YAZAR | TARİH OLUŞTURULDU | VERSION | BELGE NUMARASI |
---|---|---|---|
Peter Marshall | 8 Nisan 2016 | V1.1 | CC11 - 00101 |
Giriş
CCP Gransden, şekillendirme işlemleri için termoplastik karbon fiber prepreg malzemelerini ısıtmak üzere bir kızılötesi fırın inşa etmek için Ceramicx'e başvurdu. Bu test çalışması, satış teklifinde (CSP 000 008) tanımlanan işlevlerin bir parçası olarak gerçekleştirildi. Birinci aşama, öngörülen minimum malzeme sıcaklığı 425 ° C olan bu proje için kızılötesi ısıtıcı değerlendirmesini ve seçimini içerir.
Malzeme Açıklaması
230 x 230 x 1mm parçalarında iki malzemeden üç örnek alınmıştır. Bu durumlarda, matris PEEK idi.1 ve PPS2. Daha küçük bir PEKK örneği3 200 x 150 x 2mm boyutlarında da alındı. Materyal sert, parlak siyah bir yüzeyle pürüzsüzdü. PEEK ve PPS numunelerinin yüzeyindeki yüzeyde küçük bir desen görüldü.
PEEK ve PPS örnekleri, 115 x 115 mm'lik parçalar halinde kesildi. PEKK malzemesi 100 x 75mm parçalara kesildi.
Yöntem
İki farklı ısıtıcı aile değerlendirildi; halojen (QH ve QT) ve siyah içi boş seramik (FFEH). Her durumda, merdaneler, malzemenin üstüne ve altına ayarlanabilir yükseklikte monte edildi.
FastIR
Ceramicx'in FastIR 500 ünitelerinden ikisinin, malzemenin üzerine ve altına monte edilmesini sağlamak için bir montaj sistemi üretildi. Bir FastIR 500, bir 500 x 500 mm muhafazasına paralel şekilde monte edilmiş yedi ısıtma elemanından oluşur. Bu tüpler arasındaki boşluk 81mm'dir. 1500W ve 2000W 'long' (toplam uzunluk: 473mm) elemanları, sırasıyla iki ünite 21 veya 28kW'den toplam çıktı veren elemanlar kullanıldı. Isıtıcı üniteleri, eleman yüzeyi ile numune arasındaki mesafenin 55mm ve 95mm arasında değişeceği şekilde monte edildi.
Kullanılan deney protokolü aşağıdaki gibidir:
- Fanlar açık
- Merkezi üç ısıtma elemanı açık, üst ve alt
- Dıştaki dört ısıtma elemanı açık, üst ve alt
İki FastIR birimi arasındaki örneğin görüntüsü Şekil 1'te gösterilmektedir. İki ısıtma ünitesi arasındaki boşluğu kapatacak hiçbir şey kullanılmadı.
Elements
FastIR ünitesine iki tip eleman monte edilebilir; kuvars halojen ve kuvars tungsten. Bu elemanlar farklı tepe kızılötesi dalga boyları yayar; yaklaşık 1.0 - 1.2μm'de halojen ve 1.6 - 1.9μm arasında tungsten. Her tüpün çapı 10mm, toplam uzunluğu 473mm ve ısıtılmış 415mm'dir.
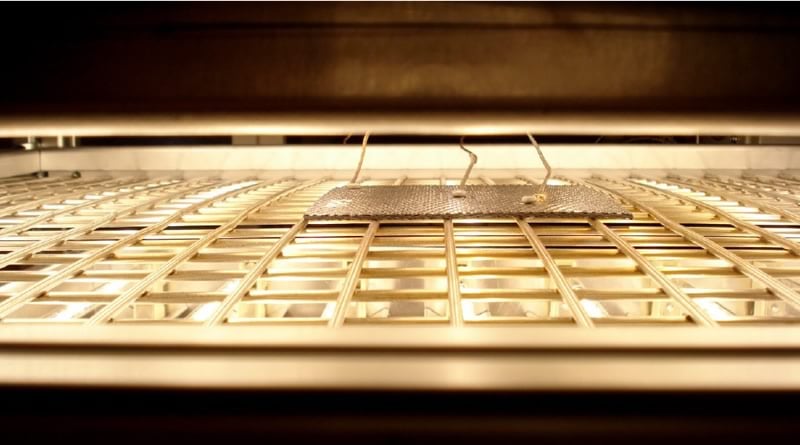
Siyah içi boş
Her bir plaka 2kW güç veren, XXUMX x 7 matrixx'in 800W FFEH elemanlarının bir 11.2 x 510 matrisini içerecek şekilde özel bir ısıtma plakası tasarlanmıştır. Bu matris, bir 510 x 65mm kasa içine alınmış ve yukarıda detaylandırılan FastIR sistemi ile aynı çerçeveye monte edilmiştir. Deney protokolü kullanıldı; ancak, bu plakalarda fanlar kullanılmamıştır. Bu elemanlar arasındaki mesafe XNUMXmm idi.
