181 sekúnd a pri 100mm sa tento čas zvýšil na 244 sekúnd
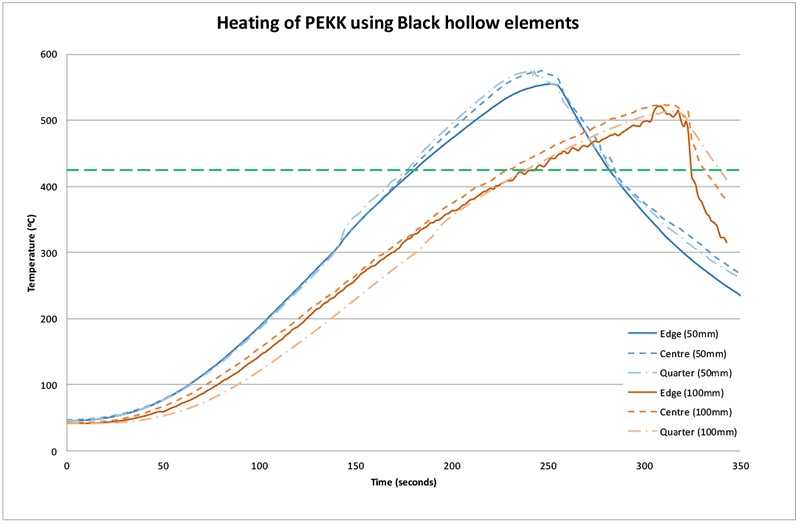
PPS
PPS sa veľmi úspešne zahrievala, pričom čierne duté prvky s 425 ° C sa zaznamenávali v sekundách 171 a 219 v sekundách 50 a 100mm. Vykurovacia krivka pre tento materiál je znázornená na obrázku 11. Opäť došlo k uvoľňovaniu dymu zapáchajúceho síru, avšak jeho množstvo nebolo také veľké ako u halogénových ohrievačov, ako je podrobne uvedené vyššie. To môže byť čiastočne spôsobené neprítomnosťou ventilátorov na zadnej strane vyhrievacej dosky.
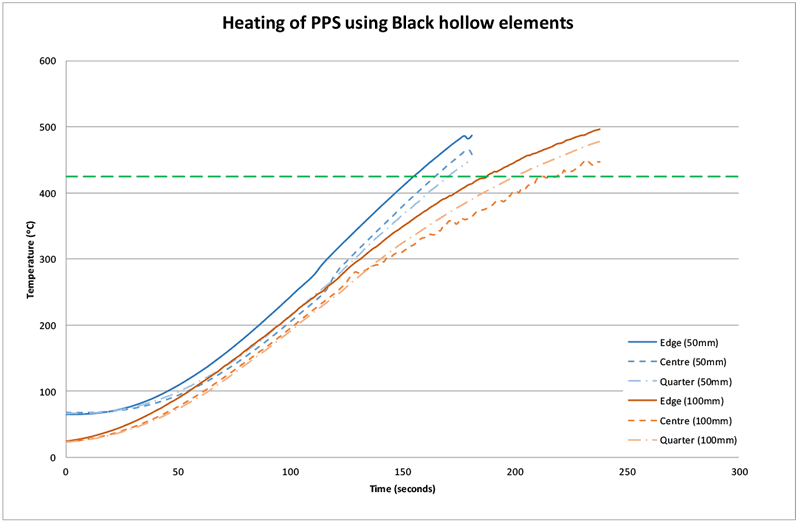
Zhrnutie časov potrebných na zahriatie materiálov s halogénovými, volfrámovými a dutými keramickými prvkami na cieľovú teplotu je uvedené nižšie v tabuľke 1. Pretože montáž halogénových prvkov na dlhšie vzdialenosti ako 55mm nebola všeobecne úspešná, boli tieto výsledky z tabuľky vynechané.
Materiál |
Typ ohrievača (výkon)
|
vzdialenosť | Čas na dosiahnutie 425 ° C |
---|---|---|---|
PEEK | QHL (2kW) | 55mm | 99 |
QTL (2kW) | 55mm | 206 | |
FFEH (800W) | 50mm | 185 | |
FFEH (800W) | 100mm | 230 | |
Pekka | QTL (2kW) | 55mm | 102 |
FFEH (800W) | 50mm | 181 | |
FFEH (800W) | 100mm | 244 | |
PPS | QHL (2kW) | 55mm | 66 |
QTL (2kW) | 55mm | 88 | |
FFEH (800W) | 50mm | 171 | |
FFEH (800W) | 100mm | 219 |
Sendvičové testovanie
Uskutočnilo sa sendvičové testovanie, aby sa získali informácie o prenose tepla cez materiál. To sa uskutočnilo zahriatím vzorky z jednej strany, meraním teploty na oboch stranách a porovnaním výsledkov. Skúmali sa iba volfrámové trubice a čierne duté prvky, pretože na základe výsledkov FastIR nie sú krátkovlnné halogénové trubice vhodným ohrievačom pre dané materiály.
