AUTOR | DATA UTWORZENIA | WERSJA | NUMER DOKUMENTU |
---|---|---|---|
Dr Peter Marshall | 8 kwietnia 2016 | V1.1 | CC11 - 00101 |
Wprowadzenie
Firma CCP Gransden zwróciła się do Ceramicx o zbudowanie pieca na podczerwień do podgrzewania termoplastycznych materiałów prepregu z włókna węglowego do operacji formowania. Te prace testowe zostały przeprowadzone w ramach funkcji określonych w ofercie sprzedaży (CSP 000 008). Faza pierwsza obejmuje ocenę i wybór promiennika podczerwieni do tego projektu, przy założonej minimalnej temperaturze materiału wynoszącej 425 ° C.
Opis materiału
Otrzymano trzy próbki dwóch materiałów w kawałkach 230 x 230 x 1mm. W tych przypadkach matrycą był PEEK1 i PPS2. Mniejsza próbka PEKK3 o wymiarach 200 x 150 x 2mm. Materiał był sztywny, gładki z błyszczącym czarnym wykończeniem. Na powierzchni próbek PEEK i PPS widoczny był mały wzór.
Próbki PEEK i PPS pocięto na kawałki 115 x 115 mm. Materiał PEKK pocięto na kawałki 100 x 75mm.
Metoda wykonania
Oceniono dwie różne rodziny grzejników; halogen (QH i QT) i czarna pusta ceramika (FFEH). W każdym przypadku płyty przymocowano powyżej i poniżej próbki materiału o regulowanej wysokości.
FastIR
System montażowy został wyprodukowany, aby umożliwić montaż dwóch jednostek FastIR 500 firmy Ceramicx nad i pod materiałem. FastIR 500 składa się z siedmiu elementów grzejnych zamontowanych równolegle w obudowie 500 x 500 mm. Odstęp między tymi rurkami wynosi 81mm. Zastosowano elementy 1500W i 2000W „long” (długość całkowita: 473mm), dające całkowitą moc wyjściową odpowiednio z dwóch jednostek 21 lub 28kW. Jednostki grzejne zostały zamontowane w taki sposób, że odległość między powierzchnią elementu a próbką zmieniała się między 55mm i 95mm.
Zastosowano następujący protokół eksperymentalny:
- Wentylatory włączone
- Włączone trzy centralne elementy grzejne, góra i dół
- Na zewnątrz włączone są cztery elementy grzejne, góra i dół
Obraz próbki między dwiema jednostkami FastIR pokazano na rysunku 1. Nic nie użyto do zamknięcia szczeliny między dwiema jednostkami grzewczymi
Elementy
W module FastIR można zamontować dwa rodzaje elementów; halogen kwarcowy i wolfram kwarcowy. Elementy te emitują różne szczytowe długości fal podczerwonych; halogen w przybliżeniu 1.0 - 1.2μm i wolfram między 1.6 - 1.9μm. Każda rura ma średnicę 10mm, całkowitą długość 473mm i podgrzewaną długość 415mm.
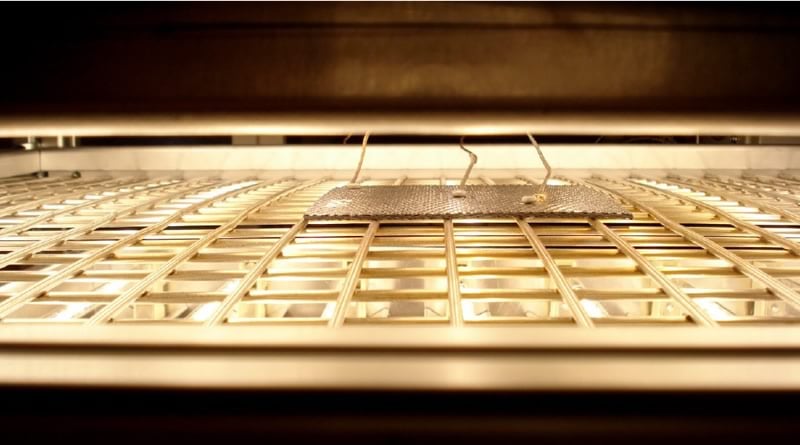
Czarna dziura
Specjalna płyta grzewcza została zaprojektowana tak, aby zawierała matrycę 2 x 7 elementów 800W FFEH firmy Ceramicx, co daje każdej płycie 11.2kW moc. Matryca została zamknięta w obudowie 510 x 510mm i zamontowana w tej samej ramie, co opisany powyżej system FastIR. Zastosowano protokół eksperymentalny; jednak w tych płytach nie zatrudniono fanów. Odległość między tymi elementami wynosiła 65mm.
