저자 | 작성일 | 버전 | 문서 번호 |
---|---|---|---|
피터 마샬 박사 | 8 4월 2016 | V1.1 | CC11 – 00101 |
개요
CCP Gransden은 Ceramicx에 접근하여 성형 작업을 위해 열가소성 탄소 섬유 프리프 레그 재료를 가열하는 적외선 오븐을 구축했습니다. 이 테스트 작업은 판매 제안서 (CSP 000 008)에 정의 된 기능의 일부로 수행되었습니다. 425 단계에는이 프로젝트를위한 적외선 히터 평가 및 선택이 포함되며 최소 재료 온도는 XNUMX ° C입니다.
재료 설명
두 재료의 세 가지 샘플을 230 x 230 x 1mm 조각으로 받았습니다. 이 경우 매트릭스는 PEEK였습니다.1 그리고 PPS2. PEKK의 작은 샘플3 200 x 150 x 2mm의 크기로도 받았습니다. 광택이 나는 검은 색 마감 처리로 견고하고 매끄 럽습니다. PEEK 및 PPS 샘플의 표면에서 표면에 작은 패턴이 보였다.
PEEK 및 PPS 샘플을 115 x 115 mm 조각으로 절단 하였다. PEKK 재료를 100 x 75mm 조각으로 절단했다.
방법
2 개의 별개의 히터 패밀리가 평가되었다; 할로겐 (QH 및 QT) 및 흑색 중공 세라믹 (FFEH). 각각의 경우에, 플래 튼은 조정 가능한 높이로 재료 샘플의 위와 아래에 장착되었다.
FastIR
Ceramicx의 FastIR 500 장치 2 개를 재료 위와 아래에 장착 할 수 있도록 마운팅 시스템이 제조되었습니다. FastIR 500는 500 x 500 mm 케이스에 병렬로 장착 된 7 개의 가열 요소로 구성됩니다. 이 튜브 사이의 간격은 81mm입니다. 1500W 및 2000W 'long'(총 길이 : 473mm) 요소가 각각 21 또는 28kW의 두 단위에서 총 출력을 제공하는 데 사용되었습니다. 히터 유닛은 소자 표면과 샘플 사이의 거리가 55mm와 95mm 사이에서 변하도록 장착되었다.
사용 된 실험 프로토콜은 다음과 같습니다.
- 팬 켜기
- 중앙 3 개의 가열 요소가 켜져 있고 맨 위와 맨 아래
- 4 개의 가열 요소 외부에서 전원을 켠 후 상단 및 하단
두 FastIR 장치 사이의 샘플 이미지는 그림 1에 표시되어 있습니다. 두 가열 장치 사이의 간격을 막는 데 사용 된 것은 없습니다
요소
FastIR 장치에는 두 가지 유형의 요소를 장착 할 수 있습니다. 석영 할로겐 및 석영 텅스텐. 이 소자들은 서로 다른 피크 적외선 파장을 방출합니다. 대략 1.0 – 1.2μm의 할로겐 및 1.6 – 1.9μm 사이의 텅스텐. 각 튜브의 직경은 10mm, 총 길이는 473mm, 가열 길이는 415mm입니다.
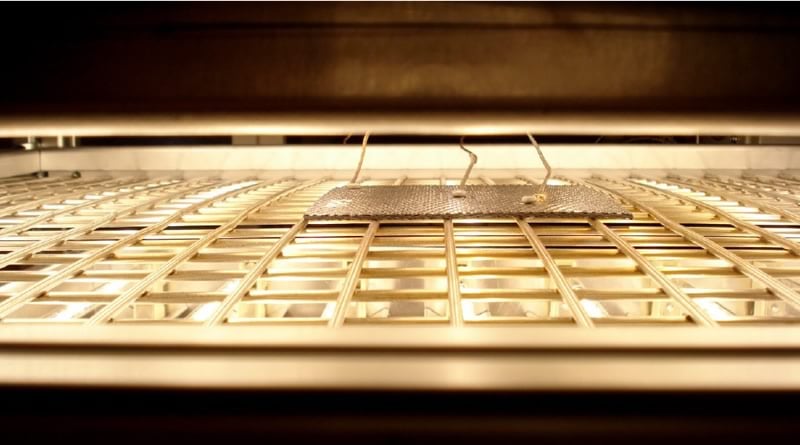
블랙 할로우
맞춤형 가열 플래 튼은 Ceramicx의 2W FFEH 요소의 7 x 800 매트릭스를 통합하여 각 플래 튼 11.2kW의 전력을 제공하도록 설계되었습니다. 이 매트릭스는 510 x 510mm 케이스에 포함되었으며 위에서 설명한 FastIR 시스템과 동일한 프레임에 장착되었습니다. 실험 프로토콜이 사용되었다; 그러나이 플래 튼에는 팬이 사용되지 않았습니다. 이 요소들 사이의 거리는 65mm입니다.
