АВТОР | ДАТА СОЗДАНИЯ | Версия | НОМЕР ДОКУМЕНТА |
---|---|---|---|
Доктор Питер Маршалл | 8 апреля 2016 | V1.1 | CC11 - 00101 |
Введение
CCP Gransden обратилась к Ceramicx с просьбой построить инфракрасную печь для нагрева термопластичных препрегов из углеродного волокна для операций формования. Эта работа по тестированию проводилась как часть функций, определенных в коммерческом предложении (CSP 000 008). Первый этап включает оценку и выбор инфракрасного обогревателя для этого проекта, при этом минимальная температура материала должна быть 425 ° C.
Описание материала
Три образца двух материалов были получены в виде кусков 230 x 230 x 1mm. В этих случаях матрица была PEEK1 и PPS2, Меньший образец ПЭКК3 с размерами 200 x 150 x 2mm также был получен. Материал был твердым, гладким с глянцевой черной отделкой. Небольшая картина была видна на поверхности на поверхности образцов PEEK и PPS.
Образцы PEEK и PPS были разрезаны на куски 115 x 115 мм. Материал PEKK был разрезан на куски 100 x 75mm.
Способ доставки
Были оценены два разных семейства обогревателей; галоген (QH и QT) и черная полая керамика (FFEH). В каждом случае валики были установлены выше и ниже образца материала с регулируемой высотой.
FastIR
Была изготовлена монтажная система, позволяющая устанавливать два из блоков Ceramicx FastIR 500 над и под материалом. FastIR 500 состоит из семи нагревательных элементов, установленных параллельно в корпусе 500 x 500 мм. Расстояние между этими трубами составляет 81 мм. Были использованы элементы 1500W и 2000W 'long' (общая длина: 473mm), дающие общий выходной сигнал от двух единиц 21 или 28kW соответственно. Нагреватели были установлены таким образом, чтобы расстояние между поверхностью элемента и образцом варьировалось между 55mm и 95mm.
Используемый протокол эксперимента был следующим:
- Вентиляторы включены
- Центральные три нагревательных элемента включены сверху вниз
- Снаружи включены четыре нагревательных элемента, сверху вниз
Изображение образца между двумя модулями FastIR показано на рисунке 1. Ничто не использовалось, чтобы заключить промежуток между двумя нагревательными единицами
Elements
Два элемента могут быть установлены в блоке FastIR; кварц галоген и кварц вольфрам. Эти элементы излучают различные пиковые длины инфракрасных волн; галоген при приблизительно 1.0 - 1.2μm и вольфрам между 1.6 - 1.9μm. Каждая трубка имеет диаметр 10mm, общую длину 473mm и длину нагреваемой части 415mm.
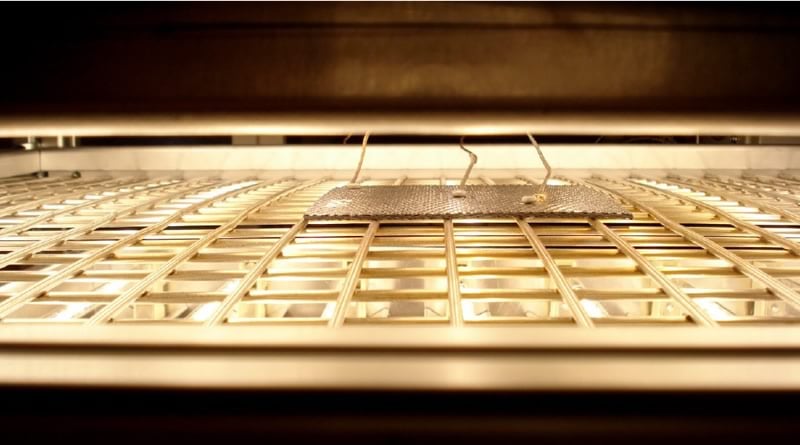
Черная полость
Специальная нагревательная плита была разработана для включения матрицы 2 x 7 элементов Ceramicx 800W FFEH, обеспечивающей мощность каждой плиты 11.2kW. Эта матрица была заключена в корпус 510 x 510mm и смонтирована в той же раме, что и система FastIR, описанная выше. Протокол эксперимента был использован; однако, поклонники не были наняты на этих плитах. Расстояние между этими элементами было 65mm.