İki farklı eleman-örnek mesafesi, 50 ve 100mm kullanıldı. Yine, iki ısıtma ünitesi arasındaki boşluk açık bırakıldı
Elements
Ceramicx siyah içi boş elemanlar orta ila uzun rejimlerde (2 - 10μm) en yüksek dalga boylarını yayar. Her elemanın boyutları 245 x 60mm (lxw) 'dir. Seramik elemanlarla ilişkili daha uzun dalga boyları birçok polimerik maddenin ısıtılması için çok verimlidir.
Aletler
K tipi termokupllar M3 vidaları kullanılarak numunenin yüzeyine yapıştırılmıştır. Seramik çimento denendi, ancak bu, malzemenin yüzeyine yapışmadı. Gereken yüksek sıcaklıklar göz önüne alındığında, mevcut hiçbir yapıştırıcı sabit kalmayacaktı, bu nedenle mekanik fiksasyon gerekli görüldü. Termokupllar, her bir numunenin ortasına ve ayrıca Şekil 10'te gösterildiği gibi kenardan 30mm (kenar) ve 2mm (çeyrek) yerleştirildi. Bu, termokuplları doğrudan tüp elemanlarının üzerine ve elemanların arasındaki merkeze yerleştirerek maksimum sıcaklık farkının kaydedilmesini sağlar. Sıcaklık verileri, tek saniye aralıklarla kaydedildi.
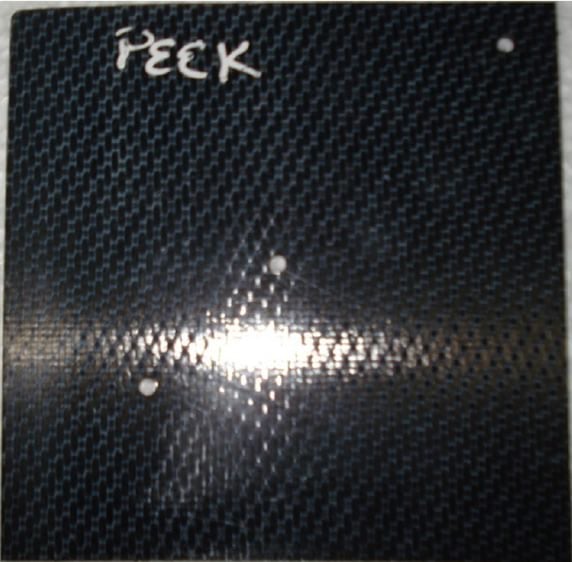
Sandviç testi
Sandviç test cihazı, Şekil 2'te gösterildiği gibi gelişmiş bir malzeme termal tepki test makinesidir. Dikey olarak yukarı ve aşağı bakacak şekilde, çeşitli konumlarda kızılötesi ısıtıcılar iki konuma monte edilebilir. Bu, test edilen malzemenin üstten ve / veya alttan ısıtılabilmesini sağlar. Test edilen malzemenin üst ve alt yüzey sıcaklığını belirlemek için temassız dört optik pirometre kullanılır. Yayıcıların çalışma sıcaklıklarına kadar ısınmasına izin verilir ve daha sonra malzeme önceden belirlenmiş bir süre için yayıcıların altına alınır. Bu test, hangi ısıtıcının malzemeden en iyi nüfuzu verdiğini belirlemek için numunenin üzerine hem 1kW tungsten (QTM) hem de 800W siyah içi boş elemanlar (FFEH) ile 75mm üzerine monte edildi.
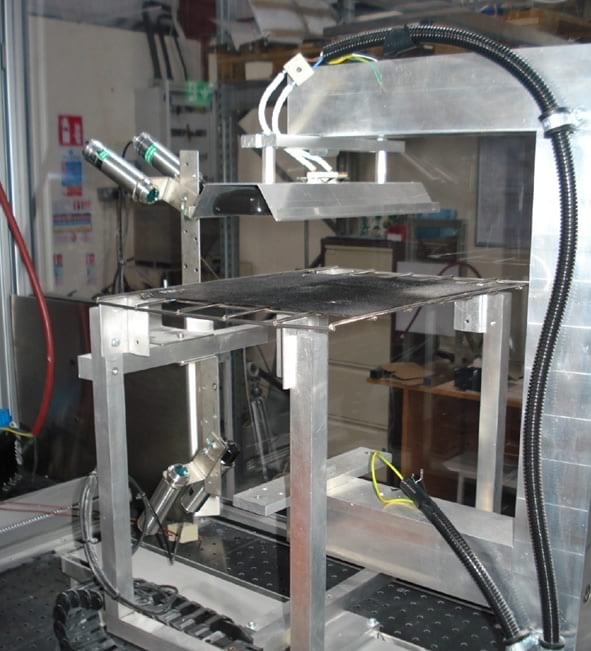
Sonuçlar
FastIR
Bu bölüm, söz konusu üç malzeme için tungsten ve halojen tüpler için bulunan sonuçları bildirir. Testler üç farklı ısıtıcı yüksekliğinde (55mm, 80mm ve 95mm) yapılmıştır.
