ผู้แต่ง | วันที่สร้าง | VERSION | หมายเลขเอกสาร |
---|---|---|---|
ดร. ปีเตอร์มาร์แชล | 8 เมษายน 2016 | V1.1 | CC11 - 00101 |
บทนำ
CCP Gransden เข้าหา Ceramicx เพื่อสร้างเตาอบอินฟราเรดเพื่อให้ความร้อนกับวัสดุพรีเรกคาร์บอนไฟเบอร์แบบเทอร์โมพลาสติกสำหรับการขึ้นรูป งานทดสอบนี้ดำเนินการโดยเป็นส่วนหนึ่งของฟังก์ชันที่กำหนดไว้ในข้อเสนอการขาย (CSP 000 008) ระยะที่หนึ่งเกี่ยวข้องกับการประเมินและการเลือกฮีตเตอร์อินฟราเรดสำหรับโครงการนี้โดยอุณหภูมิของวัสดุขั้นต่ำที่กำหนดไว้คือ 425 ° C
คำอธิบายวัสดุ
ตัวอย่างวัสดุสองชิ้นได้รับเป็นชิ้น 230 x 230 x 1mm ในกรณีเหล่านี้เมทริกซ์คือ PEEK1 และ PPS2. ตัวอย่างเล็ก ๆ ของ PEKK3 ด้วยขนาดของ 200 x 150 x 2mm ก็ได้รับเช่นกัน วัสดุมีความแข็งเรียบเนียนด้วยพื้นผิวสีดำมันวาว รูปแบบขนาดเล็กสามารถมองเห็นได้บนพื้นผิวบนพื้นผิวของตัวอย่าง PEEK และ PPS
ตัวอย่าง PEEK และ PPS ถูกตัดเป็นชิ้น 115 x 115 วัสดุ PEKK ถูกตัดเป็นชิ้นส่วน 100 x 75mm
วิธี
ครอบครัวฮีตเตอร์ที่แตกต่างกันสองครอบครัวได้รับการประเมิน ฮาโลเจน (QH และ QT) และเซรามิกฮอลโลว์ดำ (FFEH) ในแต่ละกรณีแผ่นโลหะจะถูกติดตั้งด้านบนและด้านล่างของตัวอย่างวัสดุที่มีความสูงที่สามารถปรับได้
FastIR
ระบบติดตั้งได้รับการผลิตขึ้นเพื่ออนุญาตให้หน่วย FastIR 500 ของ Ceramicx สองตัวติดตั้งด้านบนและด้านล่างของวัสดุ FastIR 500 ประกอบด้วยเจ็ดองค์ประกอบความร้อนที่ติดตั้งในแบบคู่ขนานภายในเคส 500 x 500 มม. ระยะห่างระหว่างหลอดเหล่านี้คือ 81mm องค์ประกอบ 1500W และ 2000W 'ยาว' (ความยาวทั้งหมด: 473mm) ถูกใช้เพื่อให้เอาต์พุตทั้งหมดจากสองหน่วยของ 21 หรือ 28kW ตามลำดับ ชุดฮีตเตอร์ถูกติดตั้งเพื่อให้ระยะห่างระหว่างพื้นผิวองค์ประกอบและตัวอย่างแตกต่างกันระหว่าง 55mm และ 95mm
โปรโตคอลทดลองที่ใช้มีดังนี้:
- แฟน ๆ เปิดอยู่
- มีการเปิดองค์ประกอบความร้อนส่วนกลางสามจุดด้านบนและด้านล่าง
- มีการเปิดองค์ประกอบความร้อนสี่ด้านนอกด้านบนแล้วด้านล่าง
ภาพตัวอย่างระหว่างหน่วย FastIR ทั้งสองจะแสดงในรูปที่ 1 ไม่มีสิ่งใดถูกใช้เพื่อใส่ช่องว่างระหว่างชุดทำความร้อนทั้งสอง
องค์ประกอบ
องค์ประกอบสองประเภทสามารถติดตั้งในหน่วย FastIR ควอทซ์ฮาโลเจนและควอทซ์ทังสเตน องค์ประกอบเหล่านี้ปล่อยความยาวคลื่นอินฟาเรดสูงสุดที่แตกต่างกัน ฮาโลเจนที่ประมาณ 1.0 - 1.2μmและทังสเตนระหว่าง 1.6 - 1.9μm แต่ละหลอดมีเส้นผ่านศูนย์กลาง 10mm ความยาวรวม 473mm และความยาวความร้อน 415mm
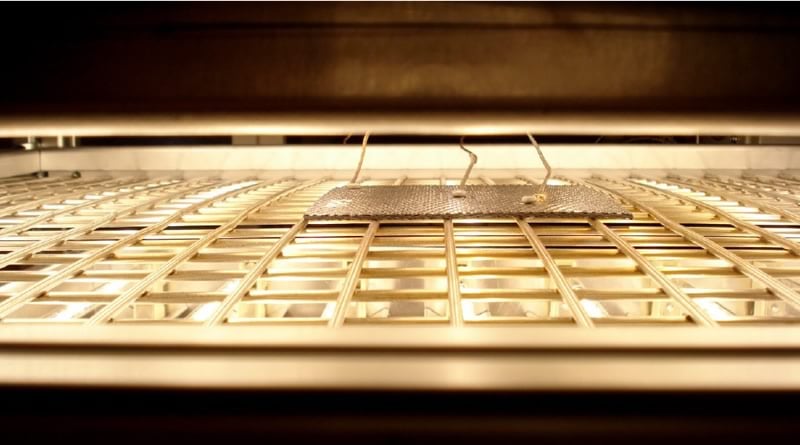
ฮอลโลว์สีดำ
