YAZAR | TARİH OLUŞTURULDU | VERSION | BELGE NUMARASI |
---|---|---|---|
Conor Newman | 18 Temmuz 2018 | V1.1 | CCII-00129 |
Giriş
Bir şirket, kür sonrası kompozit bir parçanın yüzeyini ısıtmakla ilgilenmektedir. Parça, 230 saniye içerisinde yaklaşık 15 ° C'ye ısıtılmalıdır.
Malzemeler
Bu testteki sertleşmiş kompozit, genel boyutları 250mm x 130mm x 3.8mm olan bir karbon fiber takviyeli epoksi reçinesidir.
Isıtıcılar
Her test için çeşitli ısıtıcılar kullanıldı:
- 6 x 800W siyah FFEH (Seramik tam düz eleman boş) Watt yoğunluğu = 44.8 kW / m2
- 4 x 2kW QTL tüpler (Kuvars tungsten) Watt yoğunluğu = 56 kW / m2
- 4 x 1.5kW QHL tüpler (Kuvars halojen) Watt yoğunluğu = 42 kW / m2
Yöntem
Kompozit malzeme, belirli bir dizi ısıtma elemanının altına yerleştirildi. Kompozitin üst tarafı, elemanlar tarafından doğrudan ısıtıldı ve yüzey sıcaklığını kaydetmek için kompozitin üst tarafına sabitlenmiş bir takım K tipi termokupllar. Referans için alt yüzeye bir t / c K yerleştirildi. Deneysel kurulum şekil 1'te görülebilir.
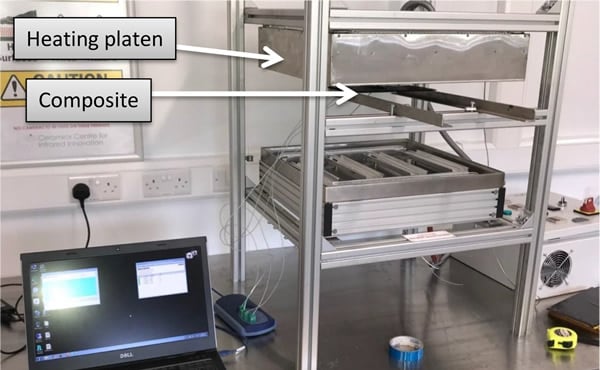
Sonuçlar
Çeşitli testlerden elde edilen tüm sonuçlar, bu bölümde hem grafik olarak hem de tablo halinde gösterilir.
Şekiller 2, 3 ve 4, kompoziti 100 mm'lik bir mesafede ısıtmanın sonuçlarını gösterir.
Seramik FFEH ile, kompozit, 227 saniye içinde maksimum bir 40 ° C sıcaklığına ulaştı.
- QTL tüplerde, kompozit, 200 saniye içerisinde maksimum bir 65 ° C sıcaklığına ulaşmıştır.
- QHL tüpleriyle, kompozit, 170 saniye içerisinde maksimum bir 80 ° C sıcaklığına ulaştı.