DİKİZLEMEK
İlk denemeler bir PEEK numunesi ve 1500mm ile ayrılan 110W kuvars halojen tüplü iki FastIR ısıtıcı ile gerçekleştirildi. Şekil 4'te gösterilen bu testin sonuçları, numunenin istenen sıcaklığa ulaşamadığını gösterir.
Elemanlar, aynı ayırımda numunenin bir lokasyonda istenen sıcaklığa ulaştığını ve aştığını gösteren 2000W kısa dalga halojen (QHL) tüplerine değiştirildi. Bu durumda, kaydedilen maksimum sıcaklık 485 ° C idi, ancak önemli sıcaklık farklılıkları (83 ° C'ye kadar) da tespit edildi. 425 ° C hedef sıcaklığına ulaşmak için gereken süre 99 saniye idi. Bu sadece iki noktada sağlandı
Quartz tungsten (QTL) tüpleri (2000W), ısıtıcı mesafesi arttıkça maksimum sıcaklık düşerek üç seviyede incelenmiştir. 55mm'de maksimum ve minimum 520 ° C sıcaklık tespit edildi. Malzeme numunesi boyunca hedef sıcaklık, 206 saniye içinde elde edildi. 80mm'ye olan mesafeyi artırarak, bunlar 450 ° C ve 415 ° C'ye düşürülmüş ve numunenin üstünde 95mm'de, numunenin maksimum ve minimum sıcaklıkları 407 ve 393 ° C'dir.
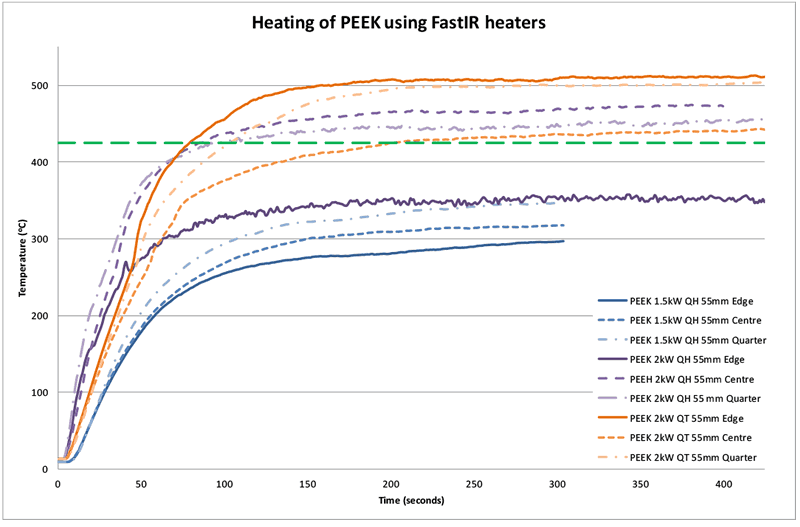
Şekil 4, ısıtıcıların numuneye yakın olmasından dolayı numunede meydana gelebilecek sıcaklık değişiminin yanı sıra malzemeyi 425 ° C'ye (206kW QT ısıtıcı için 2 saniye) ısıtmak için gereken zamana bağlı olarak ortaya çıkan sıcaklık farkını göstermektedir.
150 ° W tungsten tüpleri, kullanılan öğelerin gücünü azaltmak yerine ısıtıcı mesafesini arttırmak için daha operasyonel olarak önemli olduğu için test edilmedi.
Şekil 5, ısıtma öncesi ve sonrası numunedeki görsel farkı göstermektedir.
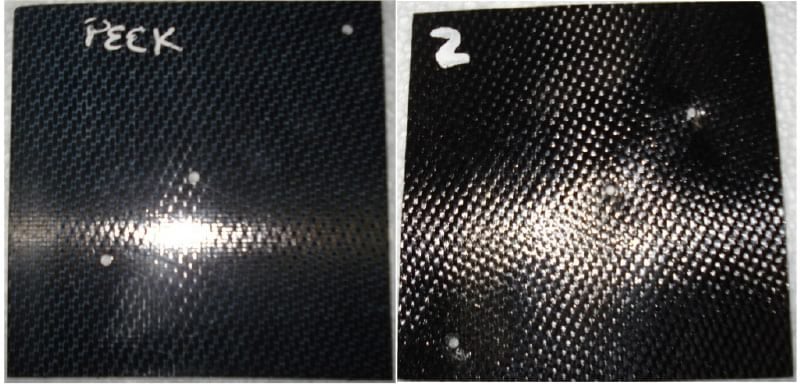
PEKK
PEKK, yalnızca 2000mm'de 55W tungsten ısıtıcılarla ısıtıldı. Malzemenin ısıl tepkisi, 500 ° C'nin üzerindeki sıcaklıklar kaydedilirken mükemmeldi. Belirtilen minimum sıcaklık, 102 ° C'nin üzerinde olan, kaydedilen maksimum sıcaklık 500 saniyede elde edildi.