แผ่นความร้อนที่กำหนดเองได้รับการออกแบบเพื่อรวมเมทริกซ์ 2 x 7 ขององค์ประกอบ 800W FFEH ของ Ceramicx ให้พลัง 11.2kW แต่ละแผ่น เมทริกซ์นี้อยู่ในเคส 510 x 510mm และติดตั้งในเฟรมเดียวกับระบบ FastIR ที่มีรายละเอียดด้านบน ใช้โปรโตคอลการทดลอง; แม้กระนั้นแฟน ๆ ไม่ได้ใช้ในแผ่นเหล่านี้ ระยะห่างระหว่างองค์ประกอบเหล่านี้คือ 65mm
ใช้ระยะทางตัวอย่างองค์ประกอบที่แตกต่างกันสองแบบคือ 50 และ 100mm อีกครั้งช่องว่างระหว่างชุดทำความร้อนทั้งสองถูกเปิดทิ้งไว้
องค์ประกอบ
องค์ประกอบกลวงของ Ceramicx ดำปล่อยความยาวคลื่นสูงสุดในระดับปานกลางถึงยาว (2 - 10μm) แต่ละองค์ประกอบมีขนาดเป็น 245 x 60mm (lxw) ความยาวคลื่นอีกต่อไปที่เกี่ยวข้องกับองค์ประกอบเซรามิกมีประสิทธิภาพมากสำหรับการทำความร้อนวัสดุโพลีเมอจำนวนมาก
การประพันธ์ดนตรี
เทอร์โมคัปเปิลชนิด K ติดอยู่ที่ผิวของตัวอย่างโดยใช้สกรู M3 ซีเมนต์เซรามิกนั้นถูก trialled แต่สิ่งนี้ไม่ได้ยึดติดกับพื้นผิวของวัสดุ เนื่องจากอุณหภูมิที่ต้องการสูงไม่มีกาวที่สามารถคงอยู่ได้ดังนั้นจึงจำเป็นต้องทำการยึดทางกล เทอร์โมคับเปิลตั้งอยู่ที่กึ่งกลางของชิ้นงานแต่ละชิ้นและ 10mm (edge) และ 30mm (ไตรมาส) จากขอบดังแสดงในรูปที่ 2 เทอร์โมคัปเปิลตั้งอยู่ที่ตำแหน่งของเทอร์โมคับเปิลโดยตรงและตรงกลางระหว่างชิ้นส่วนเพื่อบันทึกความแตกต่างของอุณหภูมิสูงสุด ข้อมูลอุณหภูมิถูกบันทึกในช่วงเวลาวินาทีเดียว
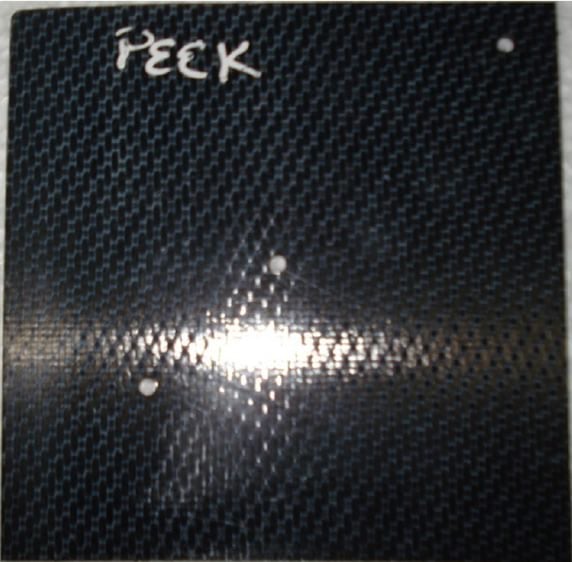
การทดสอบแซนวิช
เครื่องทดสอบแซนวิชเป็นเครื่องทดสอบการตอบสนองต่อความร้อนของวัสดุขั้นสูงดังแสดงในรูปที่ 2 เครื่องทำความร้อนอินฟราเรดชนิดต่าง ๆ สามารถติดตั้งได้ในสองตำแหน่งโดยหันขึ้นและลงในแนวตั้ง สิ่งนี้ทำให้มั่นใจได้ว่าวัสดุที่ทดสอบสามารถถูกทำให้ร้อนจากด้านบนและ / หรือด้านล่าง ออปติคัล pyrometers แบบไม่สัมผัสสี่แบบใช้เพื่อกำหนดอุณหภูมิพื้นผิวด้านบนและด้านล่างของวัสดุที่ทำการทดสอบ ตัวปล่อยความร้อนได้รับอนุญาตให้อุ่นขึ้นจนถึงอุณหภูมิในการทำงานของพวกเขาและจากนั้นวัสดุจะถูกนำไปอยู่ภายใต้ตัวปล่อย (emitter) เป็นระยะเวลาที่กำหนดไว้ การทดสอบนี้ดำเนินการกับทั้ง 1kW ทังสเตน (QTM) และ 800W องค์ประกอบกลวงสีดำ (FFEH) ติดตั้ง 75mm เหนือตัวอย่างเพื่อตรวจสอบว่าฮีตเตอร์ใดให้การแทรกซึมที่ดีที่สุดผ่านวัสดุ
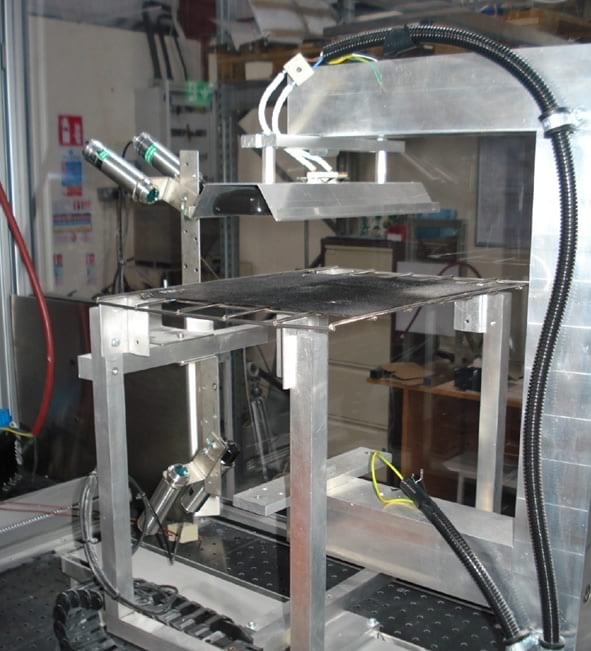
ผลสอบ
FastIR
ส่วนนี้รายงานเกี่ยวกับผลลัพธ์ที่พบสำหรับหลอดทังสเตนและหลอดฮาโลเจนสำหรับวัสดุทั้งสามที่เป็นปัญหา ทำการทดสอบด้วยความสูงของฮีตเตอร์ที่แตกต่างกันสามแบบ (55 มม., 80 มม. และ 95 มม.)