50와 100mm의 두 가지 요소 샘플 거리가 사용되었습니다. 다시, 두 가열 장치 사이의 틈이 열려있었습니다
요소
Ceramicx 블랙 중공 소자는 중장기 영역 (2 – 10μm)에서 피크 파장을 방출합니다. 각 요소의 크기는 245 x 60mm (lxw)입니다. 세라믹 요소와 관련된 더 긴 파장은 많은 폴리머 재료를 가열하는 데 매우 효율적입니다.
측정기 모델
KNUM 열전대는 M3 나사를 사용하여 샘플 표면에 부착되었습니다. 세라믹 시멘트는 시험 되었으나 이것은 재료의 표면에 부착되지 않았다. 고온이 필요한 경우, 사용 가능한 접착제가 안정적으로 유지되지 않으므로 기계적 고정이 필요한 것으로 간주됩니다. 열전대는 그림 10에 표시된 것처럼 각 시편의 중심과 가장자리에서 30mm (가장자리) 및 2mm (분기)에 위치했습니다. 이것은 최대 온도 차이가 기록 될 수 있도록 열전대를 튜브 요소 바로 위와 요소 사이의 중앙에 위치 시켰습니다. 온도 데이터는 1 초 간격으로 기록되었다.
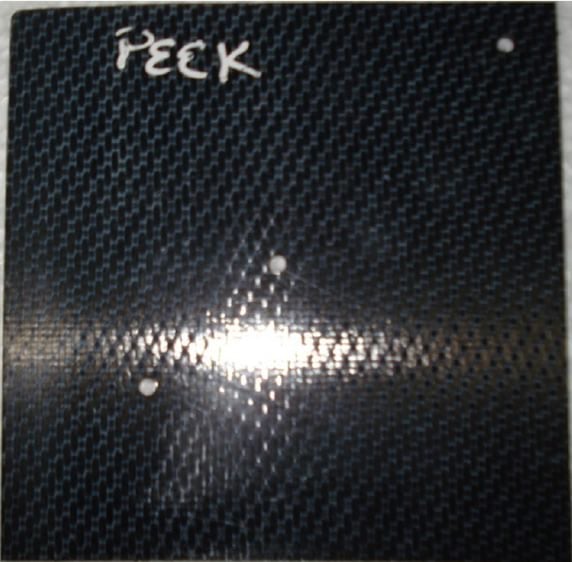
샌드위치 테스트
샌드위치 테스터는 그림 2에 표시된 고급 재료 열 응답 시험기입니다. 다양한 유형의 적외선 히터를 수직 위아래로 향하게 두 위치에 장착 할 수 있습니다. 이를 통해 테스트 된 재료를 상단 및 / 또는 하단에서 가열 할 수 있습니다. 4 개의 비접촉식 광학 고온계를 사용하여 테스트 된 재료의 상단 및 하단 표면 온도를 결정합니다. 이미 터는 그들의 작동 온도까지 예열 될 수 있고,이어서 재료는 미리 결정된 기간 동안 이미 터 (들) 아래로 가져온다. 이 테스트는 샘플 위에 1mm이 장착 된 800kW 텅스텐 (QTM) 및 75W 블랙 중공 요소 (FFEH)를 모두 사용하여 수행되었으며 어떤 히터가 재료를 통해 가장 잘 침투했는지 확인했습니다.
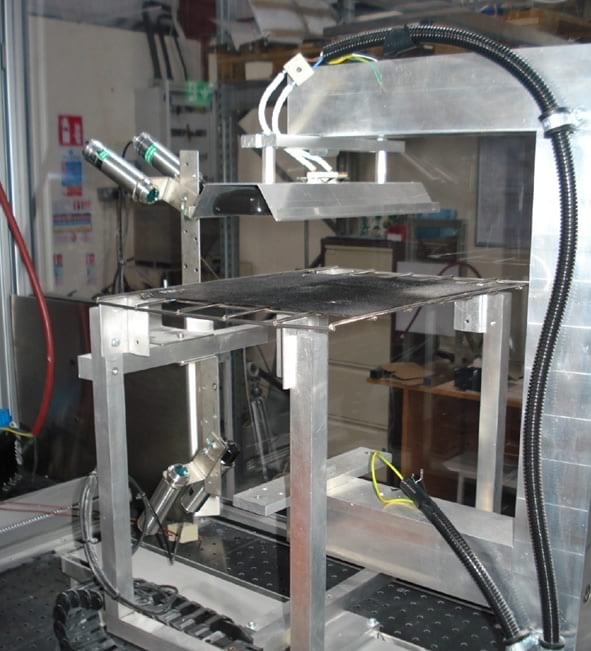
결과
FastIR
이 섹션에서는 해당 세 가지 재료에 대해 텅스텐 및 할로겐 튜브에 대해 찾은 결과를보고합니다. 테스트는 세 가지 히터 높이 (55mm, 80mm 및 95mm)로 수행되었습니다.