Использовались два разных расстояния элемент-образец: 50 и 100mm. Опять же, зазор между двумя нагревательными блоками остался открытым
Elements
Черные полые элементы Ceramicx излучают пиковые длины волн в среднем и длинном режиме (2 - 10μm). Каждый элемент имеет размеры 245 x 60mm (lxw). Длинные волны, связанные с керамическими элементами, очень эффективны для нагрева многих полимерных материалов.
Измерительные приборы
Термопары типа K были прикреплены к поверхности образца с помощью винтов M3. Керамический цемент был опробован, однако он не прилипал к поверхности материала. Учитывая требуемые высокие температуры, ни один из доступных адгезивов не будет оставаться стабильным, поэтому механическая фиксация считается необходимой Термопары были расположены в центре каждого образца, а также 10mm (край) и 30mm (четверть) от края, как показано на рисунке 2. Это расположило термопары непосредственно над трубными элементами и в центре между элементами так, чтобы регистрировалась максимальная разница температур. Данные о температуре записывались с интервалом в одну секунду.
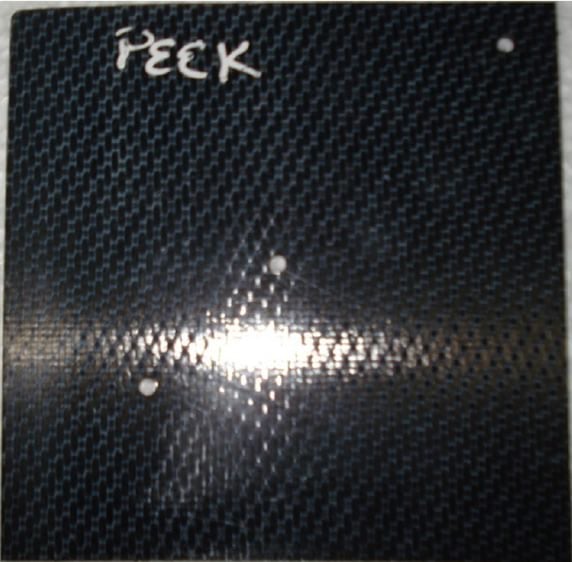
Тестирование сэндвичей
Тестер сэндвич-теста представляет собой усовершенствованную машину для испытания тепловых характеристик материала, как показано на рисунке 2. Различные типы инфракрасных обогревателей можно устанавливать в двух положениях, обращенных вертикально вверх и вниз. Это гарантирует, что тестируемый материал может нагреваться сверху и / или снизу. Четыре бесконтактных оптических пирометра используются для определения температуры верхней и нижней поверхности испытуемого материала. Эмитентам дают нагреться до их рабочей температуры, и затем материал помещают под эмиттер (ы) в течение заранее определенного периода. Это испытание было выполнено с 1kW вольфрамом (QTM) и черными полыми элементами 800W (FFEH), установленными над образцом 75mm над образцом, чтобы определить, какой нагреватель дал лучшее проникновение через материал.
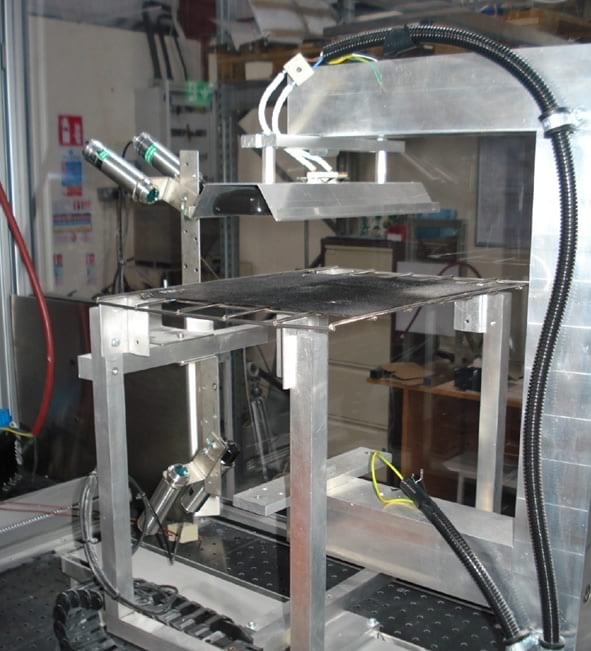
Итоги
FastIR
В этом разделе представлены результаты, полученные для вольфрамовых и галогенных трубок для трех рассматриваемых материалов. Испытания проводились с тремя различными высотами нагревателя (55 мм, 80 мм и 95 мм).