PEEK
การทดลองเริ่มต้นดำเนินการกับตัวอย่าง PEEK และเครื่องทำความร้อน FastIR สองเครื่องที่มีหลอดฮาโลเจนควอทซ์ 1500W คั่นด้วย 110mm ผลการทดสอบนี้แสดงในรูปที่ 4 บ่งชี้ว่าตัวอย่างไม่สามารถไปถึงอุณหภูมิที่ต้องการ
องค์ประกอบถูกเปลี่ยนเป็นหลอด XHUMXW หลอดฮาโลเจน (QHL) 2000W ซึ่งแสดงให้เห็นว่าในการแยกตัวเดียวกันกลุ่มตัวอย่างมาถึงและเกินอุณหภูมิที่ต้องการในที่เดียว ในกรณีนี้อุณหภูมิสูงสุดที่บันทึกไว้คือ 485 ° C อย่างไรก็ตามตรวจพบความแตกต่างของอุณหภูมิอย่างมีนัยสำคัญ (สูงสุด 83 ° C) เวลาที่ใช้ในการเข้าถึงอุณหภูมิเป้าหมายของ 425 ° C คือ 99 วินาที สิ่งนี้สามารถทำได้ในสองสถานที่เท่านั้น
หลอดควอทซ์ทังสเตน (QTL) (2000W) ได้รับการตรวจสอบในสามระดับด้วยอุณหภูมิสูงสุดที่ตกลงมาเมื่อระยะทางของฮีตเตอร์เพิ่มขึ้น ที่ 55mm ตรวจพบอุณหภูมิสูงสุดและต่ำสุดที่ 520 ° C อุณหภูมิเป้าหมายในตัวอย่างวัสดุนั้นทำได้ใน 206 วินาที การเพิ่มระยะทางถึง 80mm ซึ่งจะลดลงเป็น 450 ° C และ 415 ° C และที่ 95mm เหนือตัวอย่างอุณหภูมิสูงสุดและอุณหภูมิต่ำสุดของตัวอย่างคือ 407 และ 393 ° C
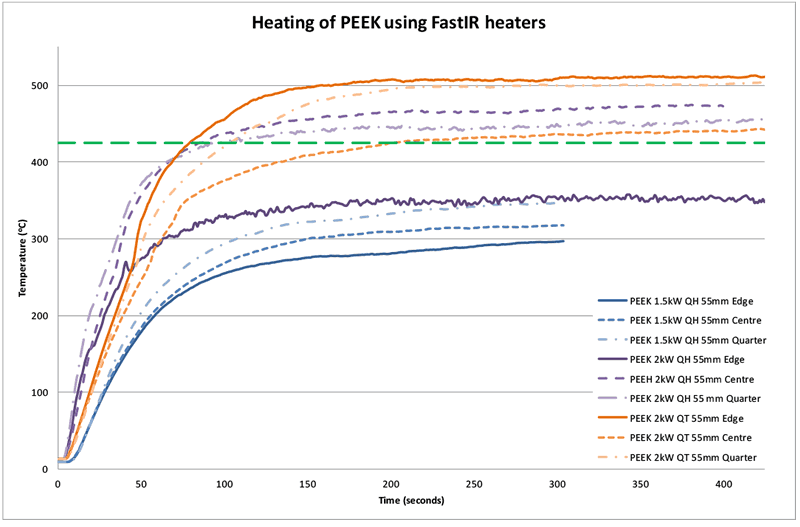
รูปที่ 4 แสดงความแปรปรวนของอุณหภูมิที่สามารถเกิดขึ้นได้ในตัวอย่างเนื่องจากความใกล้เคียงของเครื่องทำความร้อนกับตัวอย่างรวมถึงเวลาที่ต้องใช้ในการให้ความร้อนกับวัสดุถึง 425 ° C (206 วินาทีสำหรับ 2kW QT heater)
150 ° W ไม่ได้ทำการทดสอบหลอดทังสเตนเนื่องจากมันถือว่ามีความสำคัญในการใช้งานเพื่อเพิ่มระยะทางของฮีตเตอร์มากกว่าการลดกำลังขององค์ประกอบที่ใช้
รูปที่ 5 แสดงความแตกต่างของภาพในตัวอย่างก่อนและหลังการให้ความร้อน
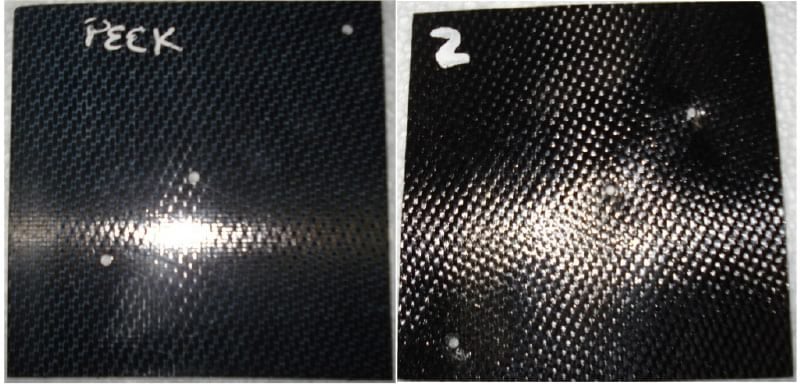
พีเคเค
PEKK ถูกทำให้ร้อนด้วยเครื่องทำความร้อนทังสเตน 2000W ที่ 55mm เท่านั้น การตอบสนองต่อความร้อนของวัสดุนั้นยอดเยี่ยมโดยมีอุณหภูมิเกิน 500 ° C ที่ถูกบันทึกไว้ อุณหภูมิต่ำสุดที่กำหนดนั้นทำได้ใน 102 วินาทีโดยที่อุณหภูมิสูงสุดที่บันทึกนั้นเกิน 500 ° C