몰래 엿보다
초기 시험은 PENUM 샘플과 1500mm로 분리 된 110W 석영 할로겐 튜브가있는 두 개의 FastIR 히터로 수행되었습니다. 그림 4에 표시된이 테스트 결과는 샘플이 필요한 온도에 도달하지 못했음을 나타냅니다.
원소를 2000W 단파 할로겐 (QHL) 튜브로 변경하여 동일한 분리에서 시료가 한 위치에서 필요한 온도에 도달하여 초과하는 것으로 나타났습니다. 이 경우 기록 된 최대 온도는 485 ° C이지만, 상당한 온도 차이 (최대 83 ° C)도 감지되었습니다. 425 ° C의 목표 온도에 도달하는 데 필요한 시간은 99 초입니다. 이것은 두 곳에서만 달성되었습니다
쿼츠 텅스텐 (QTL) 튜브 (2000W)도 히터 거리가 증가함에 따라 최대 온도가 떨어지는 3 가지 레벨에서 검사되었습니다. 55mm에서 520 ° C의 최대 및 최소 온도가 감지되었습니다. 재료 샘플 전체의 목표 온도는 206 초 내에 달성되었습니다. 80mm까지 거리를 늘리면 450 ° C 및 415 ° C로 감소하고 샘플 위의 95mm에서 샘플의 최대 및 최소 온도는 407 및 393 ° C입니다.
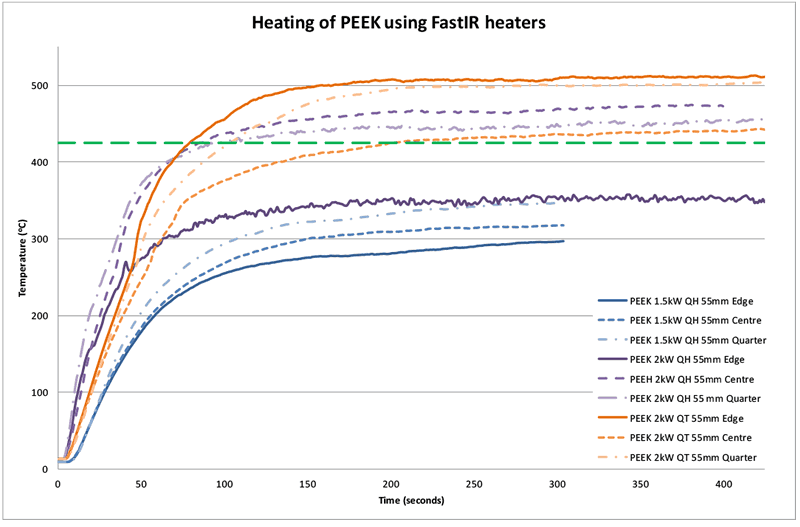
그림 4는 샘플과 히터의 근접성 및 425 ° C로 재료를 가열하는 데 필요한 시간 (206kW QT 히터의 경우 2 초)으로 인해 샘플에서 발생할 수있는 온도의 변화를 보여줍니다.
150 ° W 텅스텐 튜브는 사용 된 요소의 전력을 감소시키는 것보다 히터 거리를 증가시키는 것이 작동 상 더 중요하다고 간주되어 테스트되지 않았습니다.
그림 5는 가열 전후의 샘플의 시각적 차이를 보여줍니다.
