Thermoforming expansion
There’s a growing trend in the US, which is seeing thermoforming as a cost-effective alternative to injection moulding. Taking advantage of this shift in processes, one of Modern Machinery’s existing customers needed to expand their current thermoforming system to increase their thermoforming output of swimming pools for rehabilitation therapy and hot tubs.
Calling on the experience of their trusted supplier, Modern Machinery designed, engineered, and assembled an integral part of possibly the largest shuttle thermoforming machine systems in North America.
Ceramicx infrared technology
While the thermoformer customer using this shuttle machine already has a custom-built system from Modern Machinery using quartz heating technology, for this project, they wanted to take advantage of ceramic-based infrared technology.
With a work area measuring 9′ x 23′ (2.7m x 7m), the custom-built Modern Model 9’23’SS (Single Station Shuttle) vacuum forming machine consists of a top and bottom platen, each measuring 11′ x 24′ (3.4m x 7.3m).
And, sourced through our North American distributor, Weco International, the system uses 754 Ceramicx FTE ceramic infrared heating elements fitted in each platen. That makes 754 individual heating zones wired for 2 elements per zone of percentage control through the custom PLC operating system.
Increased productivity
Having developed our working relationship with Modern Machinery over recent years, Ceramicx and Weco have supplied much of the infrared heating technology used in their custom-built machines. More of Modern’s customers, including this one, are moving from standard injection moulding processes to thermoforming, so it seems the best days of this application are ahead.
Thermoforming offering the advantages of lower part weight, lower cost tooling, and a better finish for many large parts with low production volumes. This is a good sign for plenty of manufacturing sectors in the US as they look to increase their productivity while lowering their costs.
Ceramicx and Weco are only too happy to help customers in their advancement of infrared heating technology and we look forward to supplying products for more US and global markets in the coming years as the trend for thermoforming continues.
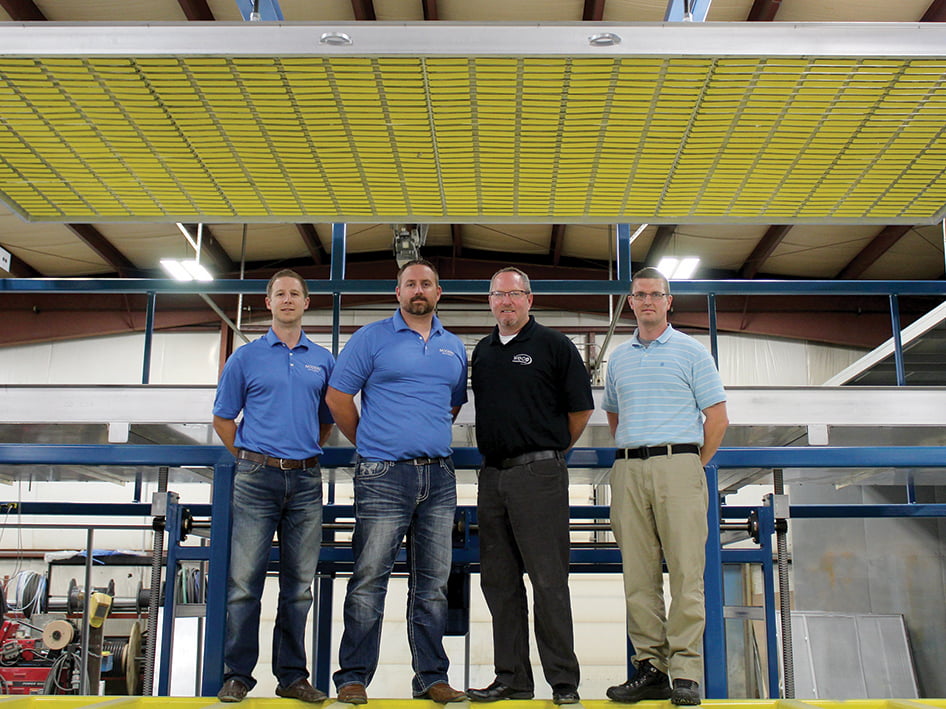