TÁC GIẢ | NGÀY TẠO | PHIÊN BẢN | SỐ VĂN BẢN |
---|---|---|---|
Bác sĩ Peter Marshall | 8 Tháng tư, 2016 | V1.1 | CC11 - 00101 |
Giới thiệu
CCP Gransden đã tiếp cận Ceramicx để xây dựng một lò hồng ngoại để làm nóng các vật liệu chế tạo sợi carbon nhiệt dẻo cho các hoạt động tạo hình của chúng. Công việc kiểm tra này được thực hiện như một phần của các chức năng được xác định trong đề xuất bán hàng (CSP 000 008). Giai đoạn một bao gồm đánh giá và lựa chọn lò sưởi hồng ngoại cho dự án này, với nhiệt độ vật liệu tối thiểu được quy định là 425 ° C.
Mô tả vật liệu
Ba mẫu của hai vật liệu đã được nhận trong các mảnh 230 x 230 x 1mm. Trong những trường hợp này, ma trận là PEEK1 và PPS2. Một mẫu PEKK nhỏ hơn3 với kích thước 200 x 150 x 2 mm cũng được nhận. Chất liệu cứng, mịn với màu đen bóng. Một mô hình nhỏ có thể nhìn thấy trên bề mặt trên bề mặt của mẫu PEEK và PPS.
Các mẫu PEEK và PPS đã được cắt thành các mảnh 115 x 115 mm. Vật liệu PEKK được cắt thành các mảnh 100 x 75mm.
Phương pháp
Hai gia đình nóng khác biệt được đánh giá; halogen (QH và QT) và gốm rỗng đen (FFEH). Trong mỗi trường hợp, trục cuốn được gắn phía trên và bên dưới mẫu vật liệu với chiều cao có thể điều chỉnh.
FastIR
Một hệ thống lắp được sản xuất để cho phép hai trong số các đơn vị FastIR 500 của Ceramicx được gắn bên trên và bên dưới vật liệu. FastIR 500 bao gồm bảy bộ phận làm nóng được gắn song song trong trường hợp 500 x 500 mm. Khoảng cách giữa các ống này là 81mm. Các phần tử 1500W và 2000W 'dài' (tổng chiều dài: 473mm) đã được sử dụng cho tổng sản lượng từ hai đơn vị tương ứng là 21 hoặc 28kW. Các bộ gia nhiệt được gắn sao cho khoảng cách giữa bề mặt phần tử và mẫu được thay đổi trong khoảng từ 55mm đến 95mm.
Giao thức thử nghiệm được sử dụng như sau:
- Quạt bật
- Ba yếu tố sưởi ấm trung tâm bật, trên rồi dưới
- Bên ngoài bốn yếu tố làm nóng được bật, trên rồi dưới
Hình ảnh của một mẫu giữa hai đơn vị FastIR được hiển thị trong Hình 1. Không có gì được sử dụng để thu hẹp khoảng cách giữa hai đơn vị sưởi ấm
Các yếu tố
Hai loại phần tử có thể được gắn trong đơn vị FastIR; thạch anh halogen và thạch anh vonfram. Các phần tử này phát ra các bước sóng hồng ngoại cực đại khác nhau; halogen ở khoảng 1.0 - 1.2μm và vonfram trong khoảng 1.6 - 1.9μm. Mỗi ống có đường kính 10 mm, tổng chiều dài 473mm và chiều dài được làm nóng là 415mm.
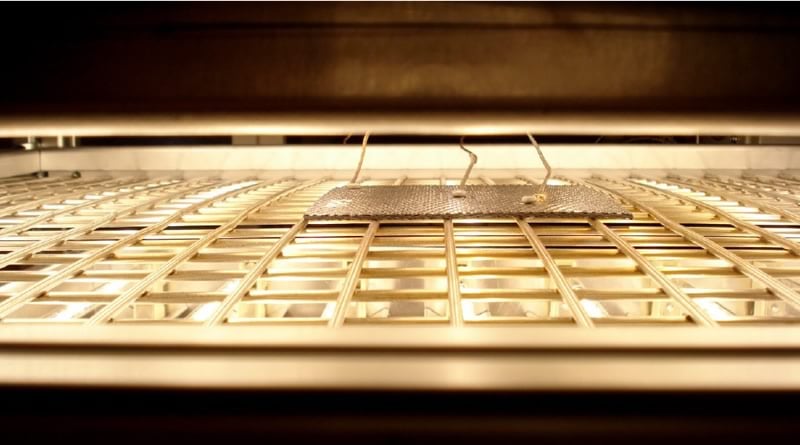
Rỗng đen
Một trục gia nhiệt tùy chỉnh được thiết kế để kết hợp ma trận 2 x 7 các yếu tố FFEH 800W của Ceramicx, cung cấp cho mỗi trục lăn 11.2kW công suất. Ma trận này được đặt trong vỏ 510 x 510mm và được gắn trong cùng khung với hệ thống FastIR chi tiết ở trên. Giao thức thử nghiệm đã được sử dụng; tuy nhiên, người hâm mộ đã không được tuyển dụng trong các máy đo này. Khoảng cách giữa các yếu tố này là 65mm.