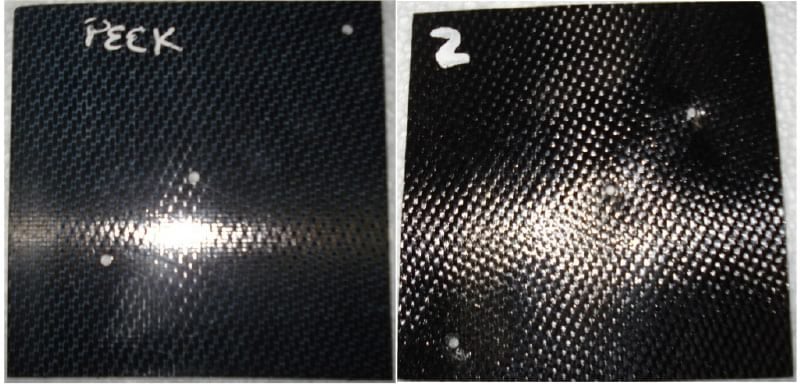
PEKK
PEKK는 2000mm에서만 55W 텅스텐 히터로 가열되었습니다. 물질의 열 반응은 500 ℃를 초과하는 온도가 기록 될 때 우수했다. 기록 된 최대 온도가 102 ° C를 초과하여 최소 규정 된 온도가 500 초 내에 달성되었습니다.
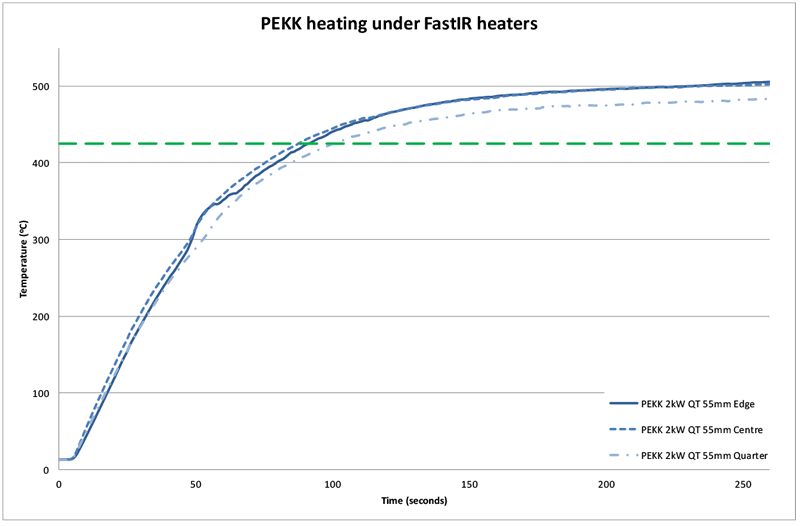
이 샘플은 그림 7와 같이 가열 후 가장자리에서 약간의 분리 및 박리와 표면 왜곡이 발생하는 것으로 나타났습니다. 저장 중 수분 흡수 및 발생한 빠른 가열 때문일 수 있습니다.
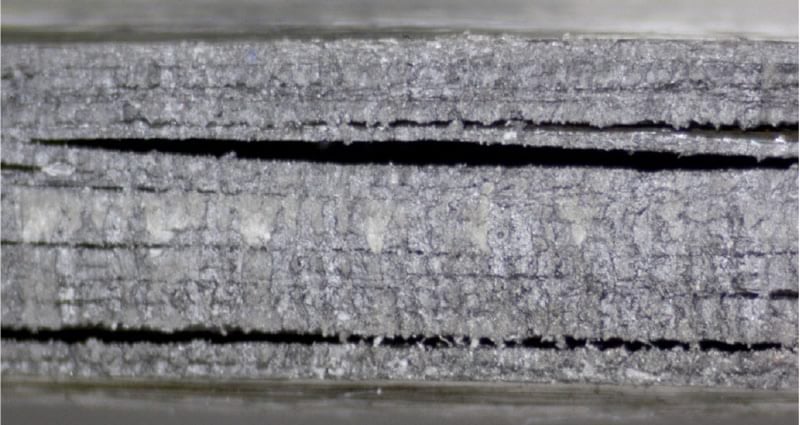
PPS
PPS 재료는 2000W 할로겐 및 텅스텐 히터로 테스트되었습니다. 할로겐 테스트는 55mm의 분리와 텅스텐 테스트는 55mm 및 95mm에서 수행되었습니다.
데이터는 텅스텐 튜브가 55mm 분리에서 더 높은 온도가 기록되고 샘플 전체의 온도 균일 성이 더 높아져 할로겐 튜브보다이 재료에 대해 더 나은 히터라는 것을 보여주었습니다. 할로겐 히터의 경우 38 ° C와 텅스텐 히터의 경우 30 ° C의 변형이 기록되었습니다. 이 기록 된 변화는 튜브에 대한 열전대의 위치에 크게 영향을받습니다. 동일한 열전대 위치는 보장되지 않습니다.
시료에서 유황 냄새가 나는 가스가 방출되어 재료가 425 ° C의 필요한 온도에 도달 한 직후 PPS 테스트가 종료되었습니다.