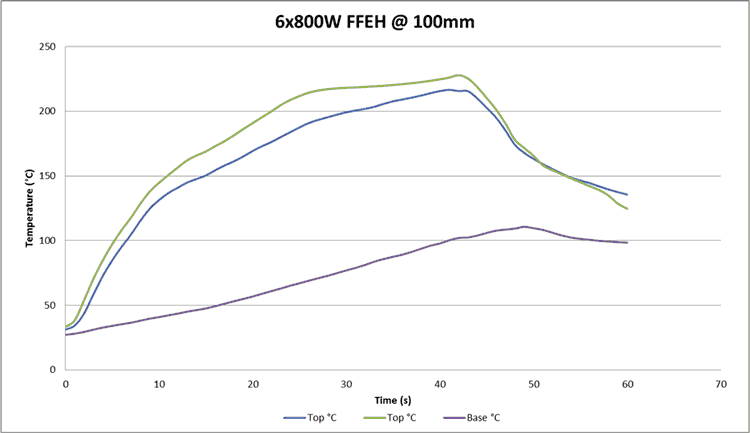
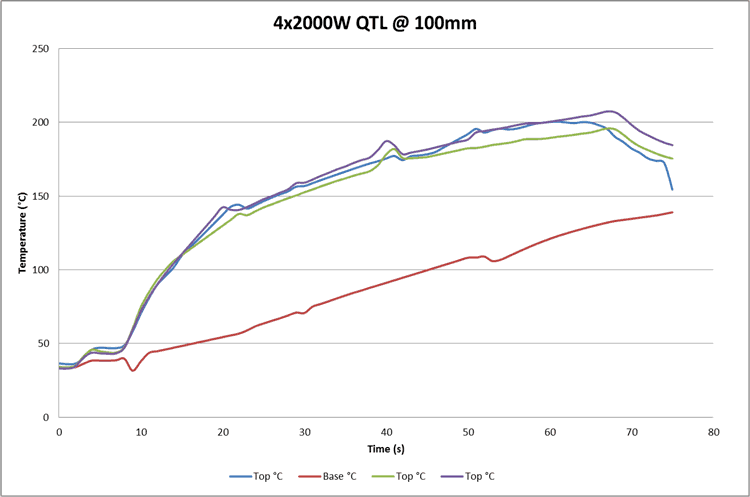
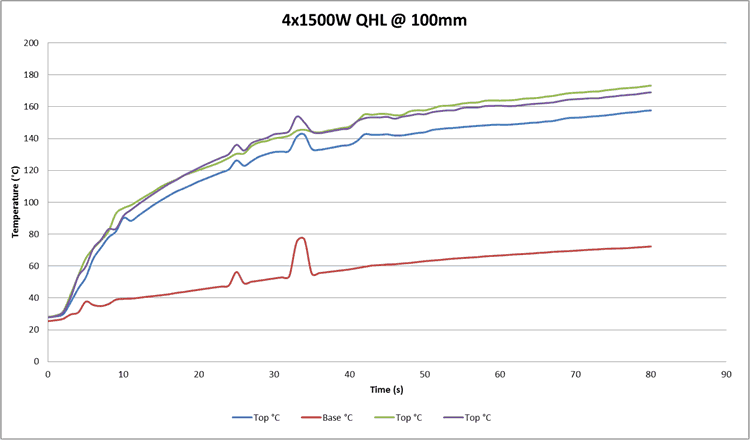
Bu sonuçları elde ettikten sonra, uzun dalga seramik elemanlarının bu kompozitin yüzeyini ısıtmak için en uygun olduğu açıktı. Bununla birlikte, element ile kompozit arasındaki mesafenin, 230 saniye içinde gerekli olan 15 ° C ısıtmasını sağlamak için azaltılması gerekecektir.
Şekil 5 ve 6, azaltılmış mesafe testlerinden gelen sonuçları göstermektedir.
- 60mm'de, kompozit, 280 saniye içinde maksimum bir 30 ° C sıcaklığına ulaştı. 230-16 saniye içinde 18 ° C'ye ulaştı.
- 50mm'de, kompozit, 350 saniye içinde maksimum bir 25 ° C sıcaklığına ulaştı. 230-12 saniye içinde 14 ° C'ye ulaştı.
250 ° C'den daha yüksek aksiyonların, termokuplları yerinde tutan yüksek sıcaklık bandının erimeye başladığına ve potansiyel olarak çarpıklıklara neden olduğuna dikkat edilmelidir.