Hai khoảng cách mẫu phần tử khác nhau đã được sử dụng, 50 và 100mm. Một lần nữa, khoảng cách giữa hai đơn vị sưởi ấm đã bị bỏ ngỏ
Các yếu tố
Các phần tử rỗng màu đen của gốmx phát ra các bước sóng cực đại ở chế độ trung bình đến dài (2 - 10μm). Mỗi phần tử có kích thước là 245 x 60mm (lxw). Các bước sóng dài hơn liên quan đến các yếu tố gốm rất hiệu quả để làm nóng nhiều vật liệu polymer.
Instrumentation
Cặp nhiệt điện loại K được gắn vào bề mặt của mẫu bằng vít M3. Xi măng gốm đã được thử nghiệm tuy nhiên điều này không bám dính vào bề mặt của vật liệu. Với nhiệt độ cao cần thiết, không có chất kết dính có sẵn sẽ vẫn ổn định, do đó việc cố định cơ học được coi là cần thiết. Các cặp nhiệt điện được đặt ở trung tâm của từng mẫu và cũng cách mép 10 mm (cạnh) và 30 mm (quý) như trong Hình 2. Điều này đặt các cặp nhiệt điện trực tiếp trên các phần tử ống và ở giữa các phần tử sao cho tối đa chênh lệch nhiệt độ sẽ được ghi lại. Dữ liệu nhiệt độ được ghi lại trong các khoảng thời gian một giây.
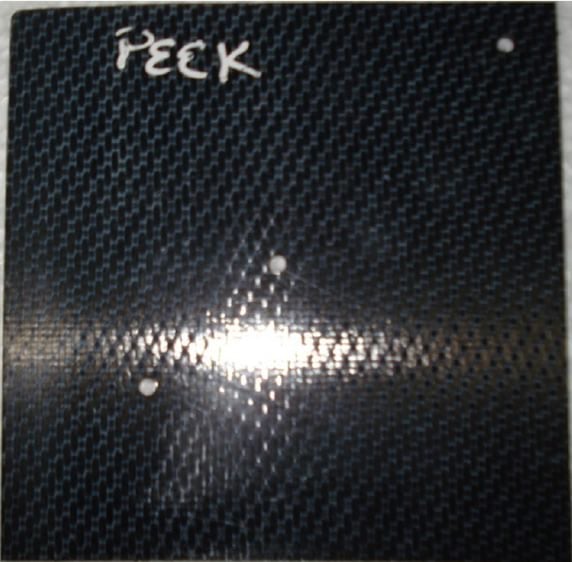
Thử nghiệm bánh sandwich
Máy thử sandwich là một máy thử phản ứng nhiệt vật liệu tiên tiến như trong Hình 2. Các loại lò sưởi hồng ngoại khác nhau có thể được gắn ở hai vị trí, hướng lên xuống theo chiều dọc. Điều này đảm bảo rằng vật liệu được thử nghiệm có thể được làm nóng từ đỉnh và / hoặc đáy. Bốn nhiệt kế quang không tiếp xúc được sử dụng để xác định nhiệt độ bề mặt trên và dưới của vật liệu được thử. Các bộ phát được phép làm nóng đến nhiệt độ hoạt động của chúng và vật liệu sau đó được đưa vào (các) bộ phát trong một khoảng thời gian xác định trước. Thử nghiệm này được thực hiện với cả hai phần tử đen 1kW vonfram (QTM) và 800W (FFEH) được gắn 75mm phía trên mẫu để xác định lò sưởi nào cho độ xuyên thấu tốt nhất qua vật liệu.
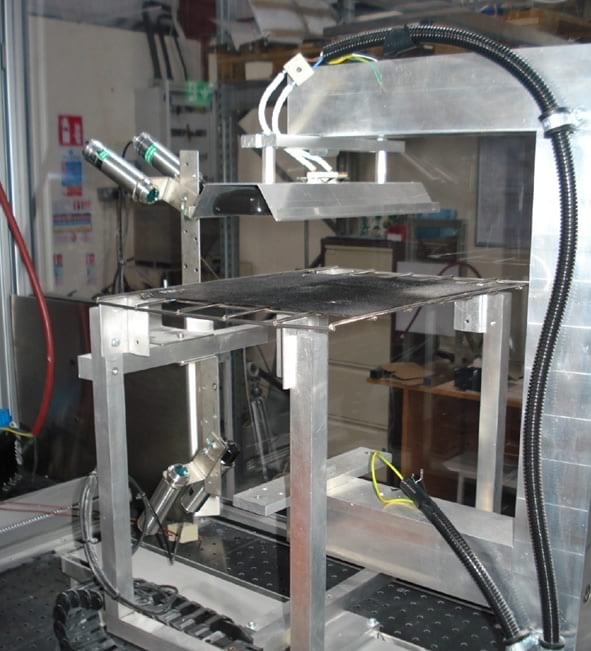
Kết quả
FastIR
Phần này báo cáo về kết quả tìm thấy đối với ống vonfram và halogen cho ba vật liệu được đề cập. Thử nghiệm được thực hiện với ba chiều cao lò sưởi khác nhau (55mm, 80mm & 95mm).