PEEK
Первоначальные испытания проводились с образцом PEEK и двумя нагревателями FastIR с кварцево-галогенными трубками 1500W, разделенными 110mm. Результаты этого теста, показанные на рисунке 4, показывают, что образец не достиг необходимой температуры.
Элементы были заменены на коротковолновые галогенные трубки (QHL) 2000W, которые показали, что при одном и том же разделении образец достигал и превышал требуемую температуру в одном месте. В этом случае максимальная зарегистрированная температура составляла 485 ° C, однако также были обнаружены значительные различия в температуре (до 83 ° C). Время, необходимое для достижения целевой температуры 425 ° C, составляло 99 секунд. Это было достигнуто только в двух местах
Кварцевые вольфрамовые (QTL) трубки (2000W) также были исследованы на трех уровнях с максимальной температурой, падающей при увеличении расстояния между нагревателями. При 55mm была обнаружена максимальная и минимальная температура 520 ° C. Целевая температура по образцу материала была достигнута в секундах 206. При увеличении расстояния до 80mm они уменьшались до 450 ° C и 415 ° C, а при 95mm над образцом максимальная и минимальная температуры образца составляли 407 и 393 ° C.
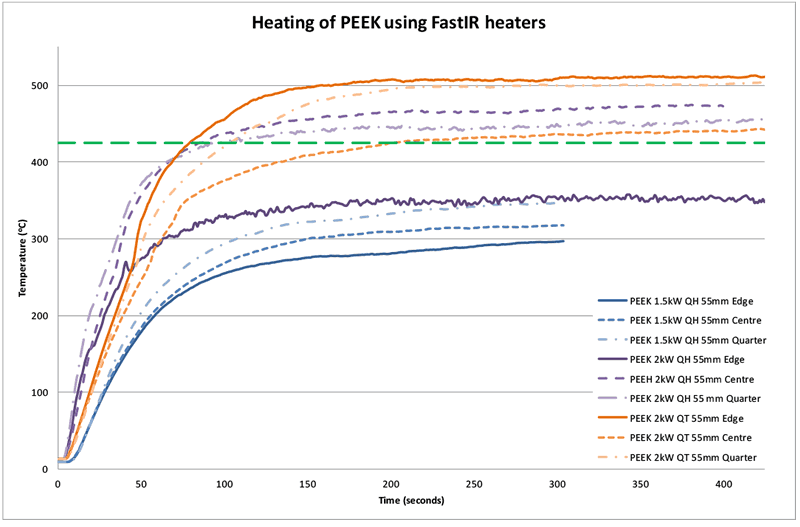
На рисунке 4 показана разница в температуре, которая может возникнуть в образце из-за непосредственной близости нагревателей к образцу, а также времени, необходимого для нагревания материала до 425 ° C (секунды 206 для нагревателя 2kW QT).
Вольфрамовые трубки 150 ° W не тестировались, так как было сочтено более важным увеличить расстояние между нагревателями, чем уменьшить мощность используемых элементов.
На рисунке 5 показана визуальная разница в образце до и после нагревания.
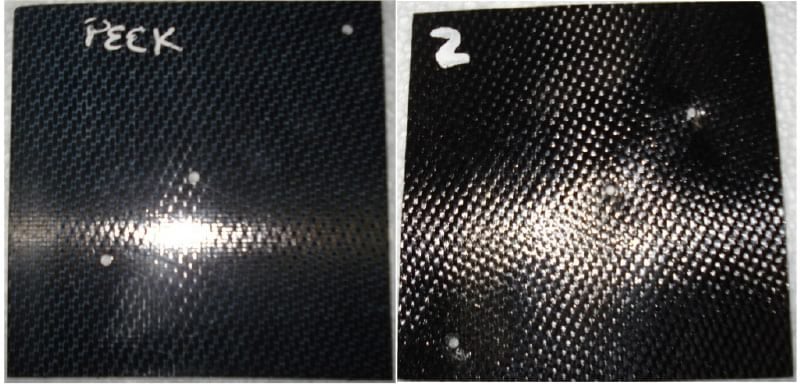
PEKK
PEKK нагревался вольфрамовыми нагревателями 2000W только на 55mm. Тепловой отклик материала был превосходным с записью температур, превышающих 500 ° C. Минимальная оговоренная температура была достигнута в секундах 102 с максимальной записанной температурой, превышающей 500 ° C.