55mm의 거리에서, 66mm에서 할로겐 및 텅스텐 히터에 대해 88 및 55 초 후에 목표 온도가 각각 기록되었다. 텅스텐 히터가 샘플로부터 95mm에 장착되었을 때, 목표 온도는 달성되지 않았다.
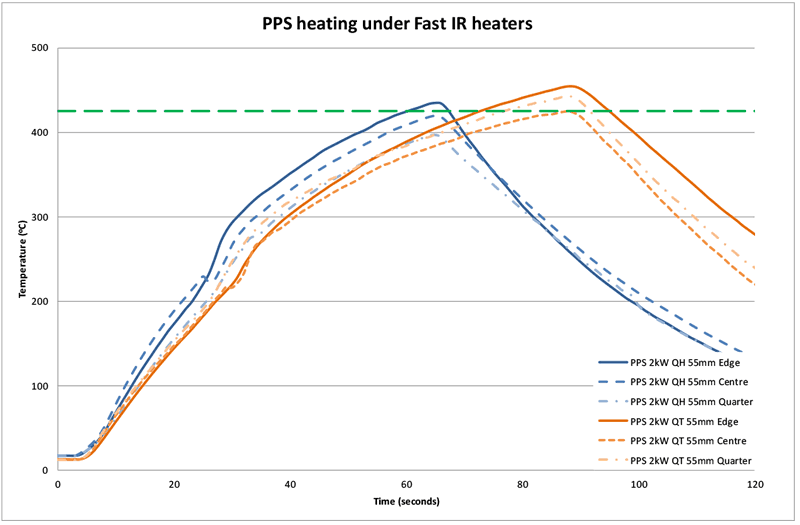
블랙 할로우
초기 테스트는 50mm의 요소 재료 분리로 수행되었습니다. 재료의 온도 상승은 모든 재료에 대해 매우 빠르다. 콜드 스타트부터 중공 형 요소는 약 10-12 분 동안 일정한 작동 수준 (표면 온도 약 700 ° C)으로 가열됩니다. 재료 온도 증가는 히터의 가열 곡선과 대체로 비슷하지만 시간 지연이있었습니다.
몰래 엿보다
필요한 처리 온도에 도달하기 위해 PEEK 샘플을 가열하는 데 걸리는 시간의 도표는 아래 그림 9에 표시되어 있습니다. 이것은 425 ° C까지 가열 시간이 히터가 185mm에서 켜질 때부터 대략 50 초임을 나타냅니다. 거리가 100mm로 증가하면 시간은 230 초로 증가합니다. 가열 중에 샘플을 두 플래 튼 사이에두고 냉각을 위해 제거 하였다.
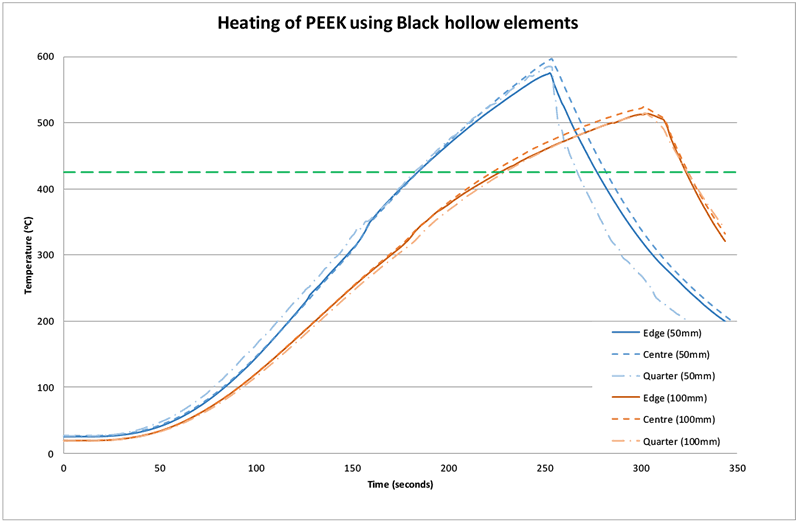
PEKK
PEKK가 최소 임계 값에 도달하는 데 걸리는 시간은 PEEK보다 약간 길었습니다. 이에 대한 두 가지 가능한 이유가 있습니다 : 1.) 재료는 적외선과 PEEK 및 2를 흡수하지 않습니다.) 재료의 두께는 두 배 (각각 1 및 2mm)입니다. 425mm에서 50 ° C에 도달하는 데 필요한 시간은 181 초이고 100mm에서 244 초로 증가했습니다.
