Over the past two years a revolutionary world first has been steadily established at Infrared (IR) heating specialist Ceramicx.
The benefits to Ceramicx customers have been many and varied: The company has targeted investment in pressure casting systems, together with innovative technology in machining, mould tool design and new investment in laboratories and environmental testing. Ceramicx has now successfully traded the craft variability of bench casting for the precision of pressure casting based systems.
Sometimes in manufacturing it takes a sudden opportunity to trigger a quantum leap in quality or quantity. For Ceramicx both issues came at the same time when a leading Tier 1 automotive lighting supplier asked for a new-design volume product – a low voltage IR DC heater to de-ice headlights with LED lighting.
Ceramicx has long taken pains to put its customer at the forefront of all development projects including major advancements in ceramic technical parts, including the use of moulded in dust pressed parts with pressure casted technical parts. These projects typically develop and advance the art and science of IR heat work for well-defined and practical outcomes.
Having successfully completed its baptism of fire on a number of new designs and with these new projects Ceramicx quickly realised that its new pressure casting capabilities could be expanded to handle the bread and butter of the company’s core business in manufacturing IR heating elements, coupled with designing and building engineered combinations of the same.
Five pressure casting machines were accordingly installed over a period of time: moving the bulk of Ceramicx element production from manual bench casting towards automated and semi-automated industrial production.
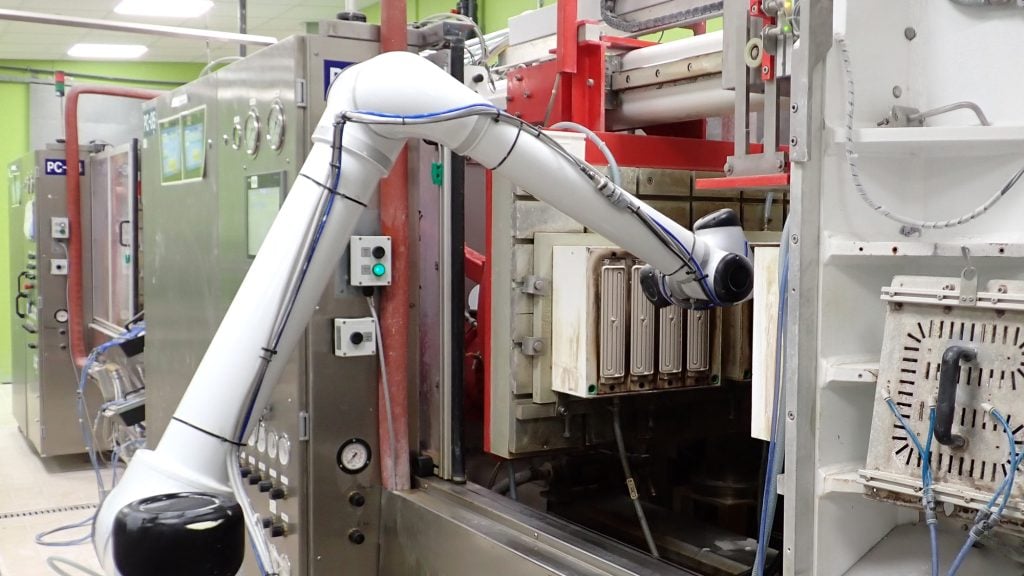
The new Ceramicx industrial pressure casting production system is today defined by a consistent flow of slip (ceramic material) that is regularly tested and constantly supplied to machine production.
State-of-the-art pressure casting machinery helps to eliminate human error and guarantees consistency in the moulded product.
Optimising air and water systems together with the in-house design and production of precision moulds also gives Ceramicx optimal control over the ceramic-based IR heating elements manufactured by the company.
A highly trained Ceramicx team keeps the pressure casting operation running smoothly. The company can now flex its modus operandi depending on the status of the order book; allowing industrialised ceramic element production.
As a result of in-house investment and increased capacity, replacing resin moulds to accommodate any new order is a very quick task. It is machine installed, reliable and cost effective, allowing Ceramicx to mix and match different elements throughout the working shift when necessary. The factory is built for development and research that is optimised for the specific needs of its customers.
Ceramicx also listened to its customer base when establishing the new product range from the pressure casting systems: For example, there was demand for a stronger and separate ‘pillar’ build from the main IR heating elements – vitrified and mechanically strong, accurate and insulative.
In response, Ceramicx now has a dedicated pressure casting machine specifically for pillar production – and has designed and engineered bespoke workstations for the wiring of those pillars before fitting them to the IR elements in a separate operation.
Each pressure casting production cell now includes:
- A pressure caster operative – who is responsible for controlling the machine and its output, also with maintaining the flow and the placements of elements.
- Wiring stations – where operators work with machines specially designed by Ceramicx that not only enhance precision with the placement of coils but can also be adjusted to suit all combinations of wattage and voltage.
- -An assembly area – where a highly trained level of focus and attention to detail is required.
There are numerous benefits to the pressure casting revolution at Ceramicx: Unlike bench casting, the semi-automated nature of the process diminishes the possibility of human error considerably.
Instead, the pressure casting machine in combination with the precision moulds, performs all the work, ensuring uniformity in every piece and providing a solid foundation for IR heating elements made to tight tolerances. If a larger quantity of elements is suddenly needed at a faster rate, the new facilities – when combined with the skilled operators – provide the flexibility to achieve industrial production with minimal disruption.
At the time of writing the vast majority of Ceramicx products are now manufactured using the pressure casting process. These elements include: FTE, HTE, FFEH, HFEH, QFEH, SFEH, SFSE-LN and the recently developed ESE bulb range.