Zastosowano dwie różne odległości element-próbka, 50 i 100mm. Ponownie przerwa między dwiema jednostkami grzewczymi pozostała otwarta
Elementy
Czarne puste w środku elementy Ceramicx emitują szczytowe długości fal w średnim i długim reżimie (2 - 10μm). Każdy element ma wymiary 245 x 60mm (dł. X szer.). Dłuższe fale związane z elementami ceramicznymi są bardzo wydajne do ogrzewania wielu materiałów polimerowych.
Oprzyrządowanie
Termopary typu K zostały przymocowane do powierzchni próbki za pomocą śrub M3. Wypróbowano cement ceramiczny, jednak nie przylegał on do powierzchni materiału. Biorąc pod uwagę wymagane wysokie temperatury, żaden dostępny klej nie byłby stabilny, dlatego konieczne było mechaniczne zamocowanie. Termopary umieszczono w środku każdej próbki, a także 10mm (krawędź) i 30mm (ćwiartka) od krawędzi, jak pokazano na rycinie 2. Umożliwiło to umiejscowienie termopar bezpośrednio nad elementami rurowymi i pośrodku między elementami, dzięki czemu zarejestrowana zostanie maksymalna różnica temperatur. Dane dotyczące temperatury rejestrowano w odstępach jednosekundowych.
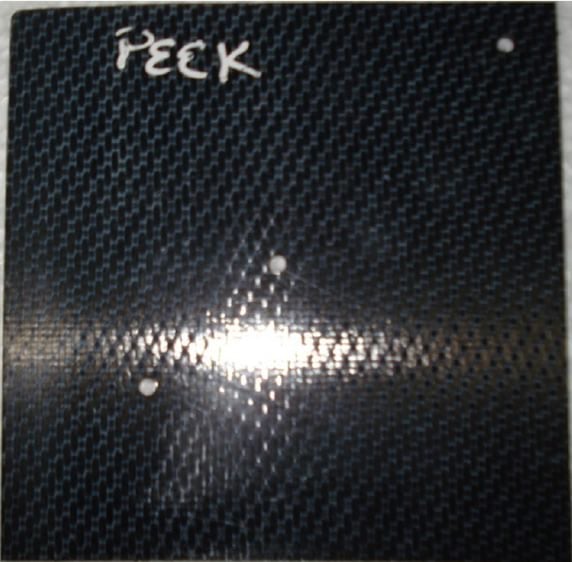
Testy kanapkowe
Tester warstwowy jest zaawansowaną maszyną do testowania reakcji termicznej materiału, jak pokazano na rysunku 2. Różne typy promienników podczerwieni mogą być montowane w dwóch pozycjach, skierowane pionowo w górę i w dół. Zapewnia to, że badany materiał może być ogrzewany od góry i / lub od dołu. Cztery bezkontaktowe pirometry optyczne służą do określenia temperatury górnej i dolnej powierzchni badanego materiału. Emitery pozostawia się do ogrzania do ich temperatury roboczej, a następnie materiał wprowadza się pod emiter (emiter) na określony czas. Ten test został przeprowadzony zarówno z wolframem 1kW (QTM), jak i czarnymi pustymi elementami 800W (FFEH) zamontowanymi 75mm nad próbką, aby ustalić, który podgrzewacz zapewnia najlepszą penetrację przez materiał.
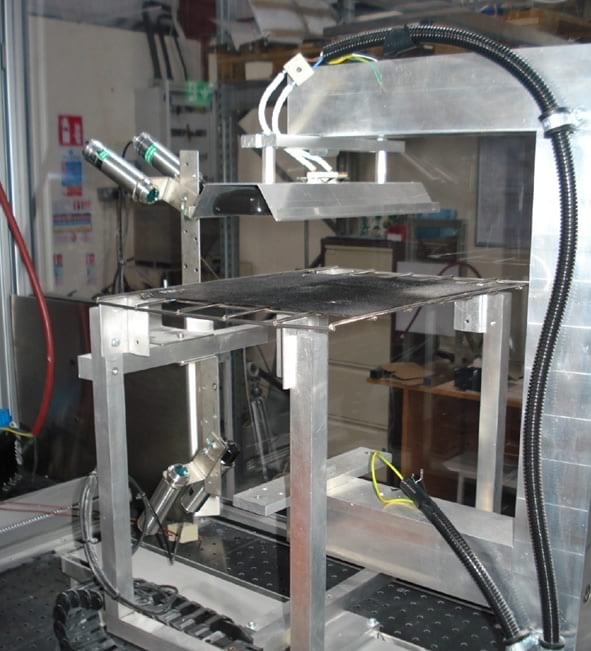
Efekt
FastIR
W tej sekcji przedstawiono wyniki znalezione dla rur wolframowych i halogenowych dla trzech omawianych materiałów. Testy przeprowadzono z trzema różnymi wysokościami grzejników (55 mm, 80 mm i 95 mm).