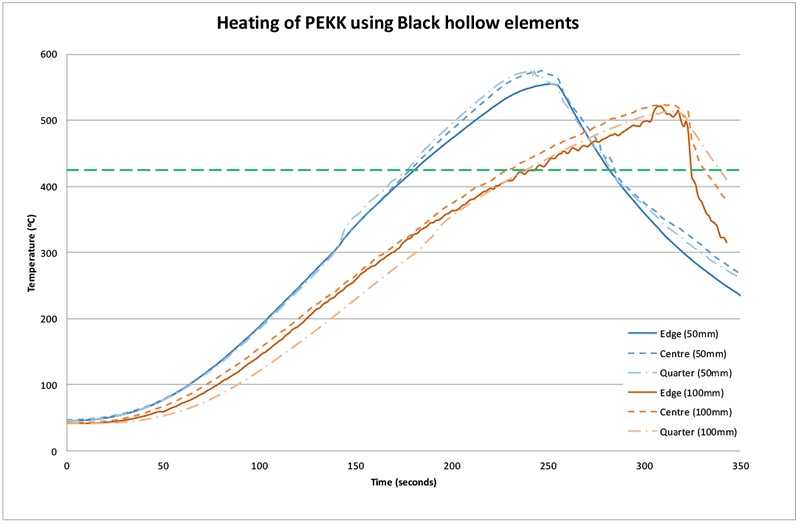
PPS
425 ° C가 171 초 및 219 초로 50 및 100mm로 각각 기록 된 검은 색 중공 요소로 PPS가 매우 성공적으로 가열되었습니다. 이 물질의 가열 곡선은 그림 11에 나와 있습니다. 다시, 유황 냄새가 나는 연기가 발생 하였지만, 이것의 양은 상기 한 바와 같이 할로겐 히터만큼 많지 않았다. 이것은 부분적으로 가열판 뒷면에 팬이 없기 때문일 수 있습니다.
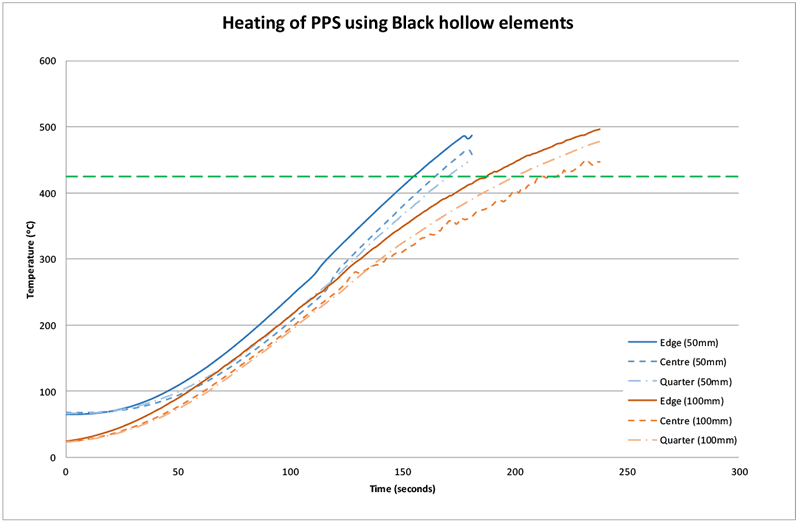
할로겐, 텅스텐 및 중공 세라믹 요소를 사용하여 재료를 목표 온도로 가열하는 데 필요한 시간을 요약하면 아래 표 1에 나와 있습니다. 55mm보다 먼 거리에 할로겐 요소를 장착하는 것이 보편적으로 성공하지 못했기 때문에 이러한 결과는 표에서 생략되었습니다.
자재 |
히터 종류 (전원)
|
거리 | 425 ° C에 도달하는 시간 |
---|---|---|---|
몰래 엿보다 | QHL (2kW) | 55mm | 99 |
QTL (2kW) | 55mm | 206 | |
FFEH (800W) | 50mm | 185 | |
FFEH (800W) | 100mm | 230 | |
PEKK | QTL (2kW) | 55mm | 102 |
FFEH (800W) | 50mm | 181 | |
FFEH (800W) | 100mm | 244 | |
PPS | QHL (2kW) | 55mm | 66 |
QTL (2kW) | 55mm | 88 | |
FFEH (800W) | 50mm | 171 | |
FFEH (800W) | 100mm | 219 |
샌드위치 테스트
재료를 통한 열 전달에 대한 정보를 얻기 위해 샌드위치 테스트를 수행했습니다. 이것은 한쪽면에서 시료를 가열하고 양쪽면의 온도를 측정하고 결과를 비교하여 수행되었습니다. FastIR 결과에 기초하여 텅스텐 튜브 및 흑색 중공 요소 만 조사되었으며, 단파 할로겐 튜브는 해당 재료에 적합한 히터가 아니다.