TUẦN
Các thử nghiệm ban đầu được tiến hành với mẫu PEEK và hai lò sưởi FastIR với ống halogen thạch anh 1500W cách nhau 110mm. Kết quả của thử nghiệm này, được hiển thị trong Hình 4, chỉ ra rằng mẫu không đạt được nhiệt độ yêu cầu.
Các phần tử đã được thay đổi thành các ống halogen sóng ngắn (QHL) 2000W cho thấy, ở cùng một khoảng cách, mẫu đạt và vượt quá nhiệt độ yêu cầu tại một địa điểm. Trong trường hợp này, nhiệt độ tối đa được ghi nhận là 485 ° C, tuy nhiên, sự khác biệt đáng kể về nhiệt độ (lên tới 83 ° C) cũng được phát hiện. Thời gian cần thiết để đạt được nhiệt độ mục tiêu 425 ° C là 99 giây. Điều này đã đạt được tại hai địa điểm duy nhất
Các ống thạch anh vonfram (QTL) (2000W) cũng đã được kiểm tra ở ba cấp độ với nhiệt độ tối đa giảm khi khoảng cách gia nhiệt tăng. Ở 55mm, nhiệt độ tối đa và tối thiểu 520 ° C đã được phát hiện. Nhiệt độ mục tiêu, trên toàn bộ mẫu vật liệu đã đạt được trong 206 giây. Tăng khoảng cách lên 80mm, các nhiệt độ này giảm xuống 450 ° C và 415 ° C và ở mức 95mm so với mẫu, nhiệt độ tối đa và tối thiểu của mẫu là 407 và 393 ° C.
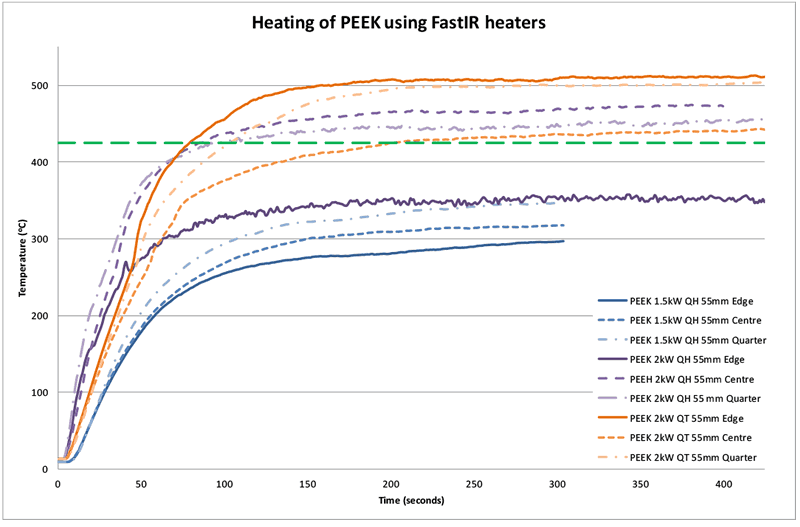
Hình 4 cho thấy sự chênh lệch nhiệt độ có thể xảy ra trên mẫu do sự gần gũi của máy sưởi với mẫu cũng như thời gian cần thiết để làm nóng vật liệu đến 425 ° C (206 giây đối với máy sưởi QT 2kW).
Các ống vonfram 150 ° W đã không được thử nghiệm vì nó được coi là hoạt động quan trọng hơn để tăng khoảng cách gia nhiệt hơn là giảm công suất của các phần tử được sử dụng.
Hình 5 cho thấy sự khác biệt trực quan trong mẫu trước và sau khi gia nhiệt.
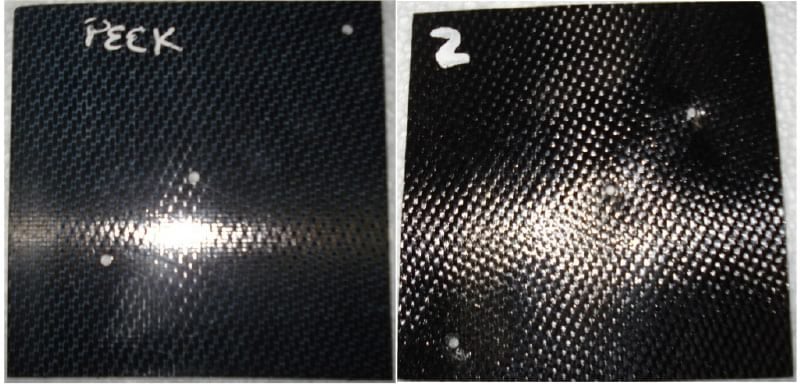
Bắc Kinh
PEKK được làm nóng bằng lò sưởi vonfram 2000W ở mức 55mm. Phản ứng nhiệt của vật liệu là tuyệt vời với nhiệt độ vượt quá 500 ° C được ghi lại. Nhiệt độ quy định tối thiểu đạt được trong 102 giây với nhiệt độ tối đa được ghi nhận vượt quá 500 ° C.
