AUTHOR | DATE CREATED | VERSION | DOCUMENT NUMBER |
---|---|---|---|
Conor Newman | 9 July 2019 | V1.1 | CC11 – 00152 |
Introduction
Two tests were implemented for the purpose of this report:
- Test 1 compares the performance of a 2 standard FFEH 800W (running at 400W each) when paired with various reflectors, and in turn when fitted with various grills as seen in an IRP4
- Test 2 quantifies the ability of an IRP4 to heat a concrete slab from a set distance. It also moniters the internal and surface temperatures of the IRP4.
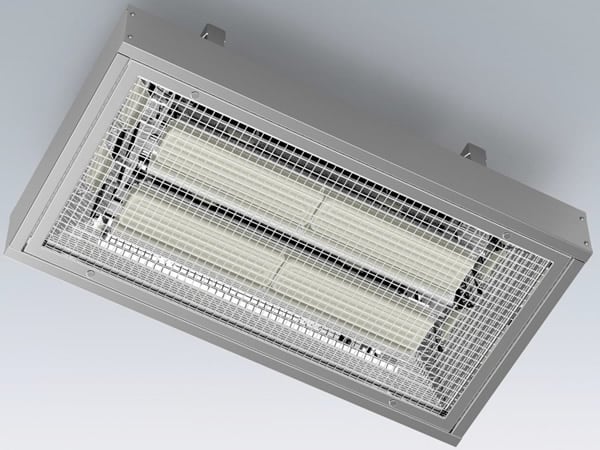
Test 1
The first test was carried on in Ceramicx’ Herschel heat flux robot. Two standard FFEH 800W elements were paired with three separate RAS 2 reflectors, and the emitted heat flux was mapped. The elements were a distance of 200mm from the sensor. It was determined that the aluminised steel reflector outperformed both the stainless steel and the bronzed stainless steel by approximately 6%.
The results were as follows:
Once the aluminised steel was determined as the optimum reflector, the Herschel was once again use, this time placing a grill in front of the elements. It was found that a stainless steel or a bronzed stainless steel grill would reduce the performance of the FTE by 20%, and the black coated stainless steel grill would reduce said performance by 26%.
The results were as follows:
Test 2
A concrete slab (dimensions 400mm x 200mm, 15mm thick) was placed on the tiled floor, 2.7m directly below the IRP4. A type K thermocouple was attached to the slab and the temperature was recorded. The tests were run for in excess of 6 hours. The following results were noted:
- The 1000W FTE set resulted in the highest slab temperature. The slab reached a temperature of 28°C.
- The 650W FTE and 800W PFQE yielded similar results, a slab temperature of approximately 26°C.
- Both FFEH sets, 800W and 600W led to the poorest results, slab temperatures of 24.5°C and 22.5°C respectively.
The results are displayed graphically in the figure below:
The internal and back surface temperatures were recorded while the IRP4 was in operation. The following results were observed:
- When fitted with either 4x650FTE,4x600FFEH,4x800WFTE,or4x800WPFQE, the internal temperature at the measured point ranged between 150-180°C, and the back surface ranged between 85-105°C.
- When fitted with 4 x 1000W FTE, the internal and back surface temperatures recorded were 240°C and 115°C respectively.
The results are displayed graphically in the figure below:
Conclusions
- Test 1 provides clear data highlighting the superior performance of an aluminised steel reflector when compared to stainless steel reflectors. The aluminised steel reflector outperformed both the stainless steel and the bronzed stainless steel by approximately 6%.
- The stainless steel grill, both standard and bronzed by heat treating, performed better than the black coated reflector. This was expected due to the high emissivity of a black coated surface. It was found that a stainless steel or a bronzed stainless steel grill would reduce the performance of the element by 20%, and the black coated stainless steel grill would reduce said performance by 26%.
- When used exclusively to heat a concrete slab 2.7m below the IRP4, the 4 x 1000W FTE array performed best. This was expected due to the higher power. However, when comparing FTE performance to FFEH performance within an IRP4, the FTE performed noticeably better. Further works will be carried out to better analyse these differences in performance.
- As expected, the internal and back surface temperatures were much higher when using the high powered 1000W FTE. Consideration would have to be given to the max operating temperatures of the IRP4’s internal components should high powered elements be used. FFEH elements resulted in marginally lower temperatures than the FTE’s.
- From a performance standpoint, the 800W PFQE elements in the IRP4 went largely unnoticed throughout these tests. The results were neither particularly high nor low with respect to the ceramic elements. The potential future benefits of using quartz elements in an IRP4 appear to be purely aesthetic.
Disclaimer
These test results should be carefully considered prior to a determination on which type of infrared emitter to use in a process. Repeated tests conducted by other companies may not achieve the same findings. There is a possibility of error in achieving the set-up conditions and variables that may alter the results include the brand of emitter employed, the efficiency of the emitter, the power supplied, the distance from the tested material to the emitter utilised and the env