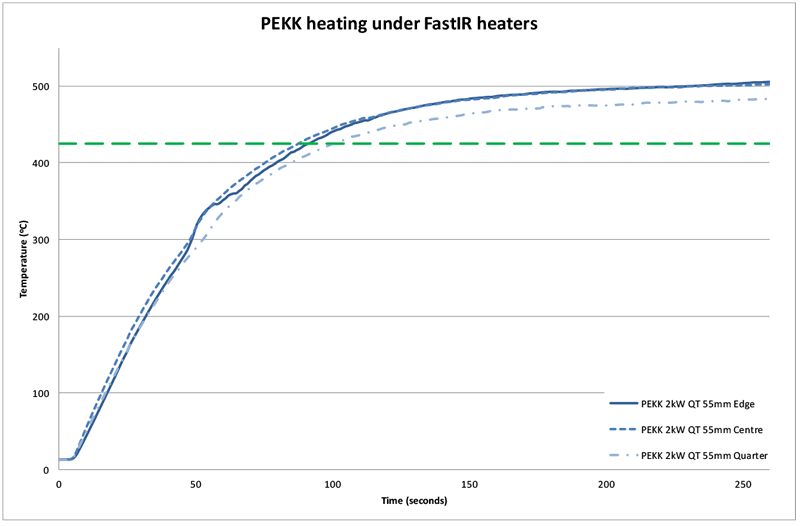
เป็นที่น่าสังเกตว่าตัวอย่างนี้ดูเหมือนจะมีรอยแยกและรอยแยกที่ขอบและมีการบิดเบือนพื้นผิวบางอย่างหลังจากความร้อนดังแสดงในรูปที่ 7 ซึ่งอาจเกิดจากการดูดซับความชื้นในระหว่างการเก็บรักษาและการให้ความร้อนอย่างรวดเร็ว
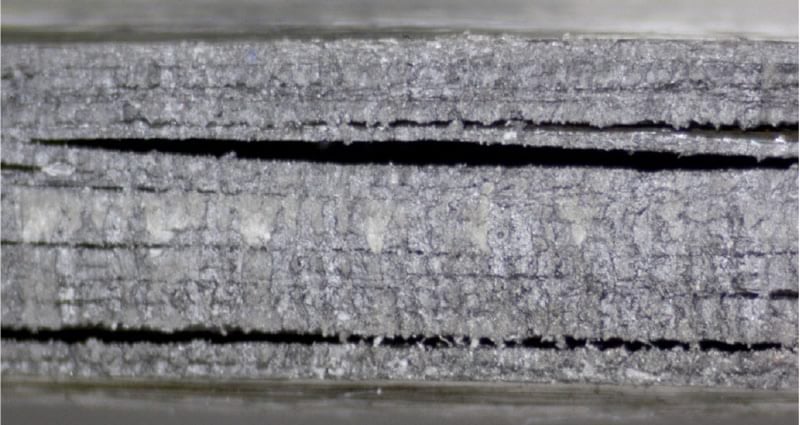
PPS
วัสดุ PPS ได้รับการทดสอบกับเครื่องทำความร้อนฮาโลเจนและทังสเตน 2000W การทดสอบฮาโลเจนดำเนินการแยก 55mm และการทดสอบทังสเตนที่ 55mm และ 95mm
ข้อมูลอีกครั้งแสดงให้เห็นว่าหลอดทังสเตนเป็นตัวทำความร้อนที่ดีกว่าสำหรับวัสดุนี้ (มากกว่าตัวทำความร้อนแบบฮาโลเจน) โดยมีการบันทึกอุณหภูมิที่สูงขึ้นในการแยก 55mm และยังมีความสม่ำเสมอของอุณหภูมิที่มากกว่าในตัวอย่าง มีการบันทึกการแปรผันของ 38 ° C สำหรับเครื่องทำความร้อนฮาโลเจนและ 30 ° C สำหรับเครื่องทำความร้อนทังสเตน การเปลี่ยนแปลงที่บันทึกไว้นี้จะได้รับอิทธิพลอย่างสูงจากตำแหน่งของเทอร์โมคัปเปิลที่สัมพันธ์กับหลอด ไม่รับประกันตำแหน่งเทอร์โมคัปเปิลเหมือนกัน
การทดสอบด้วย PPS จะสิ้นสุดลงในไม่ช้าหลังจากที่วัสดุถึงอุณหภูมิที่ต้องการ 425 ° C เนื่องจากมีการปล่อยควันของกำมะถันที่มีกลิ่นจากตัวอย่าง
ที่ระยะทาง 55mm อุณหภูมิเป้าหมายจะถูกบันทึกหลังจาก 66 และ 88 วินาทีสำหรับเครื่องทำฮาโลเจนและทังสเตนที่ 55mm ตามลำดับ เมื่อติดตั้งตัวทำความร้อนทังสเตนที่ 95mm จากตัวอย่างอุณหภูมิเป้าหมายไม่สำเร็จ
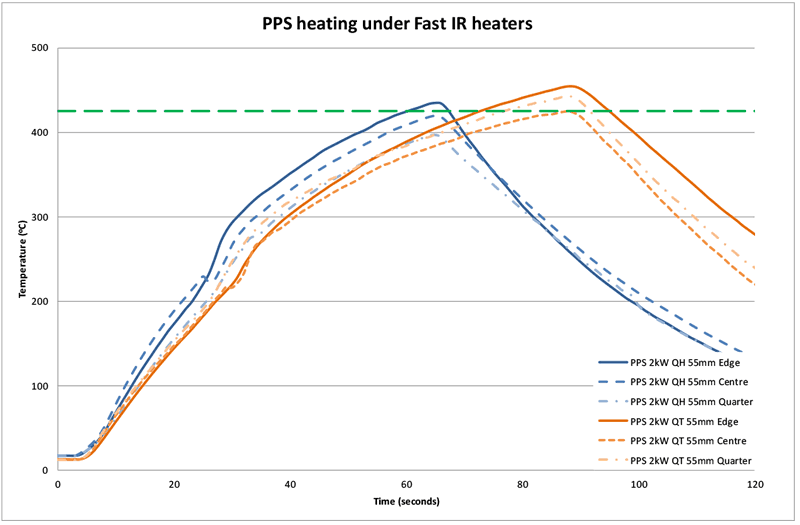
ฮอลโลว์สีดำ
ทำการทดสอบเบื้องต้นด้วยการแยกองค์ประกอบของวัสดุ 50mm อุณหภูมิที่เพิ่มขึ้นของวัสดุเป็นไปอย่างรวดเร็วมากสำหรับวัสดุทั้งหมด จากจุดเริ่มต้นที่เย็นองค์ประกอบกลวงจะใช้เวลาประมาณ 10-12 นาทีถึงความร้อนจนถึงระดับปฏิบัติการที่มั่นคง (อุณหภูมิพื้นผิวประมาณ 700 ° C) การเพิ่มขึ้นของอุณหภูมิของวัสดุนั้นใกล้เคียงกับเส้นโค้งการทำความร้อนของเครื่องทำความร้อนอย่างไรก็ตามมีความล่าช้าในเวลานี้
PEEK