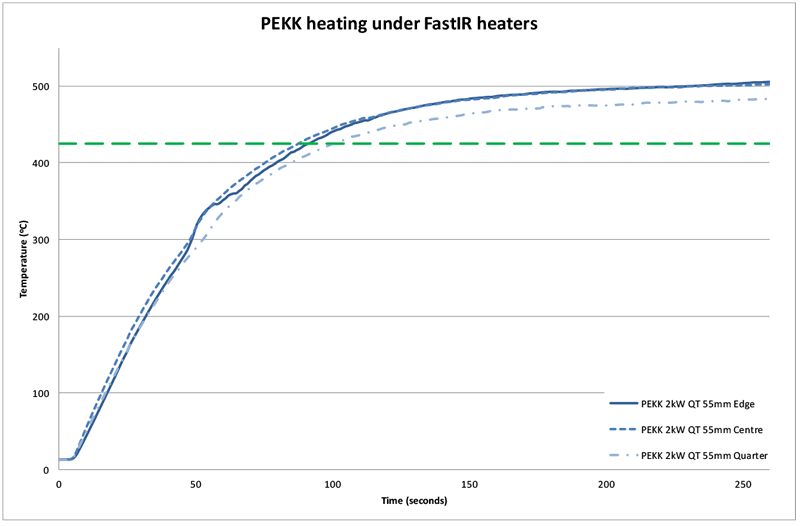
Đáng chú ý là mẫu này dường như cho thấy một số sự phân tách và tách lớp ở các cạnh và cả một số biến dạng bề mặt sau khi gia nhiệt như trong Hình 7, có thể là do sự hấp thụ độ ẩm trong quá trình lưu trữ và gia nhiệt nhanh xảy ra.
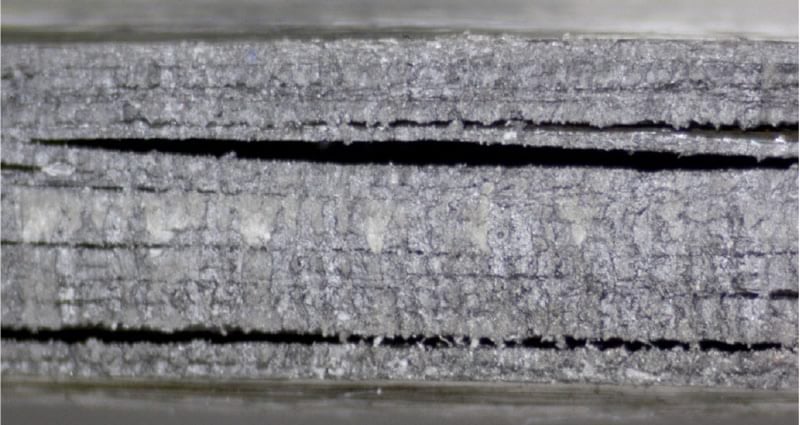
PPS
Vật liệu PPS đã được thử nghiệm với máy sưởi halogen và vonfram 2000W. Thử nghiệm halogen được thực hiện với khoảng cách 55mm và thử nghiệm vonfram ở 55mm và 95mm.
Dữ liệu một lần nữa cho thấy ống vonfram là chất gia nhiệt tốt hơn cho vật liệu này (so với lò sưởi halogen) với nhiệt độ cao hơn được ghi nhận ở mức tách 55mm và độ đồng đều của nhiệt độ trên mẫu cao hơn. Một biến thể 38 ° C đã được ghi nhận cho các lò sưởi halogen và 30 ° C cho các lò sưởi vonfram. Sự thay đổi được ghi lại này sẽ bị ảnh hưởng nhiều bởi vị trí của cặp nhiệt điện so với các ống. Vị trí cặp nhiệt điện giống hệt nhau không được đảm bảo.
Các thử nghiệm với PPS đã bị chấm dứt ngay sau khi vật liệu đạt đến nhiệt độ yêu cầu 425 ° C do có sự giải phóng khói có mùi lưu huỳnh từ các mẫu.
Ở khoảng cách 55mm, nhiệt độ mục tiêu được ghi lại sau 66 và 88 giây đối với lò sưởi halogen và vonfram ở mức 55mm tương ứng. Khi các lò sưởi vonfram được gắn ở 95mm từ mẫu, nhiệt độ mục tiêu không đạt được.
