AUTEUR | DATE CRÉÉE | VERSION | NUMÉRO DE DOCUMENT |
---|---|---|---|
Dr. Gerard McGranaghan | 27 Mars 2014 | V1.1 | CC11 - 00013 |
Introduction
Ce rapport décrit une série d'expériences sur des cassettes en quartz dans lesquelles des matériaux réflecteurs en acier inoxydable et en acier aluminisé ont été comparés. Les tests ont été effectués avec des réflecteurs et sans réflecteurs.
Numéro de test | Numéro de spécimen | Type | Puissance (W) | espace extérieur plus propre, | Réflecteur |
---|---|---|---|---|---|
1 | 1 | StSt | 800 | décoloré | Réflecteur |
2 | 2 | StSt | 800 | espace extérieur plus propre, | Réflecteur |
3 | 3 | Al St | 800 | espace extérieur plus propre, | Réflecteur |
4 | 1 | StSt | 800 | décoloré | aucune |
5 | 2 | StSt | 800 | espace extérieur plus propre, | aucune |
6 | 3 | Al St | 800 | espace extérieur plus propre, | aucune |
7 | 4 | Al St | 800 | espace extérieur plus propre, | aucune |
Les corps en acier inoxydable, bien que brillants au début, ont tendance à se décolorer rapidement avec la température. Afin d'évaluer l'effet de cette décoloration, un nouvel élément en acier inoxydable «propre» a été testé pour la sortie du flux de chaleur. Les résultats sont présentés sur la figure 1. L'élément montre un retour de 53.1% à 100mm, diminuant jusqu'à 17.0% à 500mm. Après les tests, l'élément s'était considérablement décoloré.
Afin de comparer le rendement émissif de nouveaux éléments «propres» avec des éléments déjà décolorés, un deuxième élément en acier inoxydable a été trempé dans un four à 400 ° C pendant 30 minutes. Une fois retiré, l'élément était de couleur oxyde de paille clair partout. Cependant, lorsqu'ils ont été chauffés sur le banc d'essai, les zones environnantes ont continué à se décolorer rapidement et sont devenues similaires au premier spécimen en acier inoxydable comme le montre la figure 2 (2). Les résultats des tests à 53.1% et 17.1% n'indiquent aucune différence significative de performance entre les deux éléments.
Par conséquent, un élément en acier inoxydable 800W se décolore assez rapidement du nouveau et la différence d'émission radiative entre un élément décoloré neuf et ancien est négligeable.
Lorsqu'un élément en acier aluminisé a été testé dans la même configuration, cela a donné de meilleurs résultats que l'un ou l'autre des éléments en acier inoxydable. La figure 1 montre comment l'élément AS a renvoyé 54.3% à 100mm et environ 17.8% à 500mm. Par rapport au corps en acier inoxydable, l'augmentation du rendement est probablement due à la faible émissivité du revêtement en acier aluminisé qui conduit à une réflectivité et à une réorientation de l'énergie infrarouge vers la cible plus élevées, mais aussi à sa résistance à la dégradation de la surface à un niveau plus élevé. puissances (1000W). La figure 2 (1) montre la cassette en acier aluminisé après essai; cela ne montre aucune dégradation de surface et, à l'exception de quelques signes révélateurs, est presque impossible à distinguer d'un nouvel élément.
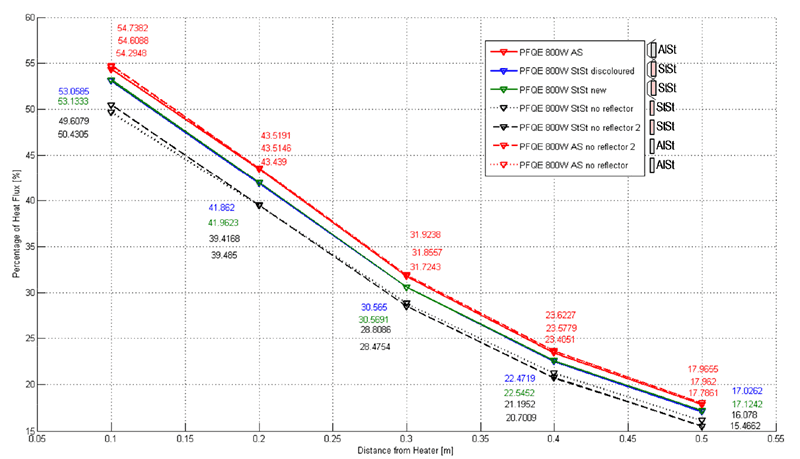
Ensuite, le réflecteur a été retiré et les mêmes éléments ont été testés à nouveau. Les résultats sont présentés sur la figure 1. Deux éléments en acier inoxydable ont été testés sans le réflecteur et montrent une baisse de performance d'environ 3 à 3.5% à 100 mm par rapport aux deux boîtiers «avec réflecteur». Cela prouve que le corps de l'élément inoxydable chauffe à un point tel qu'une décoloration se produit, et le changement ultérieur de l'émissivité de surface conduit à des pertes radiatives plus élevées de l'arrière de la cassette en acier inoxydable. Par conséquent, un réflecteur supplémentaire d'un certain type est recommandé lors de l'utilisation d'éléments en acier inoxydable, en particulier à des puissances élevées ou à des températures ambiantes où une décoloration du corps de la cassette est plus probable.