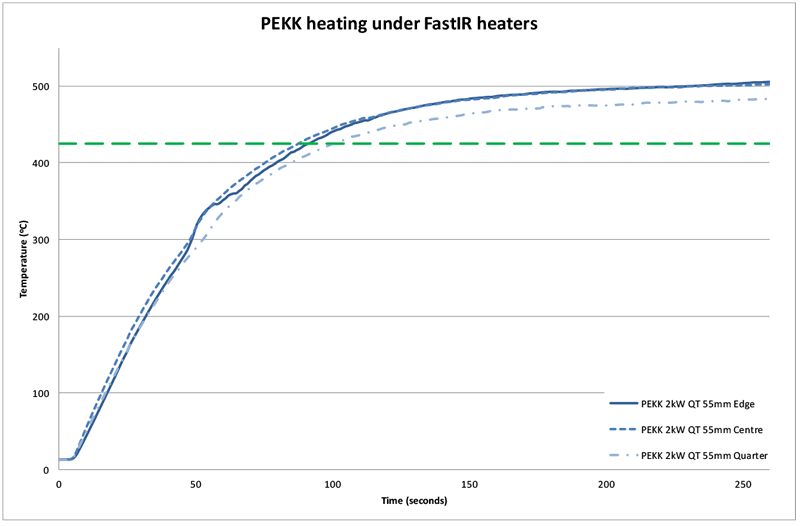
Было заметно, что этот образец, по-видимому, показал некоторое расщепление и расслоение по краям, а также некоторые искажения поверхности после нагревания, как показано на рисунке 7, возможно, из-за поглощения влаги во время хранения и произошедшего быстрого нагревания.
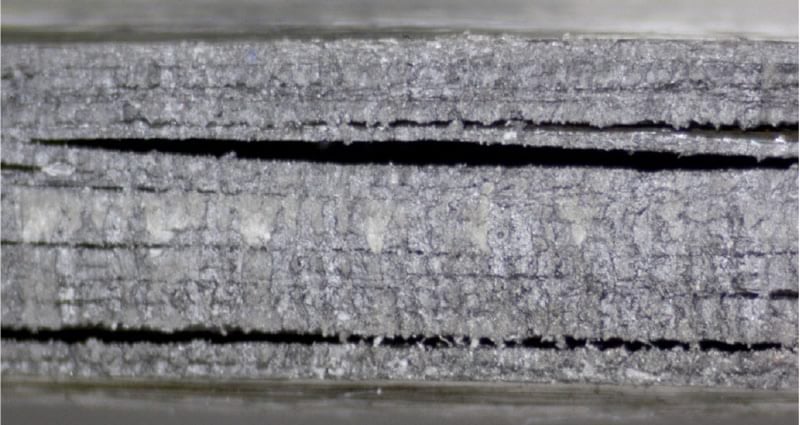
PPS
Материал PPS был испытан с галогенными и вольфрамовыми нагревателями 2000W. Тест на галоген проводился с разделением 55mm и тест на вольфрам при 55mm и 95mm.
Данные снова показали, что вольфрамовая трубка была лучшим нагревателем для этого материала (чем галогенный нагреватель) с более высокими температурами, зарегистрированными при разделении 55mm, а также с большей однородностью температуры по образцу. Изменение 38 ° C было зарегистрировано для галогенных нагревателей и 30 ° C для вольфрамовых нагревателей. Это зарегистрированное изменение будет сильно зависеть от расположения термопары относительно трубок. Одинаковые места расположения термопар не гарантируются.
Испытания с PPS были прекращены вскоре после того, как материал достиг требуемой температуры 425 ° C, поскольку из образцов было выделение паров с запахом серы.
На расстоянии 55mm заданная температура была записана через 66 и 88 секунд для галогенных и вольфрамовых нагревателей при 55mm соответственно. Когда вольфрамовые нагреватели были установлены на 95 мм от образца, заданная температура не была достигнута.
