AUTHOR | تاريخ الإنشاء | VERSION | رقم المستند |
---|---|---|---|
الدكتور بيتر مارشال | 1 ديسمبر 2017 | V1.1 | CC11 - 00120 |
المُقدّمة
يدرس هذا البحث تأثير تعريض عاكسات الأشعة تحت الحمراء المصنوعة من الفولاذ المقاوم للصدأ والفولاذ المقاوم للصدأ Ceramicx لدرجات حرارة عالية على انعكاسية المادة. تم إجراء مقارنة بين العاكسات الجديدة والمؤكسدة لقياس تأثير ذلك على النسبة المئوية لتدفق الحرارة الإشعاعي.
المواد
واستخدمت في هذه الدراسة عاكسون قياسيان الشكل (RAS 1) للعناصر الخزفية. مرة واحدة كان Ceramicx معيار الصلب aluminsed في حين أن الآخر كان الفولاذ المقاوم للصدأ. تم استخدام نفس 1000W FTE المزجج الأسود في جميع الاختبارات.
خدمة التوصيل
وضعت عاكسات في الفرن في 600 ° C لمدة 8 ساعات في ظل الظروف الجوية القياسية. بعد التسخين ، سُمح لهم بالتبريد داخل الفرن حتى يبرد. بمجرد الانتهاء من هذه العملية ، تم تجهيز FTE المزجج بلون أسود 1000W بالعاكس وتم تسجيل تدفق الحرارة باستخدام الإجراء القياسي.
يفحص روبوت Ceramicx Herschel للتدفق الحراري إجمالي تدفق الحرارة (W.cm)-2) وهو الحادث على المستشعر. يمكن تركيب السخانات في Herschel وتحليلها باستخدام روتين تخطيط تدفق الحرارة بالأشعة تحت الحمراء 3D. يستخدم هذا النظام الآلي مستشعر الأشعة تحت الحمراء الذي يتم توجيهه آليًا حول نظام شبكة إحداثي محدد مسبقًا أمام باعث المدفأة قيد الاختبار. يحتوي المستشعر على مستوى تدفق الحرارة الأقصى 2.3 W.cm-2 ويقيس الأشعة تحت الحمراء في الفرقة ميكرومتر 0.4-10. نظام الإحداثيات عبارة عن شبكة مكعبة 500mm أمام باعث التدفئة ، انظر الشكل 1. يقوم الروبوت بتحريك المستشعر بزيادات 25mm على طول مسار أفعواني في الاتجاهين X و Z ، في حين يتم تثبيت باعث التسخين على عربة انزلاق تزيد بخطوات 50mm على طول الاتجاه Y.
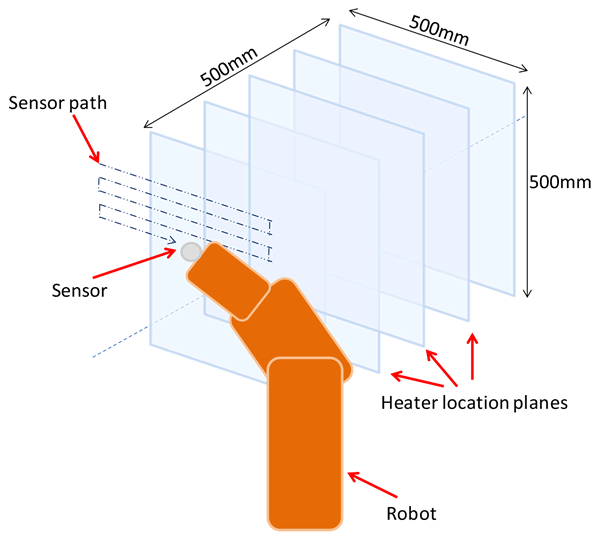
يمكن ربط نتائج الآلة بنسبة مئوية من إجمالي الطاقة المستهلكة التي يتم إرجاعها مع تدفق الحرارة المشع من المدفأة. هذا يتناقص مع المسافة من المدفأة لأن تدفق الحرارة المشع يختلف عن المدفأة.