PEEK
Wstępne próby przeprowadzono na próbce PEEK i dwóch grzejnikach FastIR z kwarcowymi lampami halogenowymi 1500W oddzielonymi 110mm. Wyniki tego testu, pokazane na rysunku 4, wskazują, że próbka nie osiągnęła wymaganej temperatury.
Elementy zmieniono na lampy halogenowe krótkofalowe 2000W (QHL), które wykazały, że przy tym samym rozdzieleniu próbka osiągnęła i przekroczyła wymaganą temperaturę w jednym miejscu. W tym przypadku maksymalna zarejestrowana temperatura wynosiła 485 ° C, jednak wykryto również znaczące różnice temperatur (do 83 ° C). Czas wymagany do osiągnięcia temperatury docelowej 425 ° C wynosił 99 sekund. Osiągnięto to tylko w dwóch lokalizacjach
Rurki kwarcowe wolframowe (QTL) (2000W) zostały również zbadane na trzech poziomach z maksymalnym spadkiem temperatury wraz ze wzrostem odległości grzejnika. Przy 55mm wykryto maksymalną i minimalną temperaturę 520 ° C. Temperatura docelowa w próbce materiału została osiągnięta w 206 sekundach. Zwiększając odległość do 80mm, zredukowano je do 450 ° C i 415 ° C, a przy 95mm powyżej próbki maksymalne i minimalne temperatury próbki wynosiły 407 i 393 ° C.
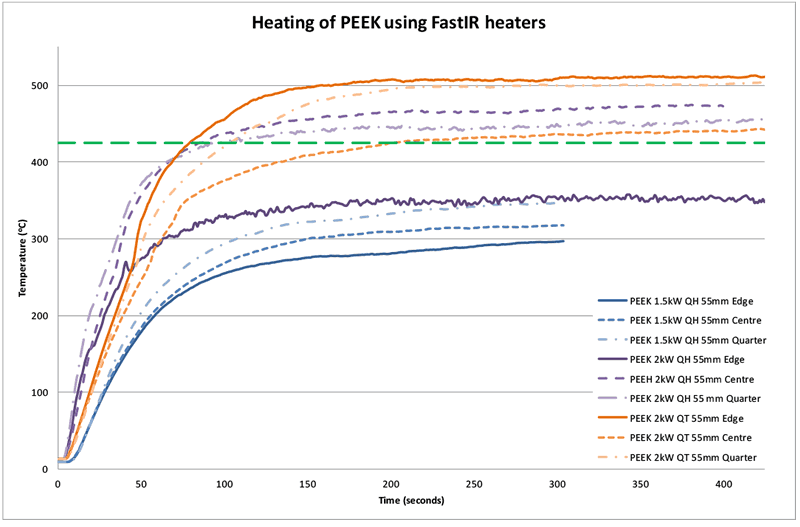
Rysunek 4 pokazuje odchylenie temperatury, które może wystąpić w próbce ze względu na bliskie sąsiedztwo grzejników z próbką, a także czas potrzebny do podgrzania materiału do 425 ° C (206 sekund dla grzałki 2kW QT).
Rurki wolframowe 150 ° W nie były testowane, ponieważ uznano za ważniejsze z operacyjnego punktu widzenia zwiększenie odległości nagrzewnicy niż zmniejszenie mocy zastosowanych elementów.
Rysunek 5 pokazuje różnicę wizualną w próbce przed i po ogrzewaniu.
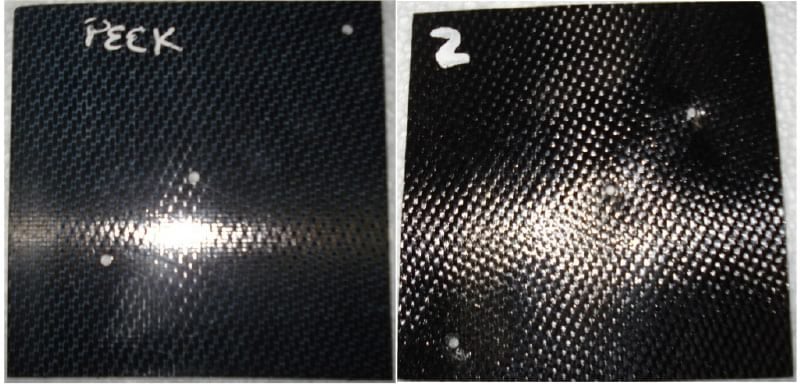
PEKK
PEKK ogrzewano za pomocą grzejników wolframowych 2000W tylko przy 55mm. Reakcja termiczna materiału była doskonała przy rejestrowanych temperaturach przekraczających 500 ° C. Minimalną wymaganą temperaturę osiągnięto w ciągu 102 sekund, a maksymalna zarejestrowana temperatura przekraczała 500 ° C.