พล็อตของเวลาที่ใช้ในการทำให้ตัวอย่าง PEEK ให้ความร้อนถึงอุณหภูมิการประมวลผลที่ต้องการแสดงอยู่ด้านล่างในรูปที่ 9 นี่แสดงให้เห็นว่าเวลาทำความร้อนถึง 425 ° C อยู่ที่ประมาณ 185 วินาทีจากเมื่อเปิดเครื่องทำความร้อนที่ 50mm หากระยะทางเพิ่มขึ้นเป็น 100mm เวลาจะเพิ่มขึ้นเป็น 230 วินาที ตัวอย่างถูกปล่อยทิ้งไว้ระหว่างแท่นวางทั้งสองในระหว่างการให้ความร้อนขึ้นและนำออกเพื่อทำความเย็น
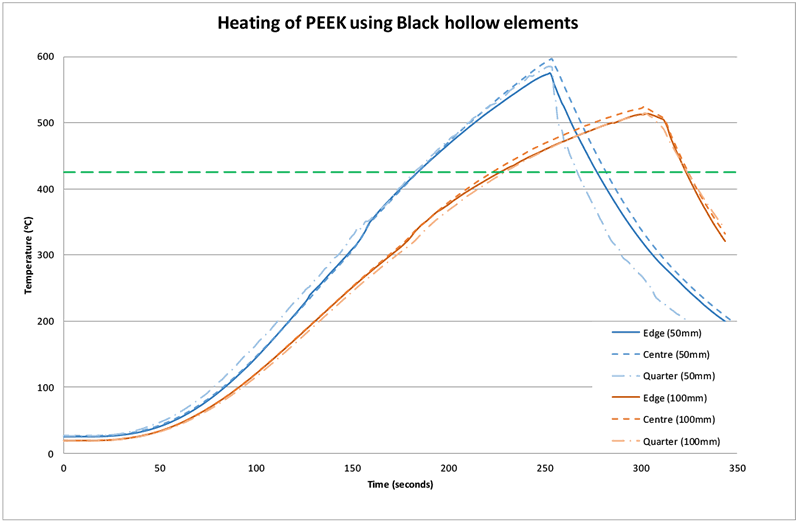
พีเคเค
เวลาที่ใช้สำหรับ PEKK ในการเข้าถึงเกณฑ์ขั้นต่ำนั้นนานกว่าเล็กน้อยสำหรับ PEEK มีสองเหตุผลที่เป็นไปได้สำหรับสิ่งนี้: 1.) วัสดุไม่ดูดซับรังสีอินฟราเรดเช่นเดียวกับ PEEK และ 2) ความหนาของวัสดุมีขนาดใหญ่เป็นสองเท่า (1 และ 2mm ตามลำดับ) เวลาที่ใช้ในการเข้าถึง 425 ° C ที่ 50mm คือ 181 วินาทีและที่ 100mm สิ่งนี้เพิ่มขึ้นเป็น 244 วินาที
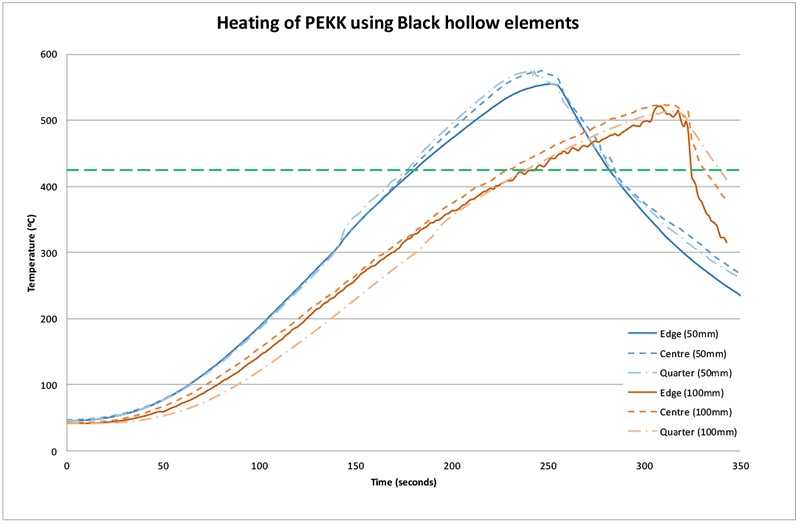
PPS
PPS ได้รับความร้อนอย่างมากกับองค์ประกอบกลวงสีดำที่มี 425 ° C ที่ถูกบันทึกใน 171 วินาทีและ 219 วินาทีที่ 50 และ 100mm ตามลำดับ กราฟแสดงความร้อนสำหรับวัสดุนี้แสดงในรูปที่ 11 อีกครั้งมีการปล่อยควันกลิ่นกำมะถัน แต่ปริมาณของสิ่งนี้ไม่มากเท่ากับเครื่องทำความร้อนฮาโลเจนตามรายละเอียดด้านบน นี่อาจเป็นส่วนหนึ่งเนื่องจากการขาดพัดลมที่ด้านหลังของแผ่นความร้อน
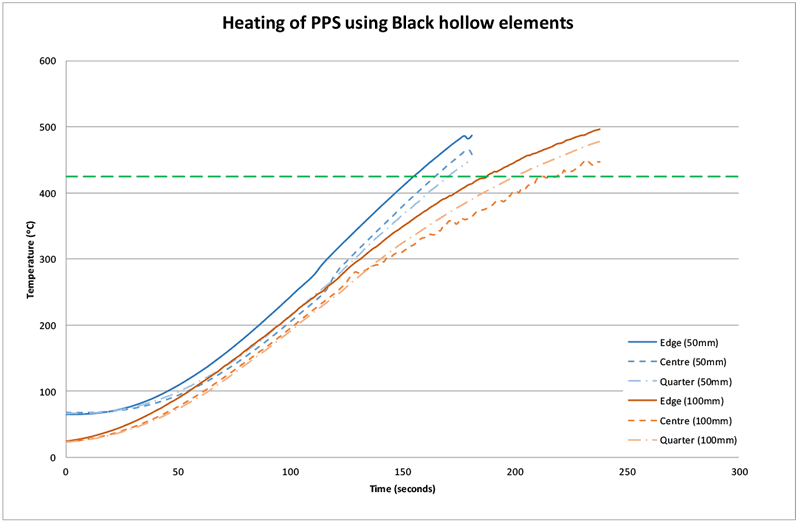
สรุปเวลาที่ต้องใช้ในการให้ความร้อนกับวัสดุโดยมีองค์ประกอบของฮาโลเจนทังสเตนและเซรามิกกลวงต่ออุณหภูมิเป้าหมายแสดงไว้ด้านล่างในตาราง 1 เนื่องจากการติดตั้งองค์ประกอบฮาโลเจนในระยะทางไกลกว่า 55mm ไม่ประสบความสำเร็จในระดับสากลผลลัพธ์เหล่านี้จึงถูกตัดออกจากตาราง
วัสดุ |
ประเภทเครื่องทำความร้อน (พลังงาน)
|
ระยะทาง | ได้เวลาไปถึง 425 ° C |
---|---|---|---|
PEEK | QHL (2kW) | 55mm | 99 |
QTL (2kW) | 55mm | 206 | |
FFEH (800W) | 50mm | 185 | |
FFEH (800W) | 100mm | 230 | |
พีเคเค | QTL (2kW) | 55mm | 102 |