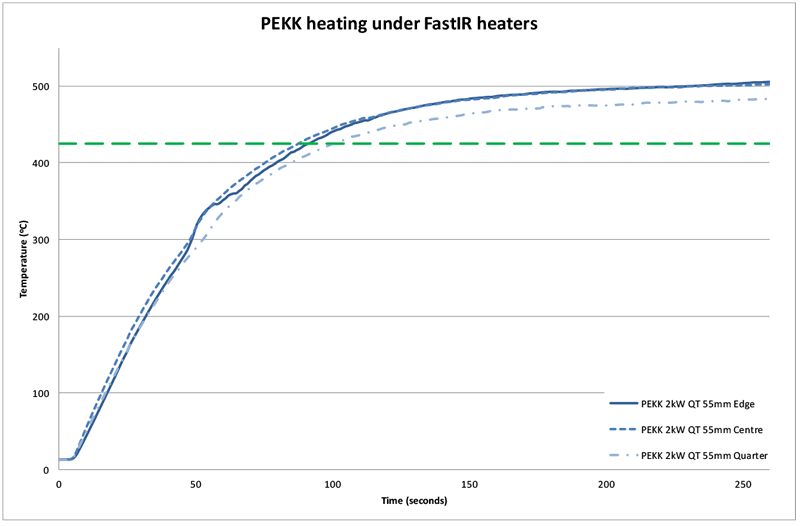
Bu numunenin, kenarlarda bir miktar yarılma ve delaminasyon gösterdiği ve ayrıca Şekil 7'te gösterildiği gibi ısıtmanın ardından muhtemelen depolama sırasında nem emiliminden ve meydana gelen hızlı ısıtmadan kaynaklanan bazı yüzey bozulmaları gösterdiği görülmüştür.
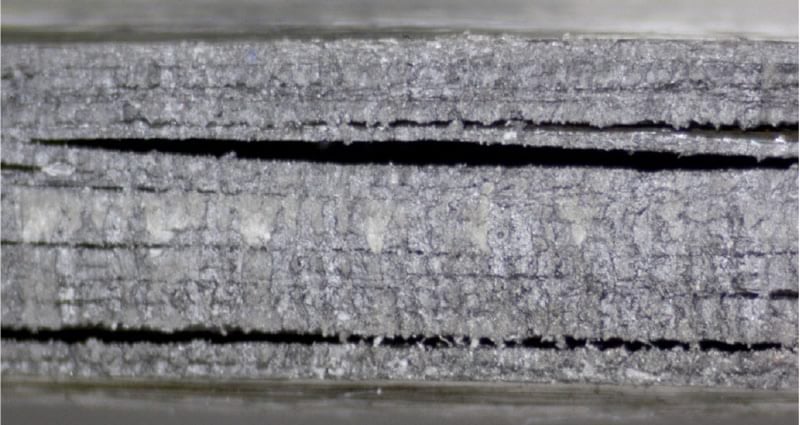
PPS
PPS malzemesi, 2000W halojen ve tungsten ısıtıcılarla test edildi. Halojen testi, bir 55mm ve 55mm ve 95mm'de tungsten testlerinin ayrılmasıyla gerçekleştirildi.
Yine veriler tungsten tüpünün bu malzeme için daha iyi bir ısıtıcı olduğunu gösterdi (halojen ısıtıcıdan daha fazla). Halojen ısıtıcılar için bir 55 ° C ve tungsten ısıtıcılar için 38 ° C bir değişiklik kaydedildi. Bu kaydedilen varyasyon, termokuplun tüplere göre konumundan büyük ölçüde etkilenecektir. Aynı termokupl konumları garanti edilmez.
PPS ile yapılan testler, malzemeden istenen 425 ° C sıcaklığına ulaşılmasından hemen sonra sonlandırıldı, çünkü numunelerden kükürt kokulu duman çıktı.
55mm mesafesinde, hedef sıcaklık, 66mm'de sırasıyla halojen ve tungsten ısıtıcılar için 88 ve 55 saniye sonra kaydedildi. Tungsten ısıtıcıları numuneden 95mm'ye monte edildiğinde, hedef sıcaklık elde edilememiştir.