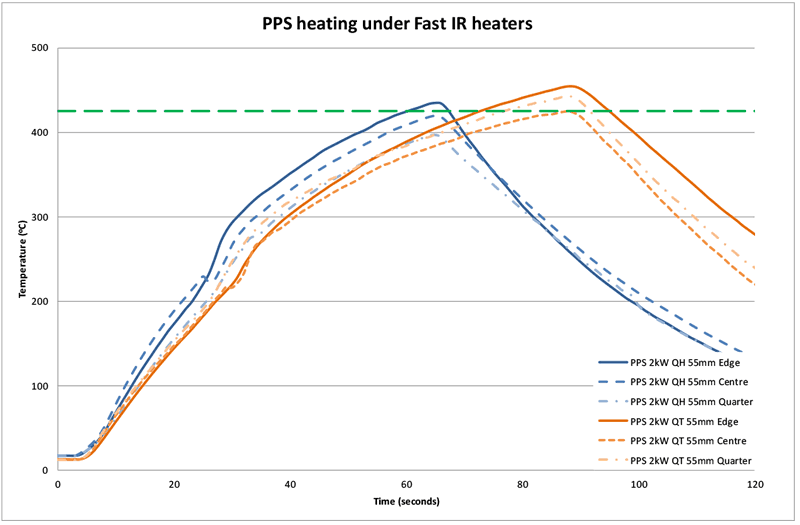
Черная полость
Первоначальные испытания проводились с разделением элемент-материал 50mm. Повышение температуры материала было очень быстрым для всех материалов. При холодном запуске полые элементы нагреваются приблизительно за 10-12 минут до стабильного рабочего уровня (температура поверхности около 700 ° C). Повышение температуры материала в целом было похоже на кривую нагрева нагревателя, однако в этом была временная задержка.
PEEK
График времени, необходимого для нагревания образца PEEK до достижения требуемой температуры обработки, показан ниже на рисунке 9. Это показывает, что время нагревания до 425 ° C составляет приблизительно 185 секунд с момента включения нагревателей со скоростью 50mm. Если расстояние увеличивается до 100mm, время увеличивается до 230 секунд. Образец оставляли между двумя плитами во время нагревания и удаляли для охлаждения.
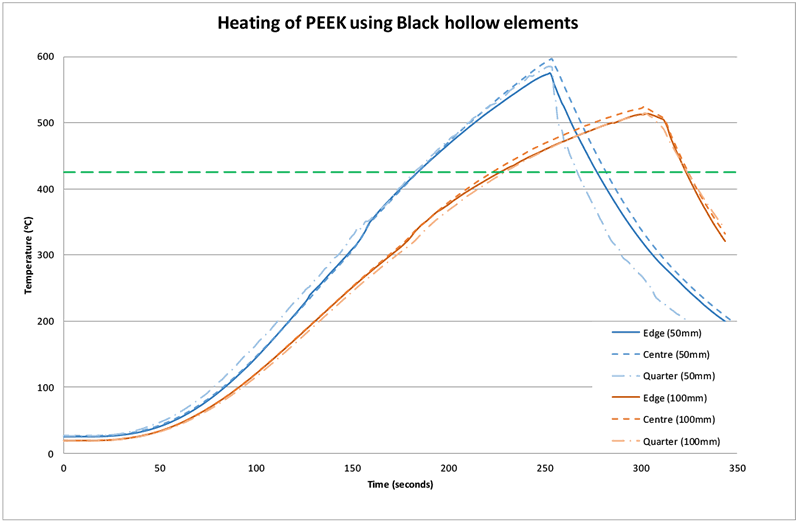
PEKK
Время, необходимое PEKK для достижения минимального порога, было немного больше, чем для PEEK. Для этого существуют две возможные причины: 1.) Материал не поглощает инфракрасное излучение, а также PEEK и 2.) Толщина материала в два раза больше (1 и 2mm соответственно). Время, необходимое для достижения 425 ° C при 50mm, составляло 181 секунд, а при 100mm оно увеличивалось до 244 секунд.