FFEH (800W) | 50mm | 181 | |
FFEH (800W) | 100mm | 244 | |
PPS | QHL (2kW) | 55mm | 66 |
QTL (2kW) | 55mm | 88 | |
FFEH (800W) | 50mm | 171 | |
FFEH (800W) | 100mm | 219 |
การทดสอบแซนวิช
มีการทดสอบแซนด์วิชเพื่อรับข้อมูลเกี่ยวกับการถ่ายเทความร้อนผ่านวัสดุ สิ่งนี้ทำโดยให้ความร้อนตัวอย่างจากด้านเดียววัดอุณหภูมิทั้งสองด้านและเปรียบเทียบผลลัพธ์ หลอดทังสเตนและองค์ประกอบกลวงสีดำได้รับการตรวจสอบเท่านั้นตามผลลัพธ์ของ FastIR หลอดฮาโลเจนแบบคลื่นสั้นไม่เหมาะสมสำหรับวัสดุที่ต้องการ
ผลลัพธ์สำหรับองค์ประกอบ QTM แสดงให้เห็นว่าไม่มีความแตกต่างของอุณหภูมิอย่างมีนัยสำคัญระหว่างพื้นผิวด้านบนและด้านล่างสำหรับวัสดุ PEEK และ PPS อย่างไรก็ตาม PPS จะให้ความร้อนได้เร็วขึ้นและส่วนโค้งของวัสดุนี้จะแยกไม่ออก ต้องสังเกตว่าวัสดุทั้งสองนี้บางมาก (≈ 1mm) ตามที่คาดไว้ความแตกต่างของอุณหภูมิสำหรับ PEKK นั้นใหญ่กว่า (75 ± 2oC) เนื่องจากความหนา (≈ 2mm) ผลลัพธ์เหล่านี้แสดงในรูปที่ 12 ด้านล่าง
สำหรับเหตุผลในการปฏิบัติงานการทดสอบจะสิ้นสุดลงเมื่อตรวจพบอุณหภูมิของ 300 ° C โดยไพโรมิเตอร์ จุดสูงสุดที่พบใน 30 วินาทีแรกของการทดสอบคือการสะท้อนกลับและไม่ใช่การอ่านอุณหภูมิที่แท้จริง
ผลลัพธ์เหล่านี้แสดงให้เห็นว่าวัสดุ PEEK และ PPS สามารถแทรกซึม IR ได้ดีโดยการใช้ตัวทำความร้อนชนิดทังสเตน อย่างไรก็ตามการทำให้เท่าเทียมกันของอุณหภูมิสำหรับ PEKK นั้นไม่ดีแสดงให้เห็นถึงความแตกต่างของอุณหภูมิเกือบ 75 ° C ในช่วง 18 วินาทีสุดท้ายของการทดสอบ 4
มันเป็นไปไม่ได้ที่จะเคลื่อนย้ายตัวอย่างวัสดุที่อยู่ใกล้กับฮีทเตอร์เพื่อวิเคราะห์ว่าจะเกิดผลกระทบเช่นไรเนื่องจากมุมแหลมที่จำเป็นสำหรับ pyrometer เพื่อดูวัสดุนั้นจะบิดเบือนการอ่าน
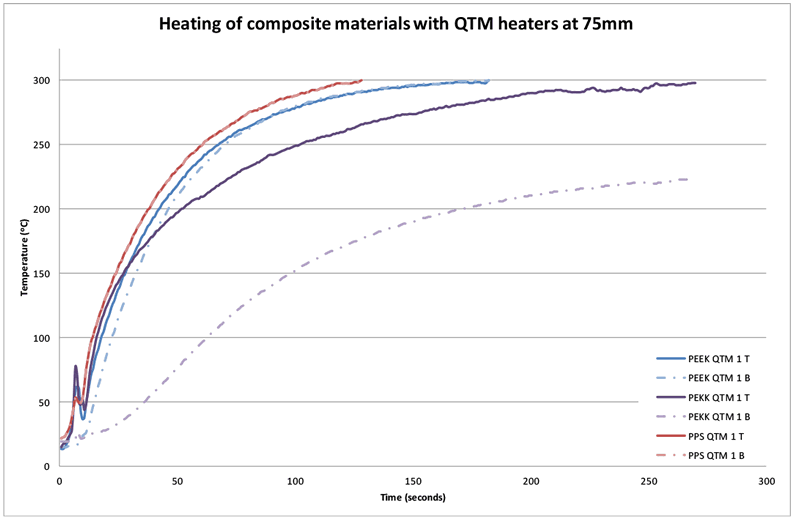