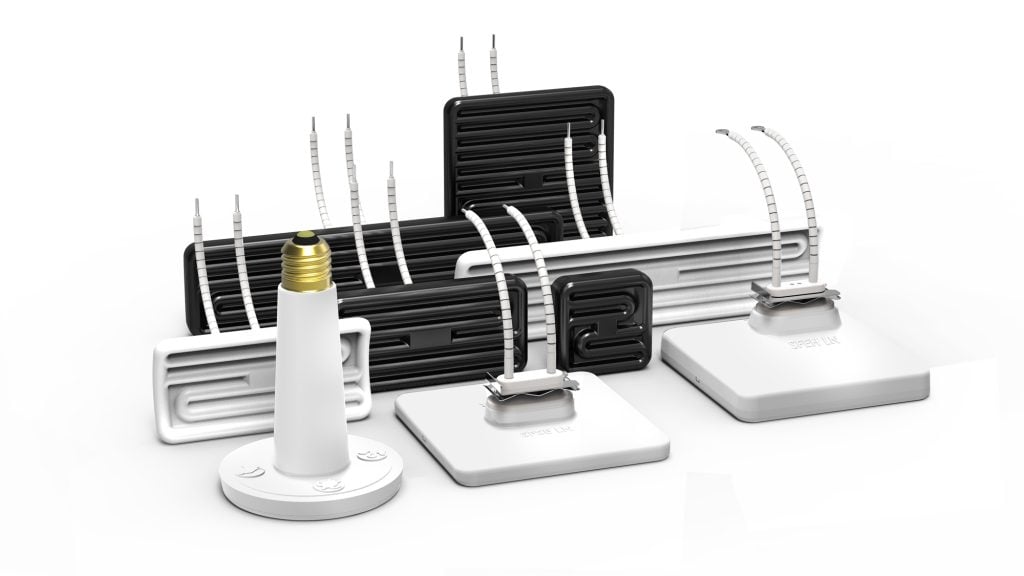
The net result of all such core production changes – accounting for an investment of some 2.4 million Euros in the past four years – has been to elevate Ceramicx above the competition. The reliability of supply, design, consistency of part and increased productivity has all helped to stabilise the supply side – while also producing a technically advanced, quality product at an extremely competitive price.
Ceramicx can now make IR heating products bespoke for designers and customers at the start of any project: discuss shapes and ideas for parts and elements; get the tools designed, prototyped and built in-house, get the products checked, environmentally tested and into full production in a matter of weeks – all under the Ceramicx roof at a very effective cost.
The Ceramicx design process begins with the assistance of Advanced CAD Software such as Solidworks in addition to other mechanical and electrical design tools used by the Ceramicx team. Once the initial design is ready, Ceramicx creates a 3D-printed prototype via additive manufacturing. This prototype is reviewed by the company’s quality and production teams, and if necessary, with the customer, in order to ensure it meets all requirements and expectations.
After finalizing the design, Ceramicx proceeds with creating all further technology, working from the master mould. Ceramicx uses a special engineering polymer to create the master mould to ensure a high-quality surface and excellent stability.
Once the design phase is complete, the focus shifts to the tool room: An expert tool making team – equipped with high-precision DMG Mori machines – then casts the resin-based mould. The Ceramicx tool room operates both morning and evening shifts to ensure the process is error-free and efficient.
When these products first come off the pressure casting line Ceramicx tests their fitness for purpose, thanks to the company’s purpose-built laboratory. This facility – now established for ten years – has a dedicated workforce, houses an automated test machine, an environmental test chamber and many other devices that simulate all conditions in the field.
The environmental test chamber, for example, operates temperatures from -50 to +190 °C with humidity (%) 0 to 100%
The Ceramicx test chamber is typically used for IR heatwork in:
Testing de-icing heaters (for automotive OEMs), simulating drying conditions for different materials and element testing under extreme conditions(e.g. A standing start at -25°C)
Every industrial innovation carries a disruption factor and a cost, and Ceramicx has certainly endured its growing pains in matching the pressure casting vision to its fundamental IR heat work over the past three years.
The results, however, are definitely worth the wait. The benefits of pressure casting processes over traditional craft production have been proven to be crystal clear.
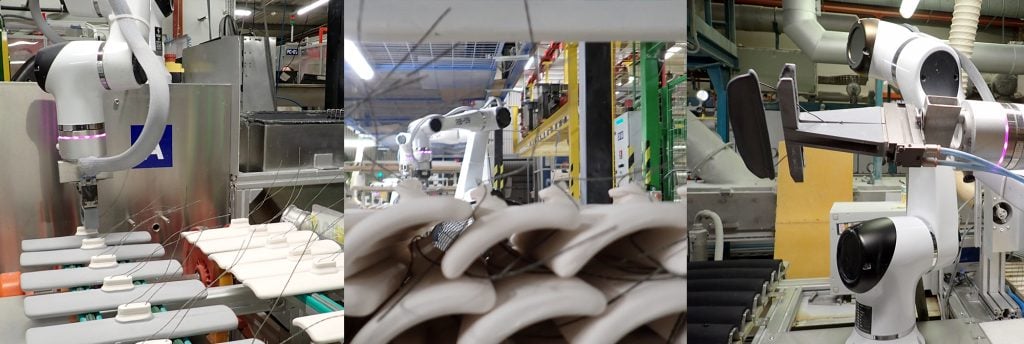
Having made the technology leap, Ceramicx once again leads the way in IR heat work. All Ceramicx customers are set to benefit in every way.
Ceramicx Pressure Casting – The Benefits:
- Improved product quality
- Improved production throughput
- Quick part design, testing and production of custom-made parts
- JIT delivery of stock products – including ISO and UL qualified
- Short lead times for non-standard products
- International service and support
- Customer focus throughout