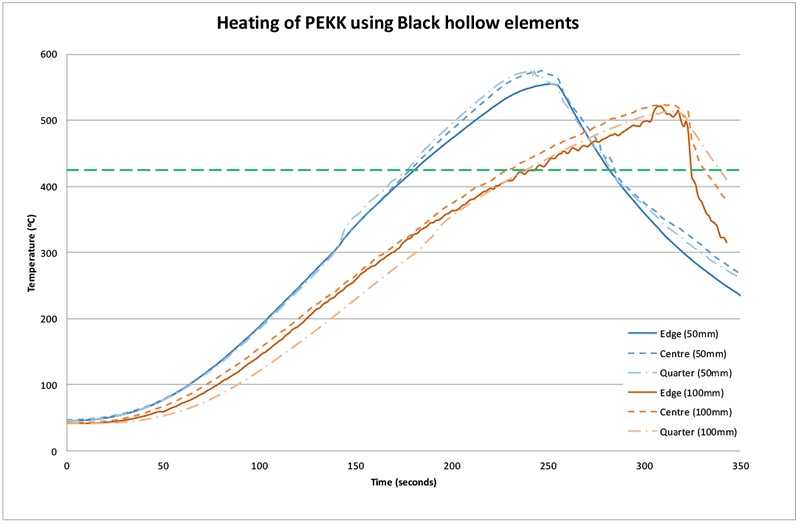
PPS
PPS очень успешно нагрелся, когда черные полые элементы с 425 ° C были записаны в секундах 171 и секундах 219 в 50 и 100mm соответственно. Кривая нагрева для этого материала показана на рисунке 11. Снова произошел выброс дыма с запахом серы, однако его количество было не таким большим, как у галогенных нагревателей, как описано выше. Частично это может быть связано с отсутствием вентиляторов на задней стороне нагревательной плиты.
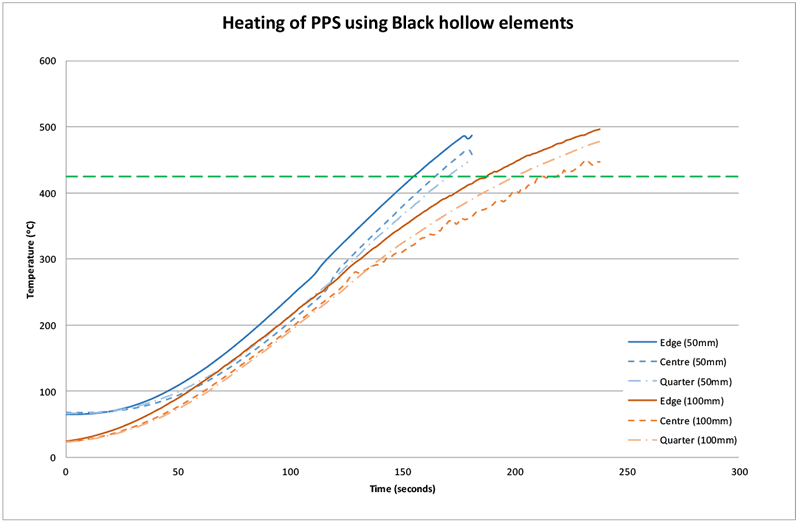
Сводка времени, необходимого для нагревания материалов с галогенными, вольфрамовыми и полыми керамическими элементами до целевой температуры, приведена ниже в таблице 1. Поскольку установка галогенных элементов на более длинных расстояниях, чем 55mm, не всегда была успешной, эти результаты были опущены в таблице.
Материалы |
Тип обогревателя (мощность)
|
Расстояние | Время достигать 425 ° C |
---|---|---|---|
PEEK | QHL (2kW) | 55 мм | 99 |
QTL (2kW) | 55 мм | 206 | |
FFEH (800W) | 50 мм | 185 | |
FFEH (800W) | 100 мм | 230 | |
PEKK | QTL (2kW) | 55 мм | 102 |
FFEH (800W) | 50 мм | 181 | |
FFEH (800W) | 100 мм | 244 | |
PPS | QHL (2kW) | 55 мм | 66 |
QTL (2kW) | 55 мм | 88 | |
FFEH (800W) | 50 мм | 171 | |
FFEH (800W) | 100 мм | 219 |
Тестирование сэндвичей
Сэндвич-тестирование проводилось для получения информации о передаче тепла через материал. Это было сделано путем нагревания образца с одной стороны, измерения температуры с обеих сторон и сравнения результатов. Были исследованы только вольфрамовые трубки и черные полые элементы, так как на основании результатов FastIR галогенные трубки с короткой волной не подходят для нагревания рассматриваемых материалов.