การให้ความร้อนของชิ้นงานที่มีองค์ประกอบกลวงสีดำในระยะทางเดียวกัน (75mm) แสดงแนวโน้มที่คล้ายกันโดยมีความแตกต่างของอุณหภูมิที่มากขึ้น (45 ± 2 ° C) สำหรับวัสดุ PEKK ที่หนากว่า (เปรียบเทียบกับวัสดุที่บางกว่า) อุณหภูมิของพื้นผิวด้านบนและด้านล่างของ PEEK นั้นแทบจะแยกไม่ออก อย่างไรก็ตามมีความแตกต่างในอุณหภูมิของ PPS (25 ± 2 ° C) ข้อมูลนี้จะแสดงในรูปที่ 13 นี่เป็นการบ่งชี้ว่าการบุก IR ของ PPS ที่มีความยาวคลื่นที่ยาวกว่านั้นไม่ดีเท่ากับ IR IR ที่สั้นกว่าอย่างไรก็ตามการปรับสมดุลอุณหภูมิของ PEKK นั้นดีกว่า (แต่ไม่เหมาะ)
ที่การแยก 75 มม. อุณหภูมิและอัตราความร้อนสูงสุดจะได้รับโดยใช้เครื่องทำความร้อนทังสเตนซึ่งดูเหมือนจะขัดแย้งกับผลลัพธ์ของลูกกลิ้งก่อนหน้า อย่างไรก็ตามไม่ควรใช้เป็นแนวทางเนื่องจากมีการใช้ฮีตเตอร์เดียวเท่านั้น ยิ่งไปกว่านั้นคุณสมบัติเหล่านี้จะได้รับการปรับปรุงให้ดีขึ้นโดยการใช้ตัวทำความร้อนที่ต่างจากฮีทเตอร์เดี่ยว
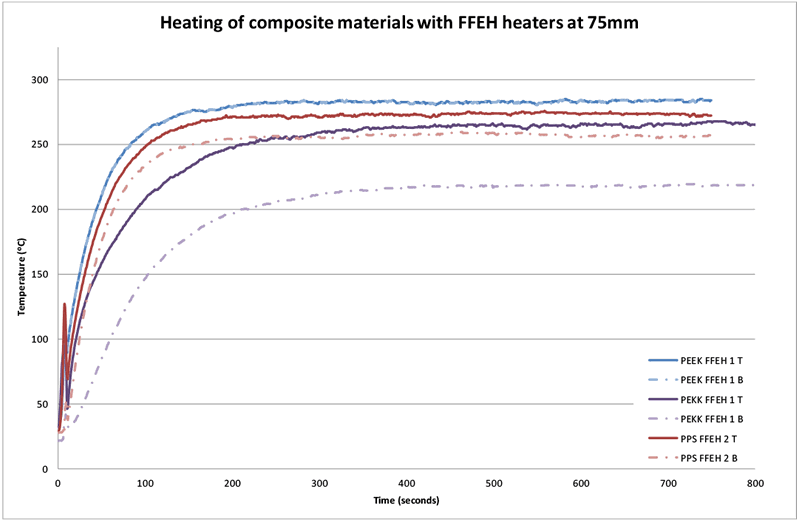
สรุป
- การทดสอบที่ดำเนินการและมีรายละเอียดข้างต้นบ่งชี้ว่าการให้ความร้อนของวัสดุเทอร์โมพลาสติกคาร์บอนทั้งสามไปจนถึงอย่างน้อย 425 ° C เป็นไปได้ทั้งองค์ประกอบฮาโลเจนคลื่นกลางและองค์ประกอบกลวงสีดำ
- อุณหภูมิสูงสุดที่สูงขึ้นสามารถทำได้โดยใช้ Ceramicx 800W องค์ประกอบกลวงสีดำ (FFEH)
- เวลาที่ต้องการให้ความร้อน PEEK ถึง 425 ° C คือ 206 วินาทีสำหรับ 2kW ตัวทำความร้อนหลอดทังสเตนที่ 55mm และ 230 วินาทีสำหรับองค์ประกอบ FFEH ที่ 100mm
- เวลาที่ใช้ในการให้ความร้อน PEKK ถึง 425 ° C คือ 102 วินาทีสำหรับ 2kW ตัวทำความร้อนหลอดทังสเตนที่ 55mm และ 244 วินาทีสำหรับองค์ประกอบ FFEH ที่ 100mm
- เวลาที่ใช้ในการให้ความร้อน PPS ถึง 425 ° C คือ 88 วินาทีสำหรับ 2kW ตัวทำความร้อนหลอดทังสเตนที่ 55mm และ 219 วินาทีสำหรับองค์ประกอบ FFEH ที่ 100mm
- อุณหภูมิสูงสุดอัตราการให้ความร้อนของวัสดุที่ทำได้และความสม่ำเสมอของอุณหภูมิพื้นผิวเป็นฟังก์ชั่นที่แข็งแกร่งของระยะทางที่เครื่องทำความร้อนติดตั้งจากวัสดุ