النتائج
المعالجة الحرارية
بعد المعالجة الحرارية ، أظهرت العاكس الصلب بالألمنيوم مساحة بلون رمادي غير لامع في الجزء الأوسط من العاكس بينما أظهر العاكس من الصلب غير القابل للصدأ اللون الأزرق / الأرجواني العميق ، كما هو موضح في الشكل 1 ، أدناه.
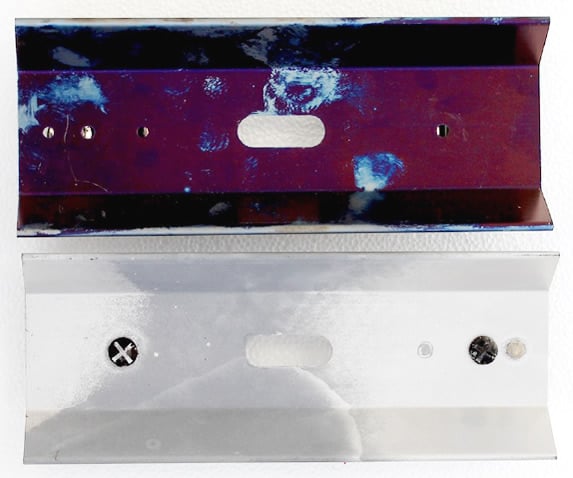
قياس تدفق الحرارة
توضح عاكسات الألمنيوم والفولاذ المقاوم للصدأ غير المستخدمة أنه يتم تسجيل الحد الأقصى لنسبة تدفق الحرارة عند 100mm من العنصر ، كما هو موضح في الشكل 3 أدناه. تشير نتائج تدفق الحرارة إلى أن النسبة المئوية للتدفق الحراري المسجلة أعلى بالنسبة للعاكس الصلب المصنوع من الألمنيوم مقارنة بعاكس الفولاذ المقاوم للصدأ ، بما يتوافق مع الكثير من المؤلفات المنشورة حتى الآن بواسطة Ceramicx وغيرها.
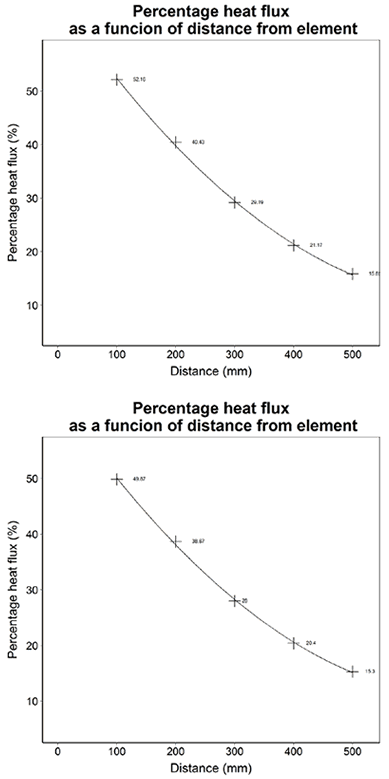
إن التعرض لفترات طويلة لدرجات الحرارة المرتفعة يسبب الأكسدة وبالتالي تنخفض كفاءة العاكس. بالنسبة للصلب المصنوع من الألمنيوم ، تتسبب طبقة الأكسيد المرئي في انخفاض 18.6٪ ، كما هو موضح في الشكل 4 ، أدناه. بالنسبة للفولاذ المقاوم للصدأ ، فإن هذا النقص هو 2٪ ، والذي يقع ضمن حدود الخطأ التجريبي.