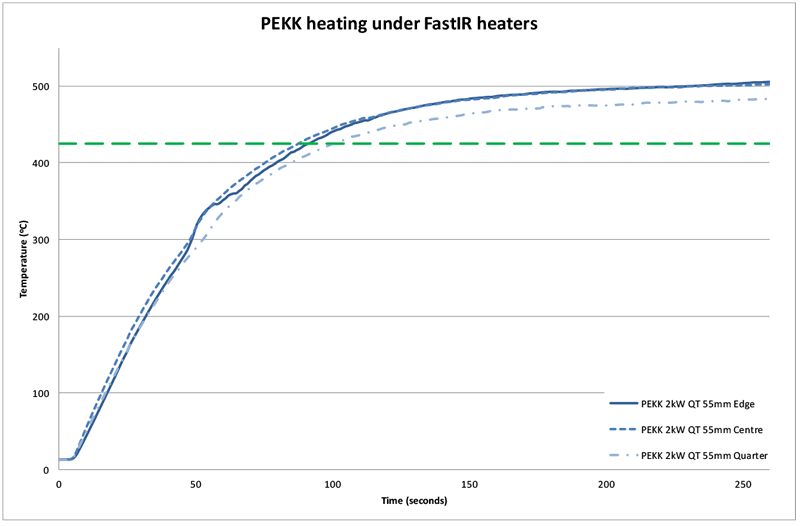
Zauważalne było, że próbka ta wykazywała pewne pękanie i rozwarstwienie na krawędziach, a także pewne zniekształcenia powierzchni po ogrzewaniu, jak pokazano na rysunku 7, prawdopodobnie z powodu absorpcji wilgoci podczas przechowywania i szybkiego nagrzewania, które miało miejsce.
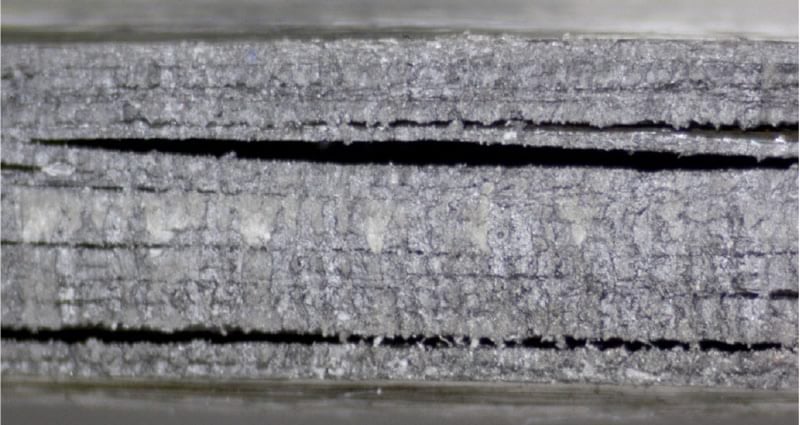
PPS
Materiał PPS został przetestowany za pomocą halogenowych i wolframowych grzejników 2000W. Test halogenowy przeprowadzono z rozdziałem 55mm, a test wolframu w 55mm i 95mm.
Dane ponownie pokazały, że rura wolframowa była lepszym ogrzewaczem dla tego materiału (niż grzejnik halogenowy), przy wyższych temperaturach rejestrowanych przy rozdzieleniu 55mm, a także większej jednolitości temperatury w próbce. Zmienność 38 ° C zarejestrowano dla grzejników halogenowych i 30 ° C dla grzejników wolframowych. Na tę zarejestrowaną zmienność duży wpływ będzie miało położenie termopary względem rur. Nie można zagwarantować identycznych lokalizacji termopar.
Testy z PPS zakończono wkrótce po osiągnięciu przez materiał wymaganej temperatury 425 ° C, ponieważ z próbek uwolniono opary zapachowe siarki.