En revanche, les cassettes en acier aluminisé fonctionnent aussi bien avec ou sans réflecteurs. C'est ce que montre la figure 1 où les cassettes en acier aluminisé non réflecteur retournent toutes les deux autour de 54.7%. La cassette AS avec réflecteur a renvoyé 54.3%, bien que 0.4% soit inférieur au boîtier sans réflecteur, cela reste dans les variations expérimentales.
La cassette en acier aluminisé fonctionne environ 4-5% mieux qu'un élément en acier inoxydable sans réflecteur.
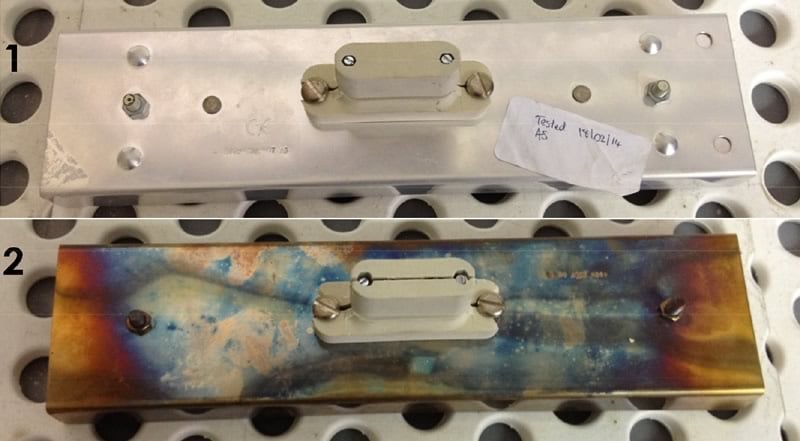
Résumé
Dans les éléments FQE et PFQE, les corps en acier inoxydable exposés à des températures élevées présenteront une dégradation de la surface conduisant à une diminution de la réflectance et à une augmentation de l'émissivité vers l'arrière nécessitant ainsi un réflecteur indépendant pour améliorer les performances.
Les corps en acier aluminisé ne présentent pas la même dégradation et comme l'émissivité reste constamment élevée, ceux-ci ne nécessitent pas de réflecteur.
Notes
Il faut l'explorer si la perte de réflectivité du corps en acier inoxydable se retrouve également dans les éléments à faible puissance. Dans les cassettes de faible puissance, la température de fonctionnement peut être nettement inférieure, par conséquent, l'acier inoxydable peut ne pas former d'oxydes et se décolorer.
Cependant, la formation d'oxydes est entraînée par la température, donc un élément de faible puissance fonctionnant dans un four fermé à des températures ambiantes élevées peut subir de telles températures élevées et également commencer à s'oxyder. À partir des essais au four, l'oxydation de l'acier inoxydable commence à se produire progressivement à partir d'environ 150 ° C, devenant très sombre à partir de 550 ° C.
Dans certains environnements, si de l'acier aluminisé est utilisé à des températures supérieures à 500 ° C en continu, un écaillage de l'aluminium peut se produire, ce qui entraînera également une dégradation des performances. Cependant, cela ne se produit pas dans des conditions normales. Le rapport technique Ceramicx CCII-00014 décrit plus en détail la résistance de l'aluminium et ne montre aucune détérioration de la surface jusqu'à environ 630 ° C.
Certains processus peuvent conduire à une nouvelle contamination de la surface du réflecteur entraînant une diminution des performances. Un réflecteur propre fonctionnera à des niveaux optimaux.
Ces problèmes de surchauffe peuvent être évités par une surveillance et une régulation soigneuses de la température dans le four ou sur les réflecteurs de température eux-mêmes.
Clause de non-responsabilité
Ces résultats de test doivent être soigneusement pris en compte avant de déterminer le type d'émetteur infrarouge à utiliser dans un processus. Des tests répétés effectués par d'autres sociétés peuvent ne pas aboutir aux mêmes résultats. Il existe une possibilité d'erreur dans la réalisation des conditions de configuration et des variables susceptibles de modifier les résultats, notamment la marque de l'émetteur utilisé, l'efficacité de l'émetteur, la puissance fournie, la distance entre le matériau testé et l'émetteur utilisé et l'environnement . Les emplacements où les températures sont mesurées peuvent également différer et donc affecter les résultats.