Výsledky prvkov QTM ukazujú, že pri materiáloch PEEK a PPS neexistuje výrazný teplotný rozdiel medzi hornou a spodnou plochou, avšak PPS sa zahrieva rýchlejšie a krivky pre tento materiál sú prakticky nerozoznateľné. Je potrebné poznamenať, že tieto dva materiály sú veľmi tenké (≈ 1mm). Ako sa očakávalo, teplotný rozdiel pre PEKK bol väčší (75 ± 2oC) kvôli jeho hrúbke (≈ 2mm). Tieto výsledky sú uvedené na obrázku 12 nižšie.
Z prevádzkových dôvodov sa test ukončí, keď pyrometre zistia teplotu 300 ° C. Vrcholom pozorovaným v prvých 30 sekundách testu je odrazivosť a nejde o skutočnú teplotu.
Tieto výsledky ukazujú, že pri PEEK a PPS s použitím volfrámového typu je možné dobré prenikanie materiálu do IR. Vyrovnanie teploty pre PEKK však nie je také dobré, čo dokazuje takmer teplotný rozdiel 75 ° C v posledných 18 sekundách testu4.
Nebolo možné presunúť vzorky materiálu bližšie k ohrievaču, aby sa analyzovalo, aký účinok by to malo, pretože ostrý uhol potrebný na to, aby pyrometer videl, že materiál skreslí odčítanie.
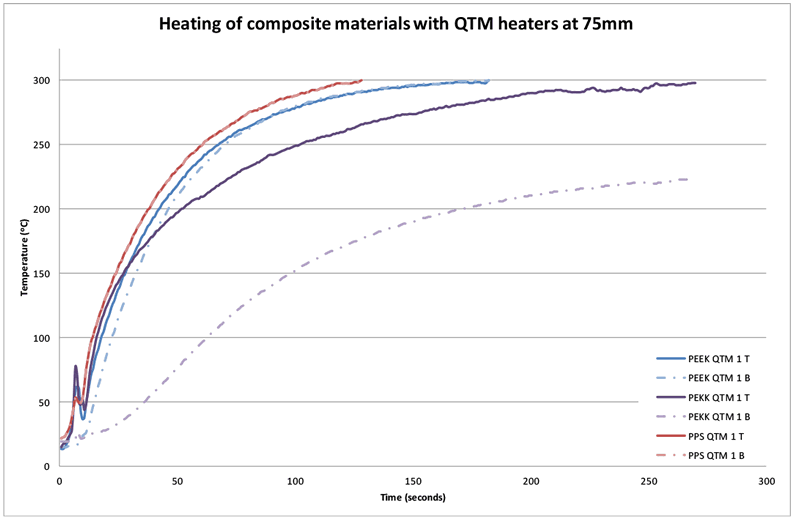
Zahrievanie vzoriek s čiernymi dutými prvkami v rovnakej vzdialenosti (75mm) ukazuje podobný trend s väčším teplotným rozdielom (45 ± 2 ° C), ktorý sa pozoruje pre hrubší materiál PEKK (v porovnaní s tenšími materiálmi). Teploty horného a spodného povrchu PEEK sú prakticky nerozoznateľné; je tu však rozdiel v teplote PPS (25 ± 2 ° C). Tieto údaje sú zobrazené na obrázku 13. To naznačuje, že IR penetrácia PPS s ožarovaním s dlhšou vlnovou dĺžkou nie je tak dobrá ako pri IR s volfrámom s kratšou vlnovou dĺžkou, avšak teplotné vyrovnanie PEKK je lepšie (ale nie ideálne).
Pri separácii 75mm sa najvyššie teploty a rýchlosti zahrievania získajú pomocou volfrámového ohrievača, ktorý sa zdá byť v rozpore s predchádzajúcimi výsledkami platne. Toto by sa však nemalo používať ako vodítko, pretože sa použil iba jeden ohrievač. Okrem toho sa tieto vlastnosti zlepšia použitím radu ohrievačov na rozdiel od jediného ohrievača.