QTM 요소의 결과는 PEEK와 PPS 재료의 상단과 하단 표면 사이에 온도 차이가 크지 않다는 것을 보여 주지만 PPS는 더 빨리 가열되며이 재료의 곡선은 거의 구분할 수 없습니다. 이 두 재료는 매우 얇습니다 (≈ 1mm). 예상대로 PEKK의 온도 차이는 두께 (≈ 75mm)로 인해 더 컸습니다 (2 ± 2oC). 이 결과는 아래 그림 12에 나와 있습니다.
작동상의 이유로 고온계에서 300 ° C의 온도가 감지되면 테스트가 종료됩니다. 테스트의 첫 30 초에 나타나는 피크는 반사율이며 실제 온도 판독 값이 아닙니다.
이 결과는 텅스텐 타입 히터를 사용하여 PEEK 및 PPS에 대해 재료의 우수한 IR 침투가 가능함을 보여줍니다. 그러나 PEKK의 온도 균등화는 좋지 않습니다. test75의 마지막 18 초에서 거의 4 ° C의 온도 차이로 나타납니다.
고온계가 재료가 판독 값을 왜곡하는 것을 보는 데 필요한 예각으로 어떤 영향을 미치는지 분석하기 위해 재료 샘플을 히터에 더 가깝게 이동할 수 없었습니다.
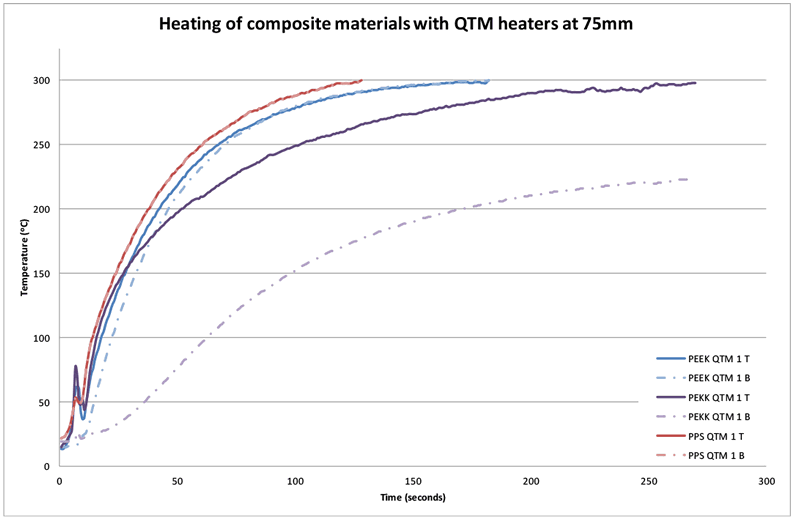
동일한 거리 (75mm)에서 검은 색 중공 요소로 시료를 가열하면 더 두꺼운 PEKK 재료 (얇은 재료와 비교)에서 더 큰 온도 차이 (45 ± 2 ° C)가 관찰되는 유사한 경향이 나타납니다. PEEK의 상단과 하단 표면의 온도는 거의 구별 할 수 없습니다. 그러나 PPS 온도 (25 ± 2 ° C)에는 차이가 있습니다. 이 데이터는 그림 13에 표시됩니다. 이는 파장이 긴 PPS의 IR 투과율이 텅스텐 IR보다 짧지 않지만 PEKK의 온도 평형화가 더 좋지만 (이상적이지는 않음) 나타냅니다.
75mm 분리시, 이전 플래 튼 결과와 모순되는 텅스텐 히터를 사용하여 최고 온도와 가열 속도를 얻습니다. 그러나 단 하나의 히터 만 사용되었으므로 가이드로 사용해서는 안됩니다. 또한, 단일 히터가 아닌 여러 히터를 사용하여 이러한 특성을 향상시킬 수 있습니다.
