What is the super-deduction tax break?
At the budget in April, we heard the announcement of a £25bn tax break aimed at encouraging UK business investment. By helping businesses cut their tax bill by up to 25p in every £1 invested in plant and machinery, the scheme helps firms invest in equipment to boost growth after a COVID-19-challenged year. The scheme is split into two parts:
- A 130% super-deduction capital allowance on plant and machinery investment
- A 50% first-year allowance for qualifying special rate assets
It’s hoped the super-deduction corporation tax relief scheme – which is available for business expenses on “qualifying plant and machinery investments” from 1st April 2021 to 31st March 2023 – will not only increase UK business investment over the next two years but will also increase the overall amount of investment as well.
How does the super-deduction work?
As we know, most tax issues can be confusing, but this scheme is relatively straightforward. Your plant and machinery need to be purchased between 1st April 2021 and 31st March 2023 to qualify and a fact sheet from the government gives us an example of how it works:
“A company incurring £1m of qualifying expenditure decides to claim the super-deduction. Spending £1m on qualifying investments will mean the company can deduct £1.3m (130% of the initial investment) in its taxable profits. Deducting £1.3m from taxable profits will save the company up to 19% of that – or £247,000 – on its corporation tax bill.”
What equipment can you claim for?
There are always rules, terms, and conditions that apply for any kind of tax-related scheme and this one’s no different. But the terminology used is far-reaching, and with most physical assets in any business classed as ‘plant and machinery’ for capital allowance purposes, it’s likely your business can take advantage.
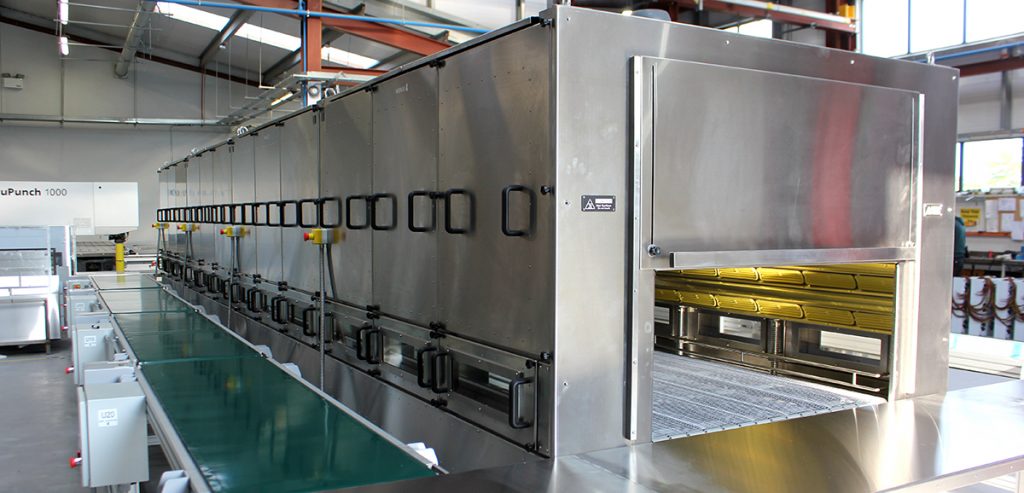
Whether you claim the full 130% super-deduction or the 50% allowance for qualifying special rate assets, the key requirement to qualify for the deduction is that all equipment purchased is new and unused. Any expenditure on second-hand equipment won’t be eligible.
Investment in Ceramicx infrared
The introduction of this corporation tax relief scheme will certainly open doors for many businesses, as the new tax year is still in its infancy, it gives you the opportunity to consider your CAPEX business spending for the next two years. By making a solid investment into machinery that might not otherwise have been possible thanks to recent events, you can now maximise your super-deductions.
With the continuing advancement of infrared technology, Ceramicx infrared heat solutions are increasing in popularity across varied manufacturing sectors and differing applications. As the original alternative energy, infrared is not only cost-effective and energy-efficient but will help your business to take steps towards a cleaner, greener, and decarbonised future.
With that in mind, there’s no better time to discover how this pioneering heat source can transform your processes and move your business forward.
Enquire with us today on what equipment you need.