AUTEUR | DATE CRÉÉE | VERSION | NUMÉRO DE DOCUMENT |
---|---|---|---|
Dr. Peter Marshall | 1 Décembre 2017 | V1.1 | CC11 - 00120 |
Introduction
Cet article étudie l'influence de l'exposition des réflecteurs infrarouges en acier aluminisé Ceramicx et en acier inoxydable à des températures élevées sur la réflectivité du matériau. Une comparaison est faite entre les réflecteurs neufs et oxydés pour mesurer l'influence de celui-ci sur le pourcentage de flux thermique radiatif.
Matériaux
Deux réflecteurs de forme standard (RAS 1) pour éléments en céramique ont été utilisés dans cette étude. Une fois était en acier aluminé standard Ceramicx tandis que l'autre était en acier inoxydable. Le même 1000W FTE vitré noir a été utilisé dans tous les tests.
Method
Les réflecteurs ont été placés dans le four à 600 ° C pendant 8 heures dans des conditions atmosphériques standard. Après chauffage, on les laissait refroidir dans le four. Une fois ce processus terminé, un FTE vitré noir 1000W a été installé sur le réflecteur et le flux de chaleur a été enregistré en utilisant la procédure standard.
Le robot à flux de chaleur Ceramicx Herschel examine le flux de chaleur total (W.cm-2) qui est incident sur le capteur. Les appareils de chauffage peuvent être montés dans le Herschel et analysés à l'aide de la routine de cartographie du flux de chaleur infrarouge 3D. Ce système automatisé utilise un capteur infrarouge qui est guidé de manière robotique autour d'un système de grille de coordonnées prédéterminé en face de l'émetteur de chauffage soumis au test. Le capteur a un flux de chaleur maximal de 2.3 W.cm-2 et mesure l'IR dans la bande 0.4-10 micromètres. Le système de coordonnées est une grille cubique 500mm située devant l'émetteur de chauffage, voir la figure 1. Le robot déplace le capteur par incréments de 25mm le long d'un chemin en serpentin dans les directions X et Z, tandis que l'émetteur de chauffage est monté sur un chariot coulissant qui s'incrémente par incréments de 50mm dans la direction des Y.
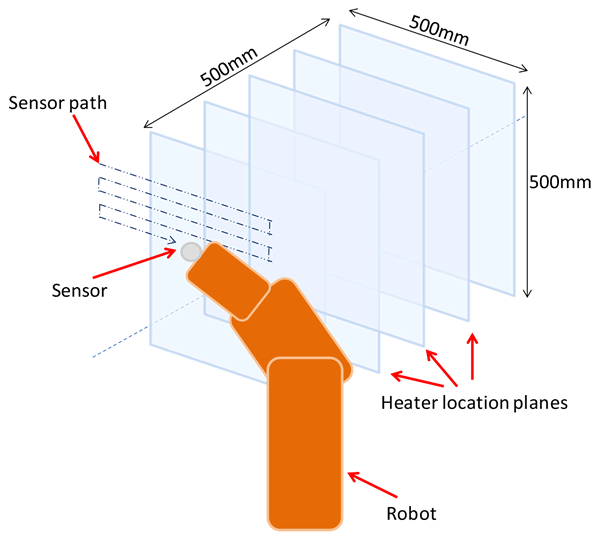
Les résultats de la machine peuvent être corrélés à un pourcentage de l'énergie totale consommée renvoyée sous forme de flux de chaleur rayonnante provenant de l'appareil de chauffage. Cela diminue avec la distance du radiateur lorsque le flux de chaleur rayonnante diverge du radiateur.
Résultats
Traitement thermique
Après traitement thermique, le réflecteur en acier aluminisé présentait une zone gris mat dans la partie centrale du réflecteur, tandis que le réflecteur en acier inoxydable présentait une couleur bleu / violet foncé, comme illustré à la figure 1 ci-dessous.
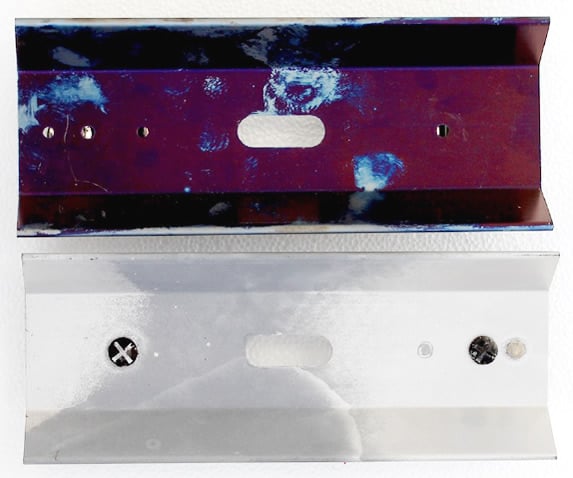
Mesure du flux thermique
Les réflecteurs inutilisés aluminisés et en acier inoxydable montrent que le pourcentage maximum de flux de chaleur est enregistré à 100mm de l'élément, comme le montre la figure 3 ci-dessous. Les résultats de flux de chaleur montrent que le pourcentage de flux de chaleur enregistré est plus élevé pour les réflecteurs en acier aluminisé que pour les réflecteurs en acier inoxydable, ce qui est conforme à de nombreux ouvrages publiés à ce jour par Ceramicx et d'autres.