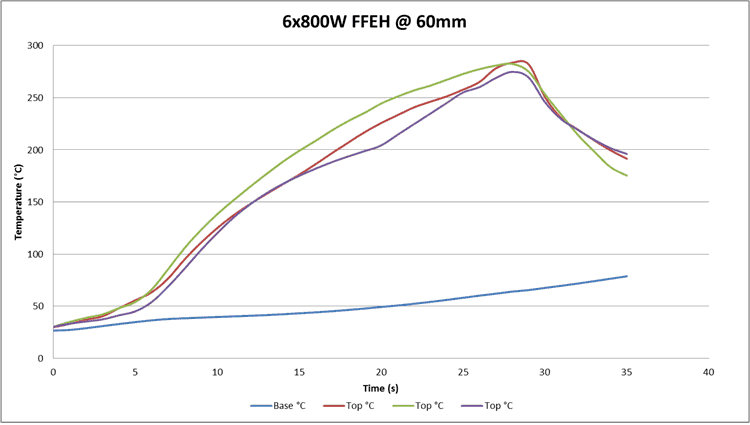
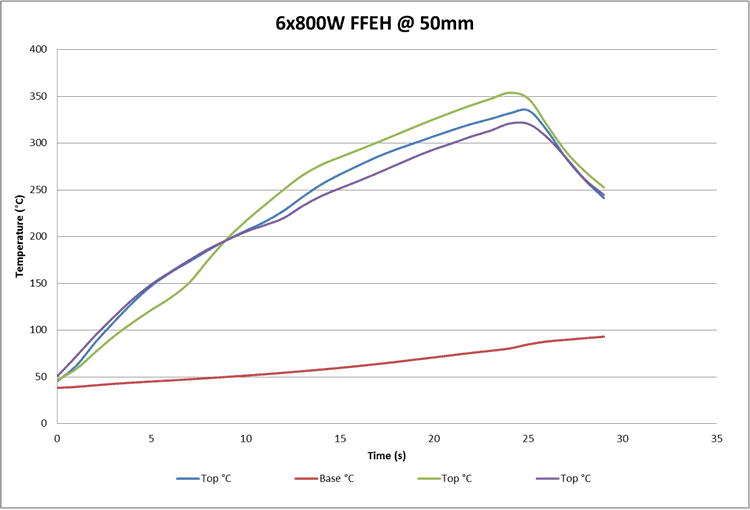
Tablo 1, testin tamamındaki sonuçları sıralar. Bu, 6mm'in kompozitin üstünde bulunan bir 800 x 50W siyah FFEH eleman dizisinin, müşterilerin ısıtma tarifinin gereksinimlerini karşılamak için yeterli olduğunu belirtir.
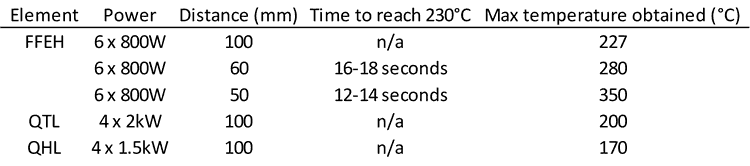
Sonuç
- Her bir ısıtma elemanı tipinin (seramik içi boş, quart tungsten, kuvars halojen) sabit bir mesafede (100mm) test edilmesinden sonra, seramik deliklerinin bir kompozitin yüzeyini ısıtmak için en uygun olduğu tespit edildi.
- QTL ve QHL tüpleri, kompozitin alt kısmının daha iyi ısıtılmasını sağlamıştır. Bu, beklenen kısa dalgalı elementler, bir kompozitin kürlenmesinde, nüfuz edici ısıtma sağlamak için kullanıldığından beklenmekteydi.
- Seramik (uzun dalga) elementleri, kompozitin üst yüzeyini ısıtmak için termal radyasyonun çoğunu genişletti.
- 100mm, elemanlarla kompozit arasındaki mesafeye, istenen sıcaklığa ulaşmak için çok büyüktü. 50mm uygun bir mesafeydi.
Feragatname
Bu test sonuçları, bir işlemde hangi tür kızılötesi yayıcının kullanılacağına karar vermeden önce dikkatlice düşünülmelidir. Diğer şirketler tarafından tekrarlanan testler aynı bulguları elde edemeyebilir. Kurulum koşullarını ve sonuçları değiştirebilecek değişkenleri sağlamada bir hata olasılığı vardır; kullanılan vericinin markası, vericinin verimliliği, sağlanan güç, test edilen malzemeden kullanılan vericiye olan mesafe ve çevre . Sıcaklıkların ölçüldüğü yerler de farklı olabilir ve bu nedenle sonuçları etkiler.