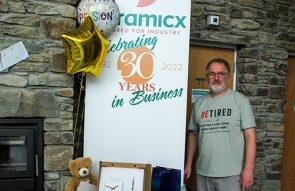
A Fond Farewell, A Warm Welcome Back and an Exciting New Chapter
David has played a pivotal role in shaping Ceramicx brand over the years – spearheading the launch of the company
Switch to our dedicated infrared solutions website for more information on industrial infrared ovens and services.
David has played a pivotal role in shaping Ceramicx brand over the years – spearheading the launch of the company ... Read moreA Fond Farewell, A Warm Welcome Back and an Exciting New Chapter
Home Information Media Media Blog
David has played a pivotal role in shaping Ceramicx brand over the years – spearheading the launch of the company
Chinaplas is an annual exhibition for the plastics and rubber industries which rotates location annually, between Shanghi in East China
Following the retirement of Frank Wilson, Ceramicx would like to announce the appointment of Paddy Martin as Managing Director. Paddy
Frank Wilson retired from his role as Managing Director at Ceramicx this week after 33 years at the helm of
Ceramicx Ltd a member of the NIBE group of companies invested in 2024 in the most modern equipment available to
Over the past two years a revolutionary world first has been steadily established at Infrared (IR) heating specialist Ceramicx. The
Please note will close for our Christmas Holidays at 4.00 pm on Friday 20th of December and re-open
Ceramicx wish our customers and friends around the world a very happy St Patrick’s Day. St. Patrick’s Day, Friday 17th
Wishing all our customers, suppliers, employees and friends a wonderful Christmas. Please note will close for our Christmas Holidays at
Get in touch with our infrared heating experts today
Signup
Register