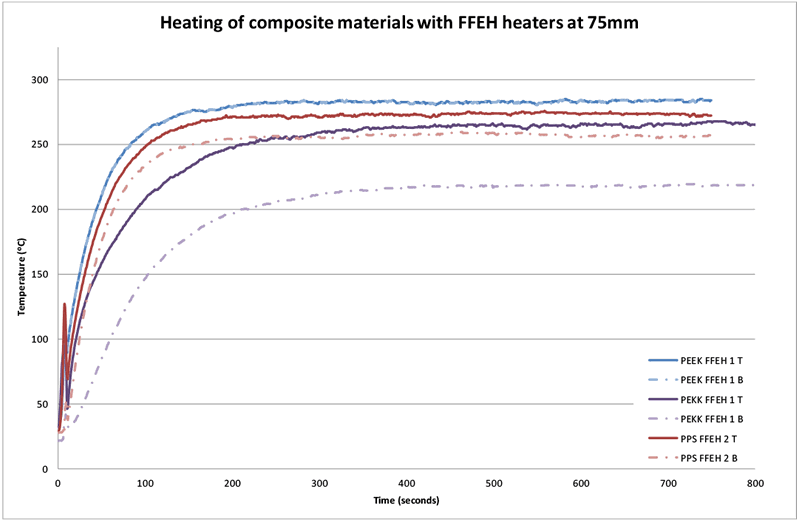
záver
- Testy, ktoré sa uskutočnili a podrobne sa uvádzajú vyššie, naznačujú, že je možné zahrievanie troch termoplastických uhlíkových kompozitných materiálov na minimum 425 ° C s halogénovými prvkami so strednou vlnou aj s čiernymi dutými prvkami.
- Vyššie maximálne teploty sa dajú dosiahnuť použitím čierneho dutého prvku Ceramicx 800W (FFEH).
- Čas potrebný na zahriatie PEEK na 425 ° C bol 206 s pre ohrievače volfrámových rúr 2kW pri 55mm a 230 s pre FFEH prvky pri 100mm
- Čas potrebný na zahriatie PEKK na 425 ° C bol 102 sekúnd pre ohrievače volfrámových rúr 2kW pri 55mm a 244 sekúnd pre FFEH prvky pri 100mm
- Čas potrebný na zahriatie PPS na 425 ° C bol 88 sekúnd pre ohrievače volfrámových rúr 2kW pri 55mm a 219 sekúnd pre FFEH prvky pri 100mm
- Maximálne dosiahnuteľné teploty, rýchlosti ohrevu materiálu a rovnomernosť povrchovej teploty sú silnou funkciou vzdialenosti, v ktorej sú ohrievače namontované od materiálu.
- Vynikajúca penetrácia infračerveným žiarením a teda vyrovnanie teploty PPS a PEEK prostredníctvom hrúbky materiálu sa dosiahli stredne vlnovým halogénom (volfrám). Vyrovnanie teploty dosiahnuté pomocou PEKK nebolo také dobré ako pri iných materiáloch.
- Vynikajúca penetrácia IR a vyrovnanie teploty sa pozorovali pri PEEK s použitím čiernych dutých prvkov. Táto nehnuteľnosť nebola tak dobrá ako v prípade PEKK a PPS.
Na základe vyššie uvedených testovacích údajov a úzkych separácií jednotlivých prvkov, ktoré sú potrebné na dosiahnutie teplôt požadovaných na vytvorenie daných materiálov, sa javí ako najlepší infračervený žiarič Ceramicx 800W čierny plochý plochý dutý prvok. Kým časy na dosiahnutie požadovaných teplôt sú o niečo dlhšie ako volfrámové ohrievače, bližšia blízkosť použitých prvkov povedie k lepšej rovnomernosti povrchovej teploty. Ďalej sa keramické prvky začali od teploty miestnosti a vyžadovali približne 12 minút, aby dosiahli prevádzkovú úroveň. Preto by sa tento čas mohol predhriatím prvkov značne skrátiť.
Malo by sa tiež poznamenať, že tieto výsledky sú založené na vzorkách, ktoré boli sprístupnené na testovanie (tj hrúbka 1mm a 2mm). Zahrievanie hrubších častí môže vyžadovať preskúmanie významných zmien v technológii zahrievania, aby sa zabezpečilo, že teplotný profil po celej hrúbke materiálu je rovnomerný a vhodný na následné formovacie operácie.
1 Polyetyléterketón
2 Polyfenylénsulfid
3 Polyetherketoneketone
4 Priemerný rozdiel medzi horným a dolným povrchom odobratým za posledných 18 sekúnd testu.
Vylúčenie zodpovednosti
Tieto výsledky skúšok by sa mali starostlivo zvážiť skôr, ako sa rozhodne, že určitý typ infračerveného žiariča použije.
Opakované testy vykonané inými spoločnosťami nemusia dosiahnuť rovnaké zistenia. Rozdiely v experimentálnych podmienkach môžu zmeniť výsledky. Medzi ďalšie zdroje chýb patria: použitá značka žiariča, účinnosť žiariča, dodávaná energia, vzdialenosť od testovaného materiálu k použitému žiariči a prostredie. Miesta, v ktorých sa teplota meria, môžu tiež spôsobiť zmeny vo výsledkoch.