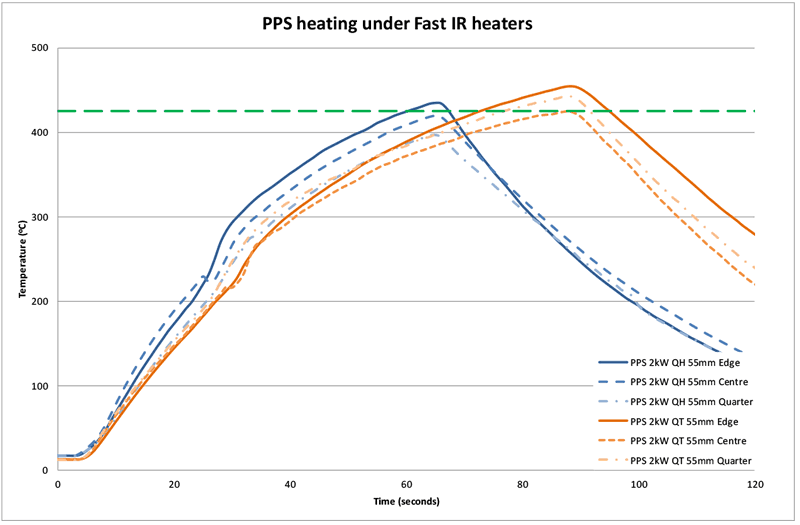
Rỗng đen
Các thử nghiệm ban đầu được tiến hành với sự phân tách vật liệu-nguyên tố là 50mm. Sự gia tăng nhiệt độ của vật liệu rất nhanh đối với tất cả các vật liệu. Từ khi bắt đầu lạnh, các phần tử rỗng mất khoảng 10-12 phút để làm nóng đến mức hoạt động ổn định (nhiệt độ bề mặt khoảng 700 ° C). Sự gia tăng nhiệt độ vật liệu tương tự như đường cong sưởi ấm của lò sưởi, tuy nhiên, có một độ trễ về thời gian trong việc này.
TUẦN
Biểu đồ thời gian cần thiết để làm nóng mẫu PEEK để đạt đến nhiệt độ xử lý cần thiết được trình bày bên dưới trong Hình 9. Điều này cho thấy thời gian gia nhiệt đến 425 ° C là khoảng 185 giây kể từ khi máy sưởi được bật ở 50mm. Nếu khoảng cách được tăng lên 100mm, thời gian được tăng lên 230 giây. Mẫu được để lại giữa hai trục trong khi gia nhiệt và lấy ra để làm mát.
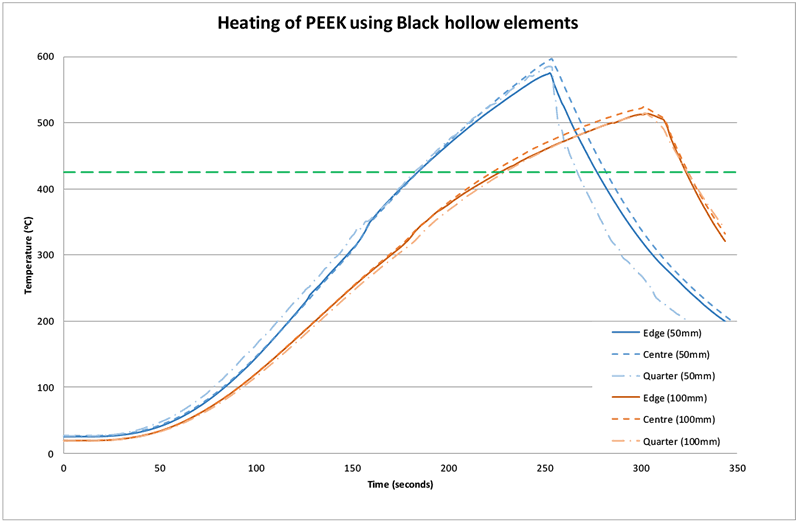
Bắc Kinh
Thời gian để PEKK đạt đến ngưỡng tối thiểu dài hơn một chút so với PEEK. Hai lý do có thể tồn tại cho điều này: 1.) vật liệu không hấp thụ bức xạ hồng ngoại cũng như PEEK và 2.) độ dày của vật liệu lớn gấp đôi (lần lượt là 1 và 2 mm). Thời gian cần thiết để đạt 425 ° C ở 50mm là 181 giây và ở 100mm, điều này tăng lên thành 244 giây
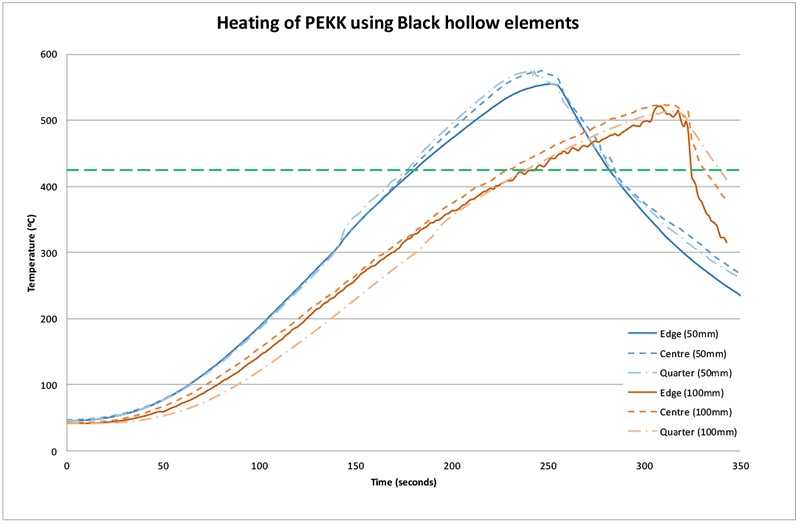
PPS