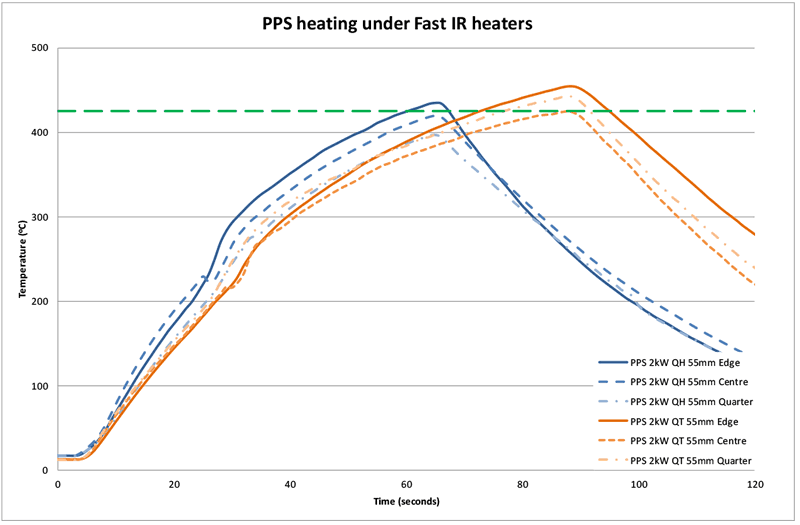
Siyah içi boş
İlk testler, 50mm'nin element materyali ayrılmasıyla yapıldı. Malzemenin sıcaklık artışı tüm malzemeler için çok hızlıydı. Soğuk bir başlangıçtan itibaren, içi boş elemanların sabit çalışma seviyelerine (yaklaşık 10 ° C yüzey sıcaklığı) ısıtılması yaklaşık 12-700 dakika sürer. Malzeme sıcaklığı artışı, ısıtıcının ısıtma eğrisine geniş ölçüde benziyordu, ancak bunun içinde bir zaman gecikmesi vardı.
DİKİZLEMEK
İstenen işlem sıcaklığına ulaşmak için PEEK örneğini ısıtmak için geçen zamanın bir grafiği, aşağıda Şekil 9'te gösterilmektedir. Bu, 425 ° C'ye kadar olan ısıtma süresinin, ısıtıcılar 185mm'de açıldığında yaklaşık 50 saniye olduğunu gösterir. Mesafe 100 mm'ye yükseltilirse, süre 230 saniyeye çıkar. Örnek, ısınma sırasında iki plaka arasında bırakılmış ve soğutma için ayrılmıştır.
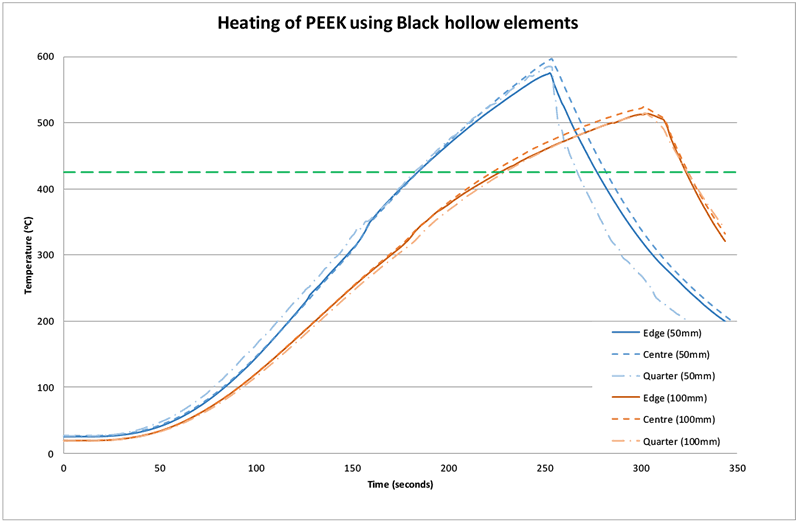
PEKK
PEKK'nın asgari eşiğe ulaşması için geçen süre PEEK'ten biraz daha uzundu. Bunun için iki olası neden vardır: 1.) Materyal kızılötesi radyasyonu ve PEEK ve 2'i emmez.) Malzemenin kalınlığı iki kat daha büyüktür (sırasıyla 1 ve 2mm). 425mm'de 50 ° C'ye ulaşmak için gereken süre 181 saniye idi ve 100mm'de bu 244 saniyeye yükseldi
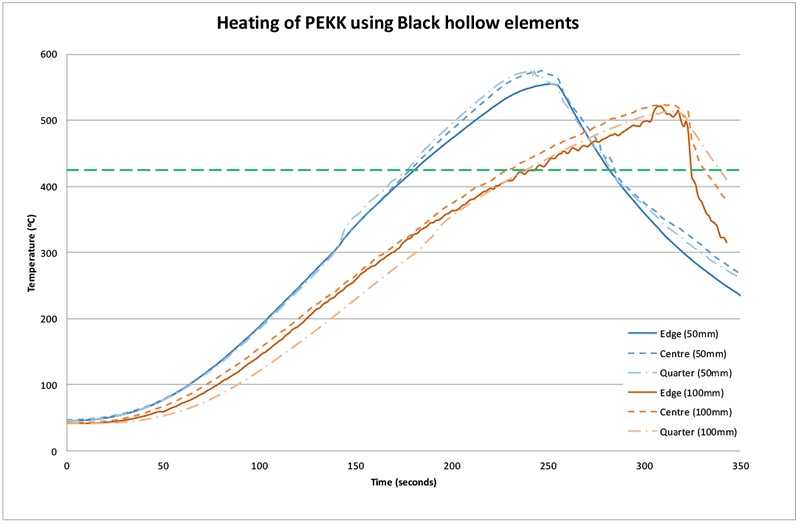
PPS