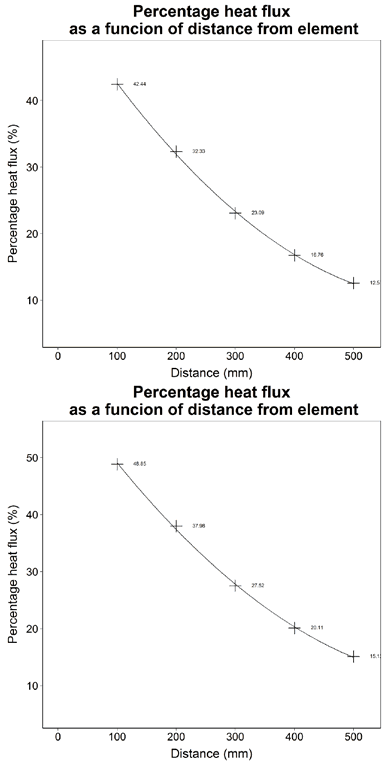
وكان ذروة تدفق الحرارة للصلب غير المعالج بالألمنيوم أعلى من الفولاذ المقاوم للصدأ. كان هذا متوقعًا بالنظر إلى أن الخصائص العاكسة للصلب المنيوم أفضل من الفولاذ المقاوم للصدأ. بعد المعالجة الحرارية ، يوضح الجدول 1 أن ذروة تدفق الحرارة للصلب الملموس انخفضت بشكل كبير حيث تمتص طبقة الأكسيد الموجودة في المادة الأشعة تحت الحمراء. على العكس من ذلك ، فإن التغير في لون عاكس الفولاذ المقاوم للصدأ ، تمشياً مع النسبة المئوية لقياس تدفق الحرارة ، أظهر انخفاضًا طفيفًا فقط.
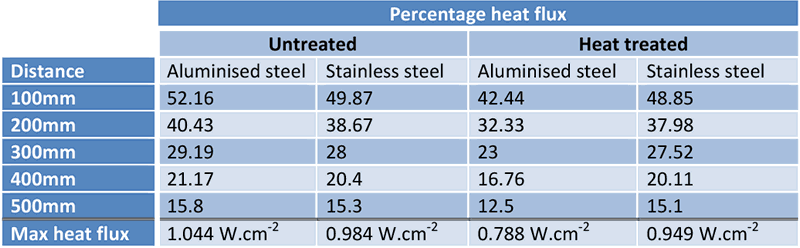
لم يلاحظ أي تغيير واضح في نمط الانبعاثات للعنصر. علاوة على ذلك ، كان التغير في تدفق الحرارة ، كدالة عن بعد ، كما هو متوقع.
وفي الختام
كما هو موضح سابقًا من قبل Ceramicx ، فإن استخدام عاكس فولاذي مصقول مصنوع من الألمنيوم يزيد من نسبة تدفق الحرارة الإشعاعية المنبعثة نحو هدف التدفئة مقارنة مع الفولاذ المقاوم للصدأ. بالنسبة لتطبيقات درجات الحرارة المنخفضة ، حيث من غير المرجح أن يحدث أكسدة الألومنيوم ، فإن الصلب الملمع يظهر أنه مادة أفضل أداء. بالنسبة للتطبيقات ذات درجات الحرارة المرتفعة ، حيث يحتمل حدوث أكسدة الألومنيوم ، يعد الفولاذ المقاوم للصدأ خيارًا أفضل لأنه يؤدي إلى نسبة أكبر من الطاقة الإشعاعية الموجهة نحو المادة المستهدفة.
إخلاء المسئولية
يجب النظر في نتائج الاختبار هذه بعناية قبل تحديد نوع باعث الأشعة تحت الحمراء المطلوب استخدامه في العملية. قد لا تحقق الاختبارات المتكررة التي أجرتها شركات أخرى نفس النتائج. هناك احتمال للخطأ في تحقيق شروط الإعداد والمتغيرات التي قد تغير النتائج ، وتشمل العلامة التجارية للباعث المستخدم ، وكفاءة الباعث ، والطاقة المزودة ، والمسافة من المادة المختبرة إلى الباعث المُستخدم والبيئة . قد تختلف أيضًا المواقع التي يتم فيها قياس درجات الحرارة وبالتالي تؤثر على النتائج.