W odległości 55mm temperatura docelowa została zarejestrowana po 66 i 88 sekundach odpowiednio dla grzejników halogenowych i wolframowych przy 55mm. Gdy grzejniki wolframowe zostały zamontowane na 95mm od próbki, temperatura docelowa nie została osiągnięta.
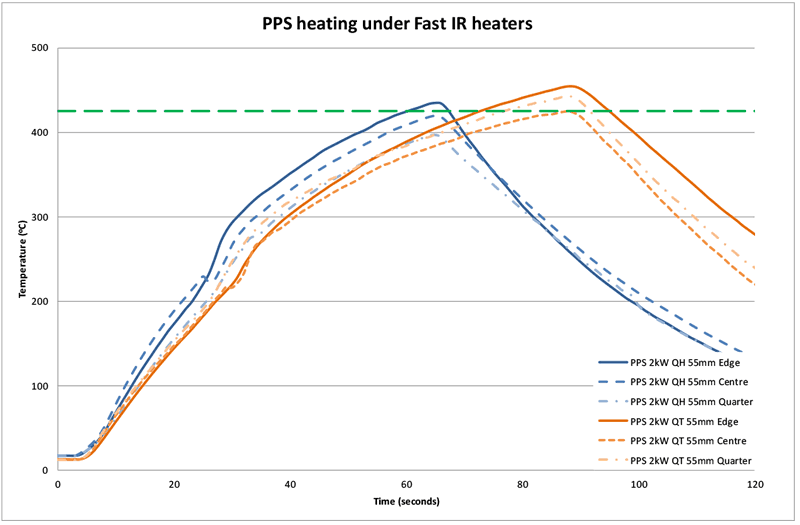
Czarna dziura
Wstępne testy przeprowadzono przy oddzieleniu elementu od materiału 50mm. Wzrost temperatury materiału był bardzo szybki dla wszystkich materiałów. Od zimnego startu puste elementy potrzebują około 10-12 minut na ogrzanie do stabilnego poziomu operacyjnego (temperatura powierzchni około 700 ° C). Wzrost temperatury materiału był zasadniczo podobny do krzywej grzewczej grzejnika, jednak było w tym opóźnienie.
PEEK
Wykres czasu potrzebnego do podgrzania próbki PEEK do osiągnięcia wymaganej temperatury przetwarzania pokazano poniżej na rysunku 9. To pokazuje, że czas nagrzewania do 425 ° C wynosi około 185 sekund od momentu włączenia grzałek przy 50mm. Jeśli odległość zostanie zwiększona do 100 mm, czas zostanie zwiększony do 230 sekund. Próbkę pozostawiano między dwiema płytami podczas podgrzewania i usuwano do chłodzenia.
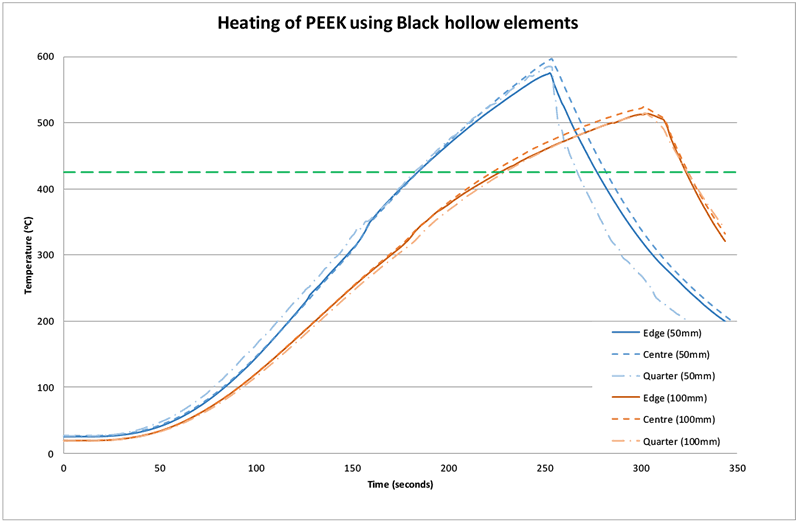
PEKK
Czas, w którym PEKK osiągnął próg minimalny, był nieco dłuższy niż w przypadku PEEK. Istnieją dwa możliwe powody: 1.) Materiał nie absorbuje promieniowania podczerwonego, a także PEEK i 2.) Grubość materiału jest dwukrotnie większa (odpowiednio 1 i 2mm). Czas wymagany do osiągnięcia 425 ° C przy 50mm wynosił 181 sekund, a przy 100mm wydłużył się do 244 sekund
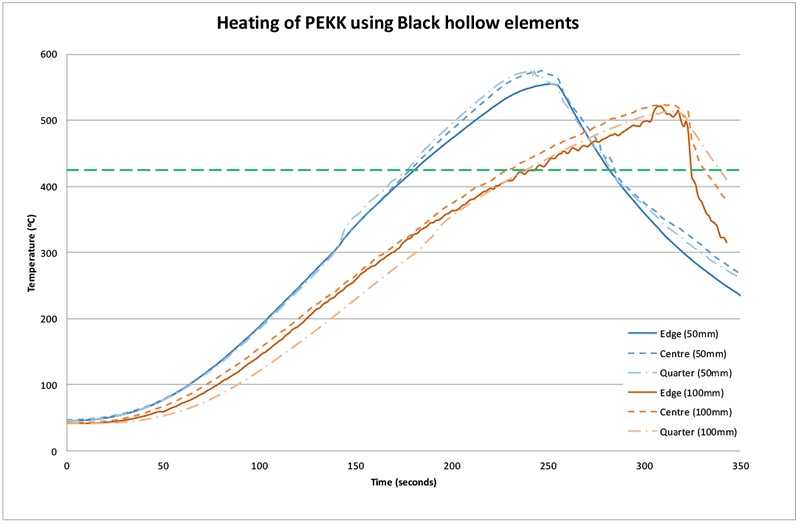