PPS, sırasıyla 425 ° C ve 171 mm'de 219 saniye ve 50 saniye olarak kaydedilmiş 100 ° C olan siyah içi boş elemanlarla çok başarılı bir şekilde ısıtılmıştır. Bu malzeme için ısıtma eğrisi, Şekil 11'te gösterilmiştir. Yine, bir kükürt kokulu duman salınımı meydana geldi, ancak bunun miktarı yukarıda açıklandığı gibi halojen ısıtıcılar kadar değildi. Bu, kısmen ısıtma plakasının arkasındaki fanların bulunmamasından kaynaklanabilir.
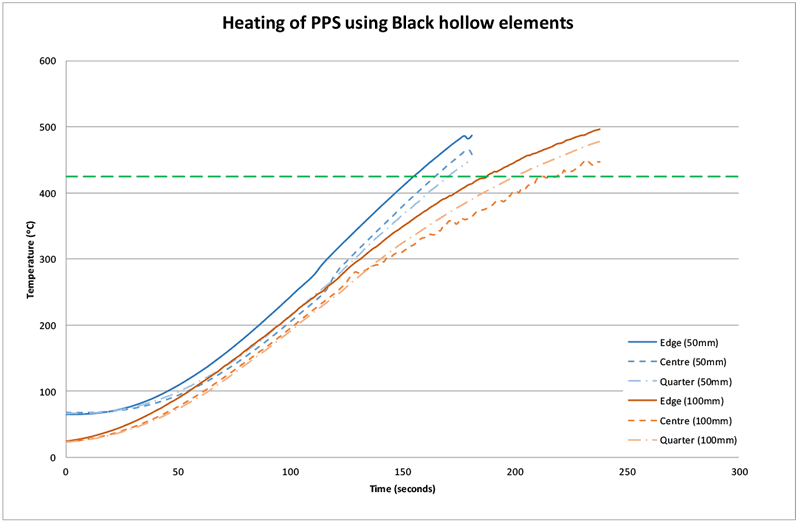
Halojen, tungsten ve içi boş seramik elemanlarla malzemelerin hedef sıcaklığa ısıtılması için gereken zamanların bir özeti, Tablo 1'te gösterilmektedir. Halojen elementleri 55mm'den daha uzun mesafelere monte etmek evrensel olarak başarılı olmadığından, bu sonuçlar tablodan çıkarılmıştır.
Malzeme |
Isıtıcı tipi (güç)
|
Mesafe | 425 ° C'ye ulaşma zamanı |
---|---|---|---|
DİKİZLEMEK | QHL (2kW) | 55mm | 99 |
QTL (2kW) | 55mm | 206 | |
FFEH (800W) | 50mm | 185 | |
FFEH (800W) | 100mm | 230 | |
PEKK | QTL (2kW) | 55mm | 102 |
FFEH (800W) | 50mm | 181 | |
FFEH (800W) | 100mm | 244 | |
PPS | QHL (2kW) | 55mm | 66 |
QTL (2kW) | 55mm | 88 | |
FFEH (800W) | 50mm | 171 | |
FFEH (800W) | 100mm | 219 |
Sandviç testi
Malzemenin içinden ısı aktarımı hakkında bilgi edinmek için sandviç testi yapıldı. Bu, numuneyi tek taraftan ısıtmak, iki taraftaki sıcaklığı ölçmek ve sonuçları karşılaştırmak suretiyle yapıldı. Sadece Tungsten tüpler ve siyah içi boş elemanlar incelendi, FastIR sonuçlarına göre, kısa dalga halojen tüpleri söz konusu malzemeler için uygun ısıtıcılar değil.