- การซึมผ่าน IR ที่ยอดเยี่ยมและการปรับสมดุลอุณหภูมิผ่านความหนาของวัสดุของ PPS และ PEEK สามารถทำได้โดยใช้ฮาโลเจนคลื่นกลาง (ทังสเตน) การทำให้เท่าเทียมกันของอุณหภูมิกับ PEKK นั้นไม่ดีเท่ากับวัสดุอื่น ๆ
- PEEK ที่ยอดเยี่ยมและความเสมอภาคของอุณหภูมินั้นสามารถมองเห็นได้ด้วย PEEK โดยใช้องค์ประกอบกลวงสีดำ คุณสมบัตินี้ไม่ดีเท่า PEKK และ PPS
จากข้อมูลการทดสอบข้างต้นและการแยกวัสดุปิดองค์ประกอบซึ่งจำเป็นต้องใช้เพื่อให้ได้อุณหภูมิที่ต้องการในการสร้างวัสดุที่เป็นปัญหาปรากฏว่าตัวปล่อยรังสีอินฟราเรดที่ดีที่สุดคือ Ceramicx 800W องค์ประกอบกลวงเต็มแบนสีดำ ในขณะที่เวลาเพื่อให้ได้อุณหภูมิที่ต้องการนั้นนานกว่าเครื่องทำความร้อนทังสเตนเล็กน้อยความใกล้ชิดขององค์ประกอบที่ใช้จะนำไปสู่ความสม่ำเสมอของอุณหภูมิพื้นผิวที่ดีขึ้น นอกจากนี้องค์ประกอบเซรามิกเริ่มต้นจากอุณหภูมิห้องและใช้เวลาประมาณ 12 นาทีเพื่อให้ถึงระดับปฏิบัติการ ดังนั้นเวลานี้อาจสั้นลงอย่างมีนัยสำคัญโดยการอุ่นองค์ประกอบ
ควรสังเกตว่าผลลัพธ์เหล่านี้เป็นไปตามตัวอย่างที่มีไว้สำหรับการทดสอบ (เช่นความหนา 1mm และ 2mm) ความร้อนของชิ้นส่วนที่หนาขึ้นอาจต้องมีการตรวจสอบการเปลี่ยนแปลงที่สำคัญของเทคโนโลยีการทำความร้อนเพื่อให้แน่ใจว่าโปรไฟล์อุณหภูมิทั่วทั้งความหนาของวัสดุมีความสม่ำเสมอและเหมาะสมสำหรับการขึ้นรูปตามมา
1 อีเทอร์คีโตน Polyether
2 โพลีฟีนลีนซัลไฟด์
3 Polyetherketoneketone
4 ความแตกต่างระหว่างพื้นผิวด้านบนและด้านล่างโดยเฉลี่ยในช่วง 18 วินาทีสุดท้ายของการทดสอบ
ข้อจำกัดความรับผิดชอบ
ผลการทดสอบเหล่านี้ควรได้รับการพิจารณาอย่างรอบคอบก่อนที่จะใช้ตัวปล่อยรังสีอินฟราเรดบางประเภท
การทดสอบซ้ำที่ดำเนินการโดย บริษัท อื่นอาจไม่ได้ผลเช่นเดียวกัน ความแตกต่างในเงื่อนไขการทดลองอาจเปลี่ยนแปลงผลลัพธ์ แหล่งที่มาของข้อผิดพลาดอื่น ๆ ได้แก่ : แบรนด์ของตัวปล่อยที่ใช้, ประสิทธิภาพของตัวปล่อย, กำลังไฟฟ้าที่ให้, ระยะทางจากวัสดุที่ทดสอบไปยังตัวปล่อยที่ใช้และสภาพแวดล้อม ตำแหน่งที่วัดอุณหภูมิอาจทำให้เกิดการเปลี่ยนแปลงในผลลัพธ์