PPS
PPS nagrzewa się bardzo skutecznie, a czarne puste elementy z 425 ° C są rejestrowane w 171 sekundach i 219 sekundach odpowiednio w 50 i 100mm. Krzywa grzewcza tego materiału pokazano na rysunku 11. Ponownie nastąpiło uwolnienie dymu siarkowego, jednak jego ilość nie była tak duża jak w przypadku grzejników halogenowych, jak opisano powyżej. Może to częściowo wynikać z braku wentylatorów z tyłu płyty grzewczej.
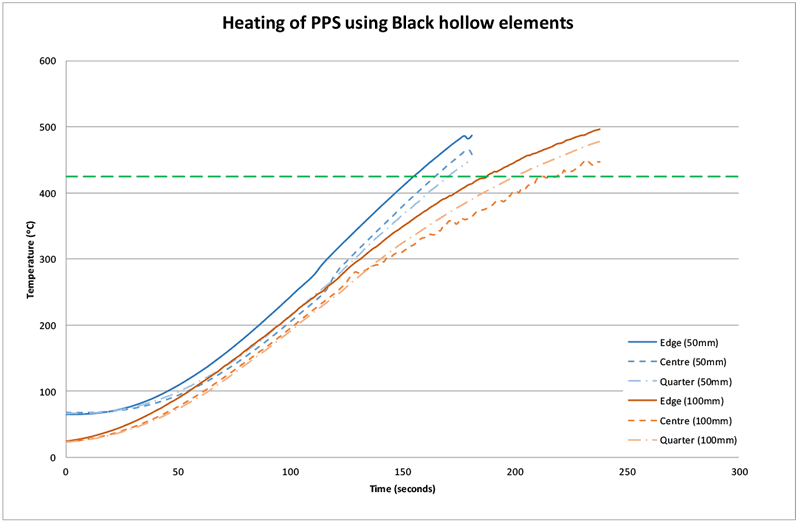
Podsumowanie czasów potrzebnych do ogrzania materiałów z halogenami, wolframem i pustymi elementami ceramicznymi do temperatury docelowej pokazano poniżej w tabeli 1. Ponieważ montaż elementów halogenowych na większych odległościach niż 55mm nie był ogólnie udany, wyniki te zostały pominięte w tabeli.
Materiał |
Typ grzałki (moc)
|
Dystans | Czas do osiągnięcia 425 ° C |
---|---|---|---|
PEEK | QHL (2kW) | 55mm | 99 |
QTL (2kW) | 55mm | 206 | |
FFEH (800 W) | 50mm | 185 | |
FFEH (800 W) | 100mm | 230 | |
PEKK | QTL (2kW) | 55mm | 102 |
FFEH (800 W) | 50mm | 181 | |
FFEH (800 W) | 100mm | 244 | |
PPS | QHL (2kW) | 55mm | 66 |
QTL (2kW) | 55mm | 88 | |
FFEH (800 W) | 50mm | 171 | |
FFEH (800 W) | 100mm | 219 |
Testy kanapkowe
Testy kanapkowe przeprowadzono w celu uzyskania informacji o przenoszeniu ciepła przez materiał. Dokonano tego poprzez podgrzanie próbki z jednej strony, pomiar temperatury po obu stronach i porównanie wyników. Przebadano tylko rury wolframowe i czarne puste elementy, ponieważ w oparciu o wyniki FastIR, krótkofalowe lampy halogenowe nie są odpowiednimi grzejnikami dla przedmiotowych materiałów.