QTM elementlerinin sonuçları, PEEK ve PPS materyalleri için üst ve alt yüzey arasında önemli bir sıcaklık farkı olmadığını gösterir, ancak PPS daha hızlı bir şekilde ısınır ve bu materyal için eğriler neredeyse ayırt edilemez. Bu iki malzemenin çok ince olduğu belirtilmelidir (≈ 1mm). Beklendiği gibi, PEKK için sıcaklık farkı kalınlığı (≈ 75mm) nedeniyle daha büyüktü (2 ± 2oC). Bu sonuçlar aşağıdaki Şekil 12'te gösterilmektedir.
Operasyonel nedenlerden dolayı, pirometreler tarafından bir 300 ° C sıcaklık tespit edildiğinde test sonlandırılır. Testin ilk 30 saniyesinde görülen tepe yansımadır ve gerçek bir sıcaklık okuması değildir.
Bu sonuçlar, tungsten tipi ısıtıcı kullanarak PEEK ve PPS için malzemenin iyi IR penetrasyonunun mümkün olduğunu göstermektedir. Bununla birlikte, PEKK için sıcaklık dengelemesi o kadar iyi değildir, test75'in son 18 saniyesinde sıcaklıktaki neredeyse 4 ° C farkıyla gösterilmiştir.
Pirometrenin malzemenin okumayı bozacağını görmesi için gereken akut açının ne gibi bir etkisinin olabileceğini analiz etmek için malzeme numunelerini ısıtıcıya yaklaştırmak mümkün değildi.
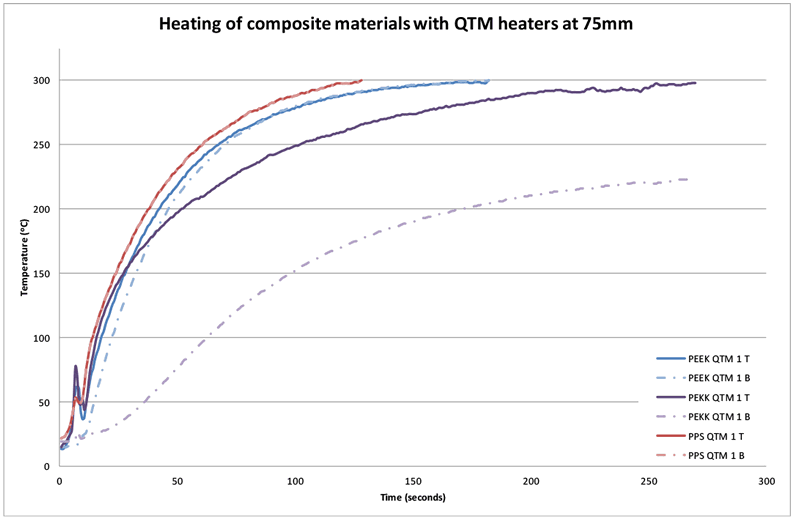
Numunelerin siyah içi boş elemanlarla aynı mesafede (75mm) ısıtılması, daha kalın PEKK malzemesi için (daha ince malzemelere kıyasla) gözlemlenen daha büyük bir sıcaklık farkına (45 ± 2 ° C) benzer bir eğilim gösterir. PEEK'in üst ve alt yüzeylerinin sıcaklıkları neredeyse ayırt edilemez; bununla birlikte, PPS (25 ± 2 ° C) sıcaklığında bir fark vardır. Bu veri Şekil 13'te gösterilmiştir. Bu, PPS'nin daha uzun dalga boyu radyasyonuna sahip IR penetrasyonunun, kısa tungsten IR'deki kadar iyi olmadığını, ancak PEKK'nin sıcaklık dengelemesinin daha iyi olduğunu (ancak ideal olmadığını) gösterir.
75mm ayrılmasında, en yüksek sıcaklıklar ve ısıtma oranları, önceki merdane sonuçlarına aykırı gibi görünen tungsten ısıtıcı kullanılarak elde edilir. Bununla birlikte, yalnızca tek bir ısıtıcı kullanıldığı için bu kılavuz olarak kullanılmamalıdır. Ayrıca, bu özellikler, tek bir ısıtıcının aksine bir dizi ısıtıcı kullanılarak geliştirilecektir.