Результаты для элементов QTM показывают, что нет существенной разницы температур между верхней и нижней поверхностями для материалов PEEK и PPS, однако PPS нагревается быстрее и кривые для этого материала практически неразличимы. Следует отметить, что эти два материала очень тонкие (≈ 1mm). Как и ожидалось, разница температур для PEKK была больше (75 ± 2oC) из-за его толщины (≈ 2mm). Эти результаты показаны на рисунке 12 ниже.
По эксплуатационным причинам испытание прекращается, когда пирометры обнаруживают температуру 300 ° C. Пик, наблюдаемый в первые секунды 30 теста, является отражательной способностью и не является истинным показанием температуры.
Эти результаты демонстрируют, что хорошее ИК-проникновение материала возможно для PEEK и PPS с использованием нагревателя вольфрамового типа. Однако выравнивание температуры для PEKK не так хорошо, о чем свидетельствует почти 75 ° C разница температур в последние 18 секунды теста 4.
Было невозможно подвинуть образцы материала ближе к нагревателю, чтобы проанализировать, как это повлияет, так как острый угол, необходимый пирометру, чтобы увидеть материал, будет искажать показания.
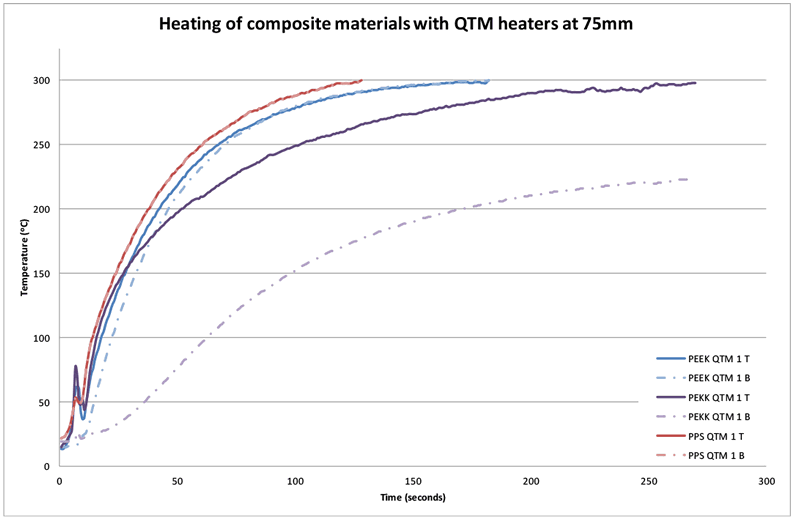
Нагрев образцов с черными полыми элементами на одинаковом расстоянии (75mm) показывает аналогичную тенденцию с большей разницей температур (45 ± 2 ° C), наблюдаемой для более толстого материала PEKK (по сравнению с более тонкими материалами). Температуры верхней и нижней поверхностей ПЭЭК практически неразличимы; однако существует разница в температуре PPS (25 ± 2 ° C). Эти данные показаны на рисунке 13. Это указывает на то, что проникновение ИК-излучения в PPS с более длинноволновым излучением не так хорошо, как с более коротким ИК-излучением вольфрама, однако температурная коррекция PEKK лучше (но не идеальная).
При сепарации 75mm самые высокие температуры и скорости нагрева получаются с использованием вольфрамового нагревателя, что, по-видимому, противоречит предыдущим результатам плиты. Это, однако, не должно использоваться в качестве ориентира, поскольку использовался только один нагреватель. Кроме того, эти характеристики будут улучшены за счет использования ряда нагревателей, а не одного нагревателя.