Wyniki dla elementów QTM pokazują, że nie ma znaczącej różnicy temperatur między górną i dolną powierzchnią dla materiałów PEEK i PPS, jednak PPS nagrzewa się szybciej, a krzywe dla tego materiału są praktycznie nie do odróżnienia. Należy zauważyć, że te dwa materiały są bardzo cienkie (≈ 1mm). Zgodnie z oczekiwaniami różnica temperatur dla PEKK była większa (75 ± 2oC) ze względu na jego grubość (≈ 2mm). Wyniki te pokazano na rysunku 12 poniżej.
Z przyczyn operacyjnych test kończy się, gdy pirometry wykrywają temperaturę 300 ° C. Szczyt widoczny w pierwszych 30 sekundach testu to współczynnik odbicia i nie jest prawdziwym odczytem temperatury.
Te wyniki pokazują, że dobra penetracja IR materiału jest możliwa dla PEEK i PPS przy użyciu grzejnika wolframowego. Jednak wyrównanie temperatury dla PEKK nie jest tak dobre, o czym świadczy prawie 75 ° C różnica temperatur w ostatnich 18 sekundach testu 4.
Nie było możliwe przesunięcie próbek materiału bliżej grzejnika, aby przeanalizować, jaki to miałoby skutek, ponieważ kąt ostry wymagany do pirometru, aby zobaczyć materiał zniekształciłby odczyt.
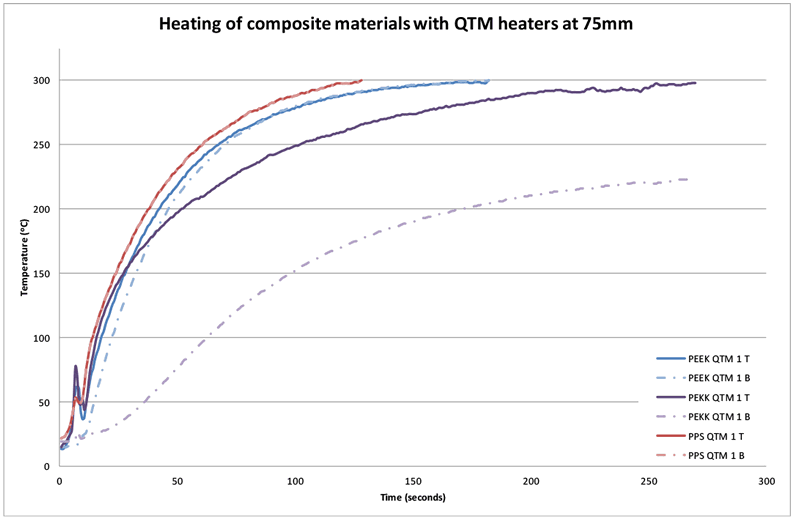
Podgrzewanie próbek czarnymi pustymi elementami w tej samej odległości (75mm) wykazuje podobny trend z większą różnicą temperatur (45 ± 2 ° C) obserwowaną dla grubszego materiału PEKK (w porównaniu z cieńszymi materiałami). Temperatury górnej i dolnej powierzchni PEEK są praktycznie nie do odróżnienia; istnieje jednak różnica w temperaturze PPS (25 ± 2 ° C). Te dane pokazano na rysunku 13. Wskazuje to, że penetracja IR PPS promieniowaniem o większej długości fali nie jest tak dobra, jak w przypadku krótszego IR wolframu, jednak wyrównanie temperatury PEKK jest lepsze (ale nie idealne).
Przy separacji 75mm najwyższe temperatury i szybkości ogrzewania uzyskuje się za pomocą grzejnika wolframowego, który wydaje się zaprzeczać poprzednim wynikom płyty. Nie należy tego jednak traktować jako wskazówki, ponieważ zastosowano tylko jeden grzejnik. Ponadto właściwości te zostaną poprawione poprzez zastosowanie szeregu grzejników w przeciwieństwie do pojedynczego grzejnika.