PPS đã làm nóng rất thành công với các phần tử rỗng màu đen với 425 ° C được ghi lại trong 171 giây và 219 giây ở 50 và 100mm tương ứng. Đường cong sưởi ấm cho vật liệu này được thể hiện trong Hình 11. Một lần nữa, một sự giải phóng khói có mùi lưu huỳnh đã xảy ra, tuy nhiên số lượng của nó không nhiều như với các lò sưởi halogen như chi tiết ở trên. Điều này có thể một phần là do sự vắng mặt của quạt ở mặt sau của tấm sưởi.
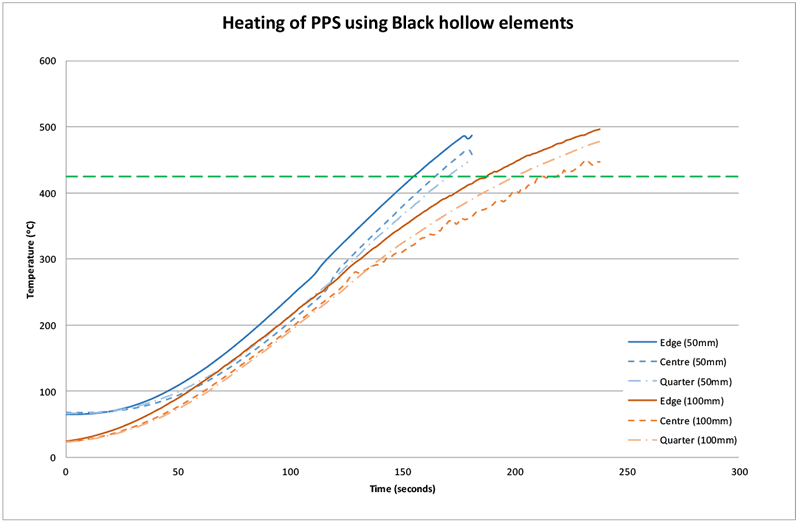
Tóm tắt về thời gian cần thiết để làm nóng vật liệu, với các nguyên tố gốm halogen, vonfram và rỗng, đến nhiệt độ mục tiêu được trình bày bên dưới trong Bảng 1. Vì việc gắn các phần tử halogen ở khoảng cách xa hơn 55mm không thành công trên toàn cầu, những kết quả này đã bị bỏ qua từ cái bàn.
Vật chất |
Loại nóng (nguồn)
|
Khoảng cách | Thời gian để đạt 425 ° C |
---|---|---|---|
TUẦN | QHL (2kW) | 55mm | 99 |
QTL (2kW) | 55mm | 206 | |
FFEH (800W) | 50mm | 185 | |
FFEH (800W) | 100mm | 230 | |
Bắc Kinh | QTL (2kW) | 55mm | 102 |
FFEH (800W) | 50mm | 181 | |
FFEH (800W) | 100mm | 244 | |
PPS | QHL (2kW) | 55mm | 66 |
QTL (2kW) | 55mm | 88 | |
FFEH (800W) | 50mm | 171 | |
FFEH (800W) | 100mm | 219 |
Thử nghiệm bánh sandwich
Thử nghiệm bánh sandwich đã được thực hiện để có được thông tin về việc truyền nhiệt qua vật liệu. Điều này được thực hiện bằng cách làm nóng mẫu từ một phía, đo nhiệt độ ở cả hai phía và so sánh kết quả. Các ống vonfram và các phần tử rỗng màu đen chỉ được kiểm tra, vì dựa trên kết quả FastIR, các ống halogen sóng ngắn không phải là máy sưởi phù hợp cho các vật liệu được đề cập.