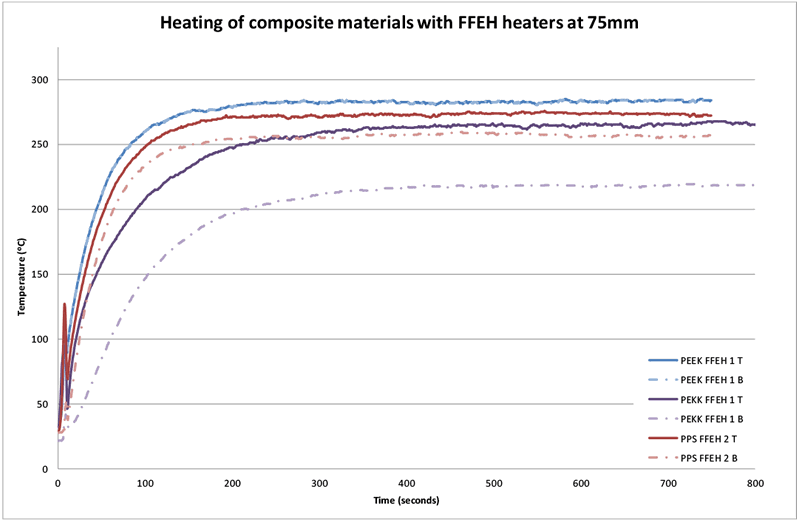
Заключение
- Проведенные и подробно описанные выше испытания показывают, что нагрев трех термопластичных углеродных композиционных материалов до минимума 425 ° C возможен как со средневолновыми галогенными, так и с полыми черными элементами.
- Более высокие максимальные температуры достигаются при использовании черного полого элемента Ceramicx 800W (FFEH).
- Время, необходимое для нагревания PEEK до 425 ° C, составляло 206 секунд для нагревателей из вольфрамовой трубки 2kW при 55mm и 230 секунд для элементов FFEH при 100mm
- Время, необходимое для нагревания PEKK до 425 ° C, составляло 102 секунд для нагревателей из вольфрамовой трубки 2kW при 55mm и 244 секунд для элементов FFEH при 100mm
- Время, необходимое для нагревания PPS до 425 ° C, составляло 88 секунд для нагревателей из вольфрамовой трубки 2kW при 55mm и 219 секунд для элементов FFEH при 100mm.
- Максимальные температуры, достижимые скорости нагрева материала и однородность температуры поверхности сильно зависят от расстояния, на котором нагреватели установлены из материала.
- Отличное проникновение инфракрасного излучения и, следовательно, выравнивание температуры по толщине материала PPS и PEEK было достигнуто с помощью средневолнового галогена (вольфрама). Выравнивание температуры, достигнутое с PEKK, было не так хорошо, как с другими материалами.
- Превосходное проникновение инфракрасного излучения и выравнивание температуры были замечены с PEEK с использованием черных полых элементов. Это свойство было не так хорошо, как для PEKK и PPS.
Исходя из приведенных выше данных испытаний и близкого разделения элементов и материалов, которые необходимы для достижения температур, требуемых для формирования рассматриваемых материалов, представляется, что лучшим инфракрасным излучателем является черный полый плоский элемент Ceramicx 800W. Хотя время достижения требуемых температур немного больше, чем у вольфрамовых нагревателей, более близкая близость используемых элементов приведет к лучшей однородности температуры поверхности. Кроме того, керамические элементы были запущены при комнатной температуре и потребовали приблизительно 12 минут для достижения эксплуатационных уровней. Следовательно, это время может быть значительно сокращено путем предварительного нагрева элементов.
Следует также отметить, что эти результаты основаны на образцах, которые были предоставлены для испытаний (то есть толщина 1mm и 2mm). Нагрев более толстых деталей может потребовать значительных изменений в технологии нагрева, чтобы исследовать, чтобы гарантировать, что температурный профиль по толщине материала является однородным и пригодным для последующих операций формования.
1 Полиэфирэфиркетон
2 Полифениленсульфид
3 полиэфиркетонкетон
4 Средняя разница между верхней и нижней поверхностями, взятая за последние 18 секунд теста.
Отказ от ответственности
Эти результаты испытаний должны быть тщательно рассмотрены, прежде чем определяться для использования определенного типа инфракрасного излучателя.
Повторные тесты, проводимые другими компаниями, могут не достичь тех же результатов. Различия в условиях эксперимента могут изменить результаты. Другими источниками ошибок являются: марка используемого излучателя, эффективность излучателя, подаваемая мощность, расстояние от испытуемого материала до используемого излучателя и окружающая среда. Места, в которых измеряется температура, также могут вызывать различия в результатах.