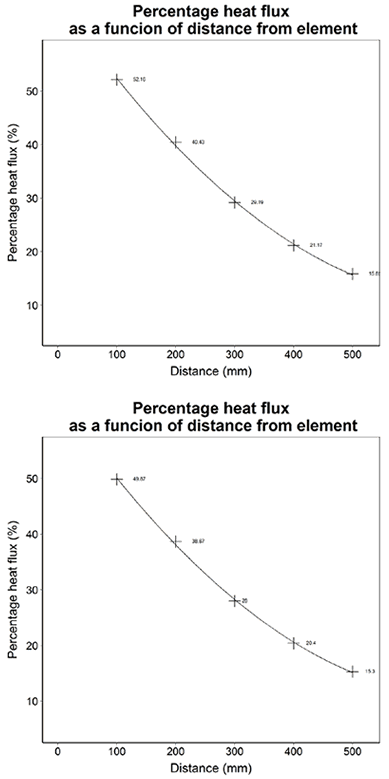
Une exposition prolongée à des températures élevées provoque une oxydation et donc une perte d'efficacité du réflecteur. Pour l'acier aluminisé, la couche d'oxyde visible provoque une diminution du% 18.6, comme illustré à la figure 4 ci-dessous. Pour l'acier inoxydable, cette diminution est de 2%, ce qui se situe bien dans les limites de l'erreur expérimentale.
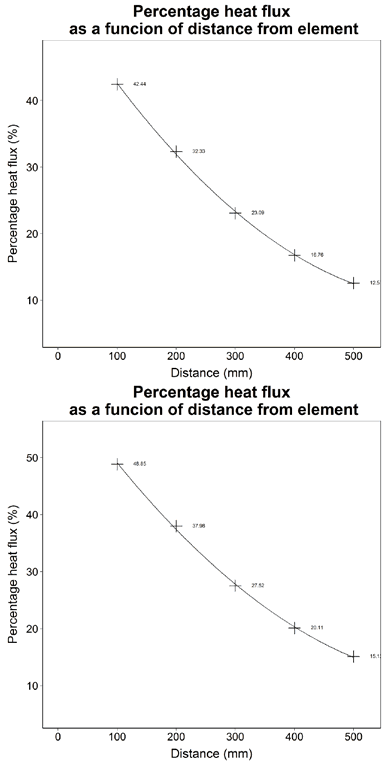
Le flux thermique de pointe pour l'acier aluminisé non traité était plus élevé que pour l'acier inoxydable. Cela était prévu étant donné que les propriétés réfléchissantes de l'acier aluminisé sont meilleures que celles de l'acier inoxydable. À la suite du traitement thermique, le tableau 1 montre que le flux thermique de pointe pour l’acier aluminisé a chuté de façon spectaculaire à mesure que la couche d’oxyde sur le matériau absorbe le rayonnement infrarouge. Inversement, le changement de couleur du réflecteur en acier inoxydable, en ligne avec la mesure du pourcentage de flux de chaleur, n'a montré qu'une faible diminution.
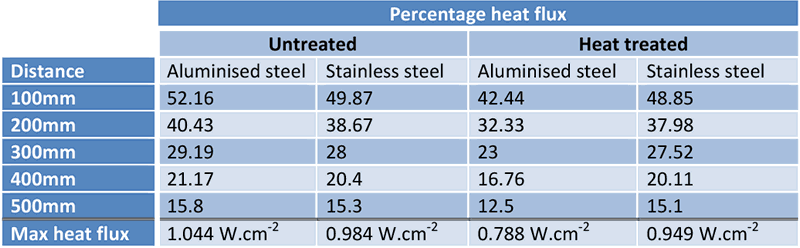
Aucun changement distinct n'a été observé dans le schéma d'émission de l'élément. De plus, l'évolution du flux thermique, en fonction de la distance, était conforme aux attentes.
Conclusion
Comme indiqué précédemment par Ceramicx, l'utilisation d'un réflecteur en acier aluminisé poli augmente le pourcentage de flux de chaleur radiative émis vers la cible chauffante par rapport à l'acier inoxydable. Pour les applications à basse température, où l'oxydation de l'aluminium est peu probable, l'acier aluminisé s'avère être un matériau plus performant. Pour les applications à haute température, où l'oxydation de l'aluminium est susceptible de se produire, l'acier inoxydable est un meilleur choix car il conduit à une plus grande proportion d'énergie radiative dirigée vers le matériau cible.
Clause de non-responsabilité
Ces résultats de test doivent être soigneusement pris en compte avant de déterminer le type d'émetteur infrarouge à utiliser dans un processus. Des tests répétés menés par d’autres sociétés peuvent ne pas aboutir aux mêmes résultats. Il existe une possibilité d'erreur dans la réalisation des conditions d'installation et les variables susceptibles d'altérer les résultats incluent la marque de l'émetteur utilisé, l'efficacité de l'émetteur, la puissance fournie, la distance du matériau testé à l'émetteur utilisé et l'environnement. . Les emplacements où les températures sont mesurées peuvent également différer et donc affecter les résultats.