Kết quả cho các yếu tố QTM cho thấy không có sự chênh lệch nhiệt độ đáng kể giữa bề mặt trên và dưới đối với vật liệu PEEK và PPS, tuy nhiên PPS nóng lên nhanh hơn và các đường cong cho vật liệu này hầu như không thể phân biệt được. Cần lưu ý rằng hai vật liệu này rất mỏng (≈ 1mm). Như mong đợi, chênh lệch nhiệt độ đối với PEKK lớn hơn (75 ± 2oC) do độ dày của nó (≈ 2 mm). Những kết quả này được hiển thị trong Hình 12 dưới đây.
Vì lý do vận hành, thử nghiệm chấm dứt khi nhiệt độ 300 ° C được phát hiện bằng nhiệt kế kế. Đỉnh nhìn thấy trong 30 giây đầu tiên của thử nghiệm là độ phản xạ và không phải là chỉ số nhiệt độ thực.
Những kết quả này chứng minh rằng khả năng thâm nhập IR tốt của vật liệu là có thể đối với PEEK và PPS bằng cách sử dụng lò sưởi loại vonfram. Tuy nhiên, sự cân bằng nhiệt độ cho PEKK không tốt bằng, thể hiện bằng sự chênh lệch nhiệt độ gần 75 ° C trong 18 giây cuối của thử nghiệm4.
Không thể di chuyển các mẫu vật liệu đến gần lò sưởi để phân tích ảnh hưởng của nó như thế nào vì góc nhọn cần thiết cho pyrometer để xem vật liệu sẽ làm sai lệch số đọc.
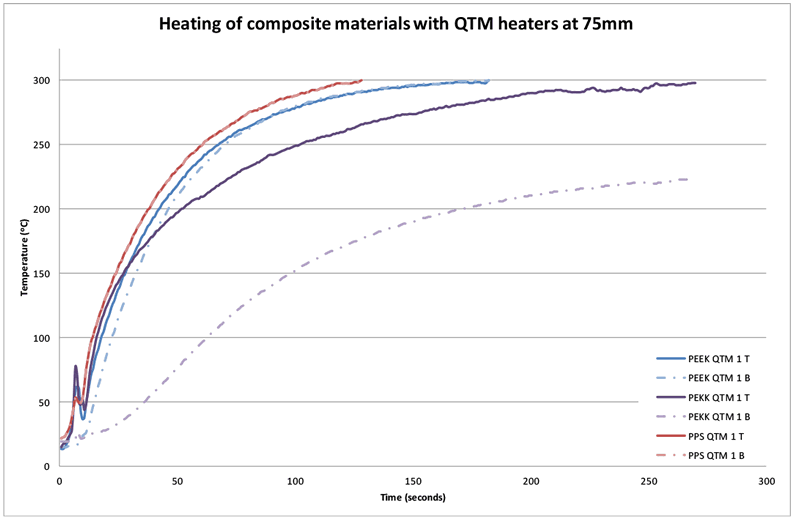
Việc làm nóng các mẫu với các phần tử rỗng màu đen ở cùng khoảng cách (75mm) cho thấy xu hướng tương tự với chênh lệch nhiệt độ lớn hơn (45 ± 2 ° C) đối với vật liệu PEKK dày hơn (so với vật liệu mỏng hơn). Nhiệt độ của bề mặt trên và dưới của PEEK hầu như không thể phân biệt được; tuy nhiên, có sự khác biệt về nhiệt độ của PPS (25 ± 2 ° C). Dữ liệu này được chỉ ra trong Hình 13. Điều này cho thấy rằng thâm nhập IR của PPS với bức xạ bước sóng dài hơn không tốt bằng IR vonfram ngắn hơn, tuy nhiên, cân bằng nhiệt độ của PEKK là tốt hơn (nhưng không lý tưởng).
Ở mức tách 75mm, nhiệt độ và tốc độ gia nhiệt cao nhất thu được bằng cách sử dụng lò sưởi vonfram dường như mâu thuẫn với kết quả trục lăn trước đó. Tuy nhiên, điều này không nên được sử dụng như một hướng dẫn vì chỉ sử dụng một lò sưởi duy nhất. Hơn nữa, những đặc điểm này sẽ được cải thiện bằng cách sử dụng một loạt các lò sưởi trái ngược với một lò sưởi duy nhất.