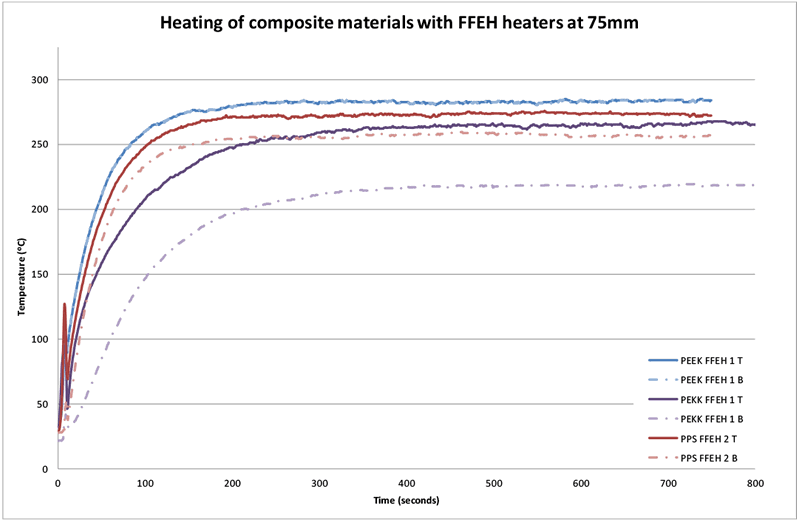
결론
- 상기에서 수행되고 상술 된 시험은 3 개의 열가소성 탄소 복합 재료를 최소 425 ℃로 가열하는 것이 중파 할로겐 및 흑색 중공 요소 모두에서 가능하다는 것을 나타낸다.
- Ceramicx 800W 블랙 중공 요소 (FFEH)를 사용하여 더 높은 최대 온도를 달성 할 수 있습니다.
- PEEK를 425 ° C로 가열하는 데 필요한 시간은 206mm에서 2kW 텅스텐 튜브 히터의 경우 55 초이고 230mm의 FFEH 요소의 경우 100 초입니다.
- PEKK를 425 ° C로 가열하는 데 필요한 시간은 102mm의 2kW 텅스텐 튜브 히터의 경우 55 초이고 244mm의 FFEH 요소의 경우 100 초입니다.
- 425 ° C로 PPS를 가열하는 데 필요한 시간은 88mm에서 2kW 텅스텐 튜브 히터의 경우 55 초이고 219mm에서 FFEH 요소의 경우 100 초입니다.
- 최대 온도, 달성 가능한 재료 가열 속도 및 표면 온도 균일 성은 히터가 재료로부터 장착되는 거리의 강력한 기능입니다.
- PPS 및 PEEK의 재료 두께를 통한 탁월한 IR 침투 및 온도 균일화는 중파 할로겐 (텅스텐)으로 달성되었습니다. PEKK로 달성 한 온도 균등화는 다른 재료만큼 좋지 않았습니다.
- 검은 중공 요소를 사용하여 PEEK에서 우수한 IR 침투 및 온도 균일화를 볼 수있었습니다. 이 속성은 PEKK 및 PPS만큼 좋지 않았습니다.
위의 테스트 데이터와 문제의 재료를 형성하는 데 필요한 온도를 달성하는 데 필요한 근접 요소-재료 분리를 기반으로, 최고의 적외선 이미 터는 Ceramicx 800W 검정 완전 평면 중공 요소입니다. 필요한 온도를 달성하는 데 걸리는 시간이 텅스텐 히터보다 약간 길지만, 사용 된 요소가 근접하면 표면 온도 균일 성이 향상됩니다. 또한, 세라믹 요소는 실온에서 시작되었으며 작동 수준에 도달하려면 약 12 분이 필요했습니다. 따라서 요소를 예열하면이 시간이 크게 단축 될 수 있습니다.
이 결과는 테스트에 사용 가능한 샘플 (즉, 1mm 및 2mm 두께)을 기반으로합니다. 더 두꺼운 부품의 가열은 재료 두께에 걸친 온도 프로파일이 균일하고 후속 성형 작업에 적합하도록 보장하기 위해 가열 기술의 상당한 변화를 조사해야 할 수도 있습니다.
1 폴리 에테르 에테르 케톤
2 폴리 페닐 렌 설파이드
3 폴리 에테르 케톤
4 테스트의 마지막 18 초 동안 취한 상단과 하단 표면의 평균 차이.
책임 부인
이러한 시험 결과는 특정 유형의 적외선 방출기가 사용되기 전에 신중하게 고려해야합니다.
다른 회사에서 실시한 반복 테스트에서도 같은 결과를 얻지 못할 수 있습니다. 실험 조건의 차이로 인해 결과가 달라질 수 있습니다. 다른 오류 원인으로는 사용 된 이미 터 브랜드, 이미 터의 효율, 공급 전력, 테스트 된 재료에서 사용 된 이미 터까지의 거리 및 환경이 있습니다. 온도가 측정되는 위치에 따라 결과가 달라질 수 있습니다.