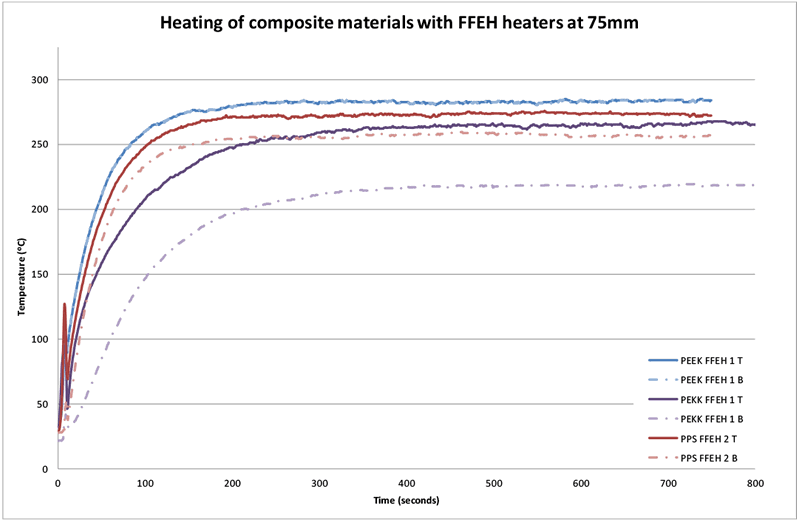
Wnioski
- Przeprowadzone i szczegółowo opisane powyżej testy wskazują, że ogrzewanie trzech termoplastycznych materiałów kompozytowych węglowych do minimum 425 ° C jest możliwe zarówno z halogenami o średniej fali, jak i czarnymi pustymi elementami.
- Wyższe maksymalne temperatury można osiągnąć za pomocą czarnego pustego elementu Ceramicx 800W (FFEH).
- Czas wymagany do podgrzania PEEK do 425 ° C wynosił 206 sekund dla grzejników wolframowych 2kW przy 55mm i 230 sekund dla elementów FFEH przy 100mm
- Czas wymagany do podgrzania PEKK do 425 ° C wynosił 102 sekund dla grzejników wolframowych 2kW przy 55mm i 244 sekund dla elementów FFEH przy 100mm
- Czas wymagany do podgrzania PPS do 425 ° C wynosił 88 sekund dla grzejników wolframowych 2kW przy 55mm i 219 sekund dla elementów FFEH przy 100mm
- Maksymalne temperatury, osiągalne szybkości nagrzewania materiału i równomierność temperatury powierzchni są silną funkcją odległości, w jakiej grzejniki są montowane z materiału.
- Doskonałą penetrację IR, a zatem wyrównanie temperatury, przez grubość materiału, PPS i PEEK uzyskano dzięki halogenowi średniofalowemu (wolframowi). Wyrównanie temperatury osiągnięte w przypadku PEKK nie było tak dobre, jak w przypadku innych materiałów.
- Doskonałą penetrację IR i wyrównanie temperatury zaobserwowano w przypadku PEEK przy użyciu czarnych pustych elementów. Ta właściwość nie była tak dobra jak w przypadku PEKK i PPS.
W oparciu o powyższe dane testowe i bliskie oddzielenia elementu od materiału, które są wymagane do osiągnięcia temperatur wymaganych do utworzenia przedmiotowych materiałów, wydaje się, że najlepszym emiterem podczerwieni jest czarny całkowicie płaski pusty element Ceramicx 800W. Chociaż czasy do osiągnięcia wymaganych temperatur są nieco dłuższe niż grzejniki wolframowe, bliższa odległość zastosowanych elementów doprowadzi do lepszej jednorodności temperatury powierzchni. Ponadto elementy ceramiczne zostały uruchomione od temperatury pokojowej i wymagały około 12 min, aby osiągnąć poziomy operacyjne. Dlatego ten czas można znacznie skrócić przez wstępne podgrzanie elementów.
Należy również zauważyć, że wyniki te oparte są na próbkach udostępnionych do testowania (tj. O grubości 1mm i 2mm). Ogrzewanie grubszych części może wymagać zbadania znacznych zmian w technologii grzewczej, aby zapewnić, że profil temperaturowy na całej grubości materiału jest jednolity i odpowiedni do kolejnych operacji formowania.
1 Keton polieterowo-eterowy
2 Siarczek polifenylenu
3 Polieteroketonoketon
4 Średnia różnica między górną i dolną powierzchnią uzyskana w ciągu ostatnich 18 sekund testu.
Odpowiedzialność
Te wyniki testu należy dokładnie rozważyć, zanim określony typ emitera podczerwieni zostanie wykorzystany.
Powtórzone testy przeprowadzone przez inne firmy mogą nie dać takich samych wyników. Różnice w warunkach eksperymentalnych mogą zmienić wyniki. Inne źródła błędów obejmują: markę zastosowanego emitera, sprawność emitera, dostarczoną moc, odległość od badanego materiału do wykorzystanego emitera oraz środowisko. Miejsca, w których mierzona jest temperatura, mogą również powodować zmiany wyników.