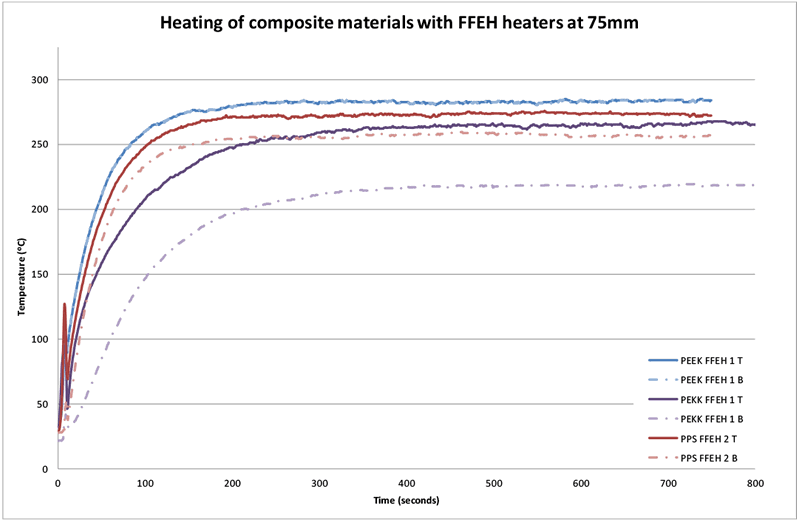
Sonuç
- Yukarıda yapılan ve ayrıntılı olarak açıklanan testler, üç termoplastik karbon kompozit malzemenin minimum 425 ° C'ye ısıtılmasının hem orta dalga halojen hem de siyah oyuk elemanlarla mümkün olduğunu göstermektedir.
- Ceramicx 800W siyah içi boş eleman (FFEH) kullanılarak daha yüksek maksimum sıcaklıklar elde edilebilir.
- PEEK'i 425 ° C'ye ısıtmak için gereken süre, 206mm'deki 2kW tungsten tüp ısıtıcıları için 55 saniye ve 230mm'deki FFEH elemanları için 100 saniyedir.
- PEKK'yi 425 ° C'ye ısıtmak için gereken süre, 102mm'deki 2kW tungsten tüp ısıtıcıları için 55 saniye ve 244mm'deki FFEH elemanları için 100 saniyedir.
- PPS'yi 425 ° C'ye ısıtmak için gereken süre, 88mm'deki 2kW tungsten tüp ısıtıcıları için 55 saniye ve 219mm'deki FFEH elemanları için 100 saniyedir.
- Maksimum sıcaklıklar, elde edilebilecek malzeme ısıtma oranları ve yüzey sıcaklığı homojenliği, ısıtıcıların malzemeden monte edildiği mesafenin güçlü bir fonksiyonudur.
- Mükemmel IR penetrasyonu ve dolayısıyla PPS ve PEEK'in malzeme kalınlığı boyunca sıcaklık eşitlemesi orta dalga halojen (tungsten) ile sağlandı. PEKK ile elde edilen sıcaklık eşitlemesi diğer malzemeler ile olduğu kadar iyi değildi.
- PEEK ile siyah içi boş elemanlar kullanılarak mükemmel IR penetrasyonu ve sıcaklık eşitlemesi görülmüştür. Bu özellik PEKK ve PPS kadar iyi değildi.
Yukarıdaki test verilerine ve söz konusu malzemeleri oluşturmak için talep edilen sıcaklıkları elde etmek için gereken yakın eleman-malzeme ayrımlarına dayanarak, en iyi kızılötesi yayıcı Seramikx 800W siyah tam düz oyuk elemandır. İstenen sıcaklıklara ulaşma süreleri, tungsten ısıtıcılardan biraz daha uzun olsa da, kullanılan elementlerin yakınlığı daha iyi yüzey sıcaklığı homojenliği sağlayacaktır. Ayrıca, seramik elemanlar oda sıcaklığından başlatıldı ve operasyonel seviyelere ulaşmak için yaklaşık 12 dakika gerekliydi. Bu nedenle, bu süre, elemanların ön ısıtılmasıyla önemli ölçüde kısaltılabilir.
Ayrıca, bu sonuçların test için uygun olan numunelere dayandığına da dikkat edilmelidir (ör., 1mm ve 2mm kalınlığında). Daha kalın parçaların ısıtılması, malzemenin kalınlığı boyunca sıcaklık profilinin düzgün ve sonraki biçimlendirme işlemleri için uygun olmasını sağlamak için araştırılmasında ısıtma teknolojisinde önemli değişiklikler gerektirebilir.
1 Polieter eter keton
2 Polifenilen Sülfür
3 Polyetherketoneketone
4 Testin son 18 saniyesinde alınan üst ve alt yüzeyler arasındaki ortalama fark.
Feragatname
Belirli bir tür kızılötesi verici kullanmaya karar verilmeden önce bu test sonuçları dikkatlice düşünülmelidir.
Diğer şirketler tarafından yapılan tekrar testleri aynı bulguları elde edemeyebilir. Deney koşullarındaki farklılıklar sonuçları değiştirebilir. Diğer hata kaynakları şunları içerir: kullanılan vericinin markası, vericinin etkinliği, sağlanan güç, test edilen malzemeden kullanılan vericiye olan mesafe ve çevre. Sıcaklığın ölçüldüğü yerler de sonuçlarda farklılığa neden olabilir.