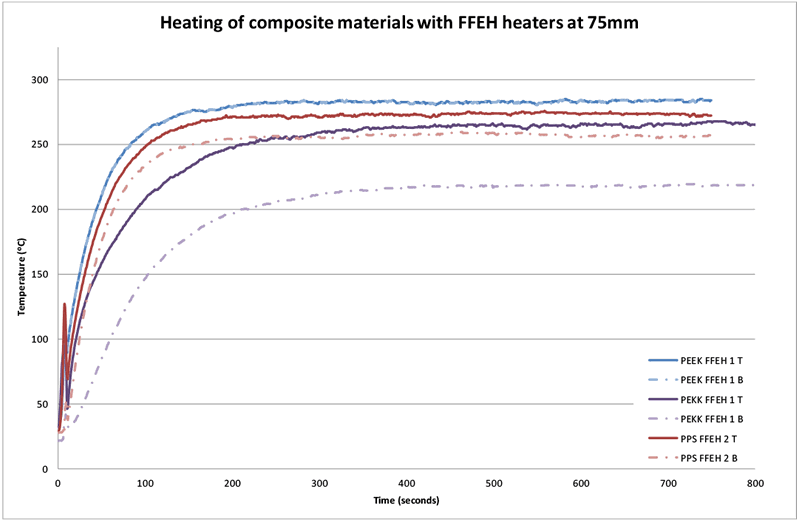
Kết luận
- Các thử nghiệm được thực hiện và chi tiết ở trên chỉ ra rằng việc gia nhiệt ba vật liệu tổng hợp carbon nhiệt dẻo đến tối thiểu 425 ° C là có thể với cả hai yếu tố halogen sóng trung bình và đen rỗng.
- Nhiệt độ tối đa cao hơn có thể đạt được bằng cách sử dụng phần tử rỗng màu đen Ceramicx 800W (FFEH).
- Thời gian cần thiết để làm nóng PEEK đến 425 ° C là 206 giây đối với lò sưởi ống vonfram 2kW ở 55mm và 230 giây đối với các yếu tố FFEH ở 100mm
- Thời gian cần thiết để làm nóng PEKK đến 425 ° C là 102 giây đối với lò sưởi ống vonfram 2kW ở 55mm và 244 giây đối với các yếu tố FFEH ở 100mm
- Thời gian cần thiết để làm nóng PPS đến 425 ° C là 88 giây đối với lò sưởi ống vonfram 2kW ở 55mm và 219 giây đối với các yếu tố FFEH ở 100mm
- Nhiệt độ tối đa, tốc độ gia nhiệt vật liệu có thể đạt được và tính đồng nhất nhiệt độ bề mặt là một chức năng mạnh mẽ của khoảng cách mà máy sưởi được gắn từ vật liệu.
- Sự thâm nhập IR tuyệt vời và do đó cân bằng nhiệt độ, thông qua độ dày vật liệu, của PPS và PEEK đã đạt được với halogen sóng trung bình (vonfram). Sự cân bằng nhiệt độ đạt được với PEKK không tốt bằng các vật liệu khác.
- Sự thâm nhập IR và cân bằng nhiệt độ tuyệt vời đã được nhìn thấy với PEEK sử dụng các yếu tố rỗng màu đen. Khách sạn này không tốt như PEKK và PPS.
Dựa trên dữ liệu thử nghiệm ở trên và các phần tử vật liệu gần nhau được yêu cầu để đạt được nhiệt độ cần thiết để tạo thành các vật liệu được đề cập, nó xuất hiện bộ phát hồng ngoại tốt nhất là phần tử rỗng phẳng đen đầy đủ của Ceramicx 800W. Trong khi thời gian để đạt được nhiệt độ yêu cầu dài hơn một chút so với lò sưởi vonfram, sự gần gũi của các yếu tố được sử dụng sẽ dẫn đến sự đồng đều nhiệt độ bề mặt tốt hơn. Hơn nữa, các yếu tố gốm đã được bắt đầu từ nhiệt độ phòng và cần khoảng 12 phút để đạt đến cấp độ hoạt động. Do đó, thời gian này có thể được rút ngắn đáng kể bằng cách làm nóng trước các yếu tố.
Cũng cần lưu ý rằng những kết quả này dựa trên các mẫu được tạo sẵn để thử nghiệm (tức là độ dày 1mm và 2 mm). Việc gia nhiệt các bộ phận dày hơn có thể yêu cầu thay đổi đáng kể công nghệ gia nhiệt để nghiên cứu nhằm đảm bảo cấu hình nhiệt độ, trên bề dày vật liệu, đồng nhất và phù hợp cho các hoạt động tạo hình tiếp theo.
1 Polyet ether ketone
2 Polyphenylene sulfua
3 Polyetherketoneketon
4 Sự khác biệt trung bình giữa các bề mặt trên và dưới được thực hiện trong 18 giây cuối cùng của thử nghiệm.
Từ chối trách nhiệm
Những kết quả kiểm tra này cần được xem xét cẩn thận trước khi một loại phát hồng ngoại nhất định được xác định sử dụng.
Các xét nghiệm lặp lại được thực hiện bởi các công ty khác có thể không đạt được kết quả tương tự. Sự khác biệt trong các điều kiện thí nghiệm có thể làm thay đổi kết quả. Các nguồn lỗi khác bao gồm: thương hiệu của bộ phát được sử dụng, hiệu quả của bộ phát, công suất được cung cấp, khoảng cách từ vật liệu được thử đến bộ phát được sử dụng và môi trường. Các vị trí đo nhiệt độ cũng có thể gây ra sự thay đổi trong kết quả.